一、蜗杆传动的失效形式
(一)齿廓间相对滑动速度Vs
在蜗杆传动中,蜗杆蜗轮的啮合齿面间会产生很大的相对滑动,滑动速度Vs方向沿蜗杆螺旋线的切线方向,如图所示,v1、v2分别代表蜗杆和蜗轮分度圆上的圆周速度,v1和v2互相垂直,则相对滑动速度
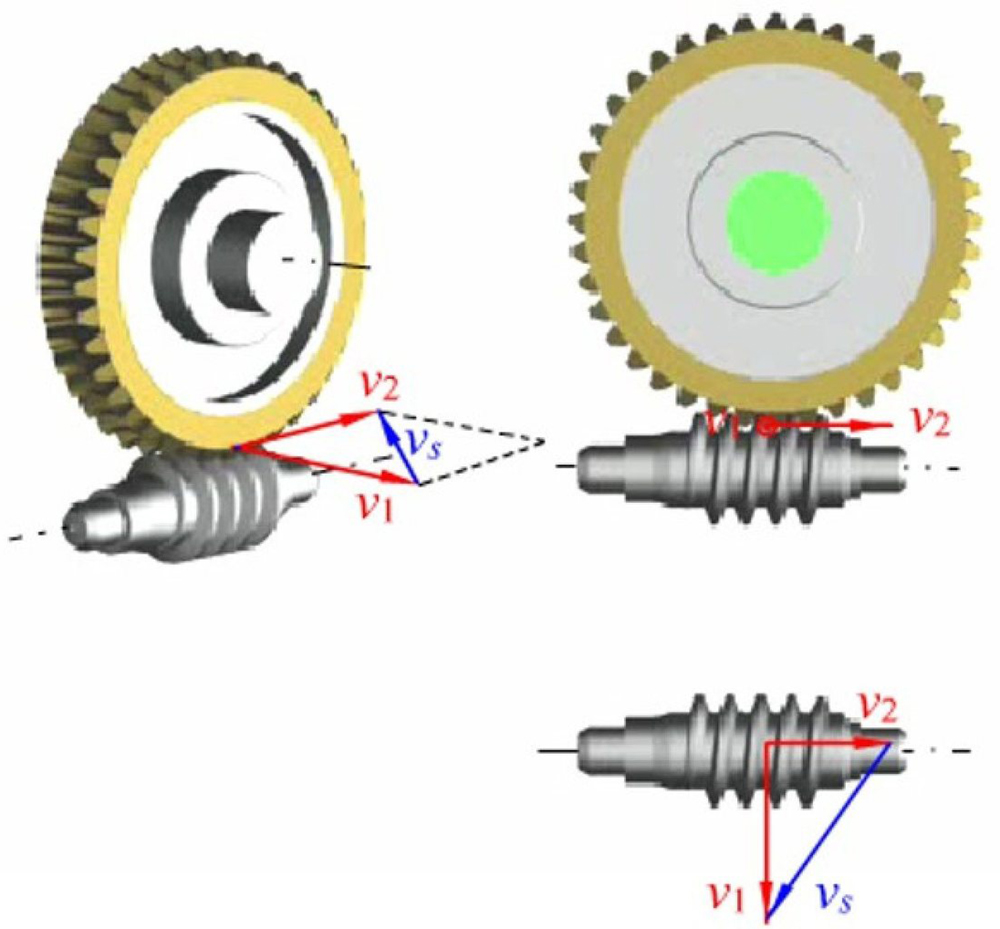
齿廓间较大的相对滑动会产生热量,润滑条件变差,传动效率降低。
(二)失效形式
蜗杆传动的主要失效形式有:齿面疲劳点蚀、胶合、磨损及轮齿折断。蜗杆传动在齿面间有较大的相对滑动速度,产生热量,使润滑油温度升高而变稀,导致润滑及散热不良,闭式传动易出现胶合。由于蜗轮的材料通常比蜗杆材料软,发生胶合时,蜗轮表面金属粘到蜗杆的螺旋面上,使蜗轮工作齿面形成沟痕。蜗轮轮齿的磨损严重,尤其在开式传动和润滑油不清洁的闭式传动中。
二、受力分析
蜗杆传动的受力分析与斜齿圆柱齿轮相似,轮齿在受到法向载荷Fn的情况下,可分解出径向载荷Fr、周向载荷Ft、轴向载荷Fa。如图所示。
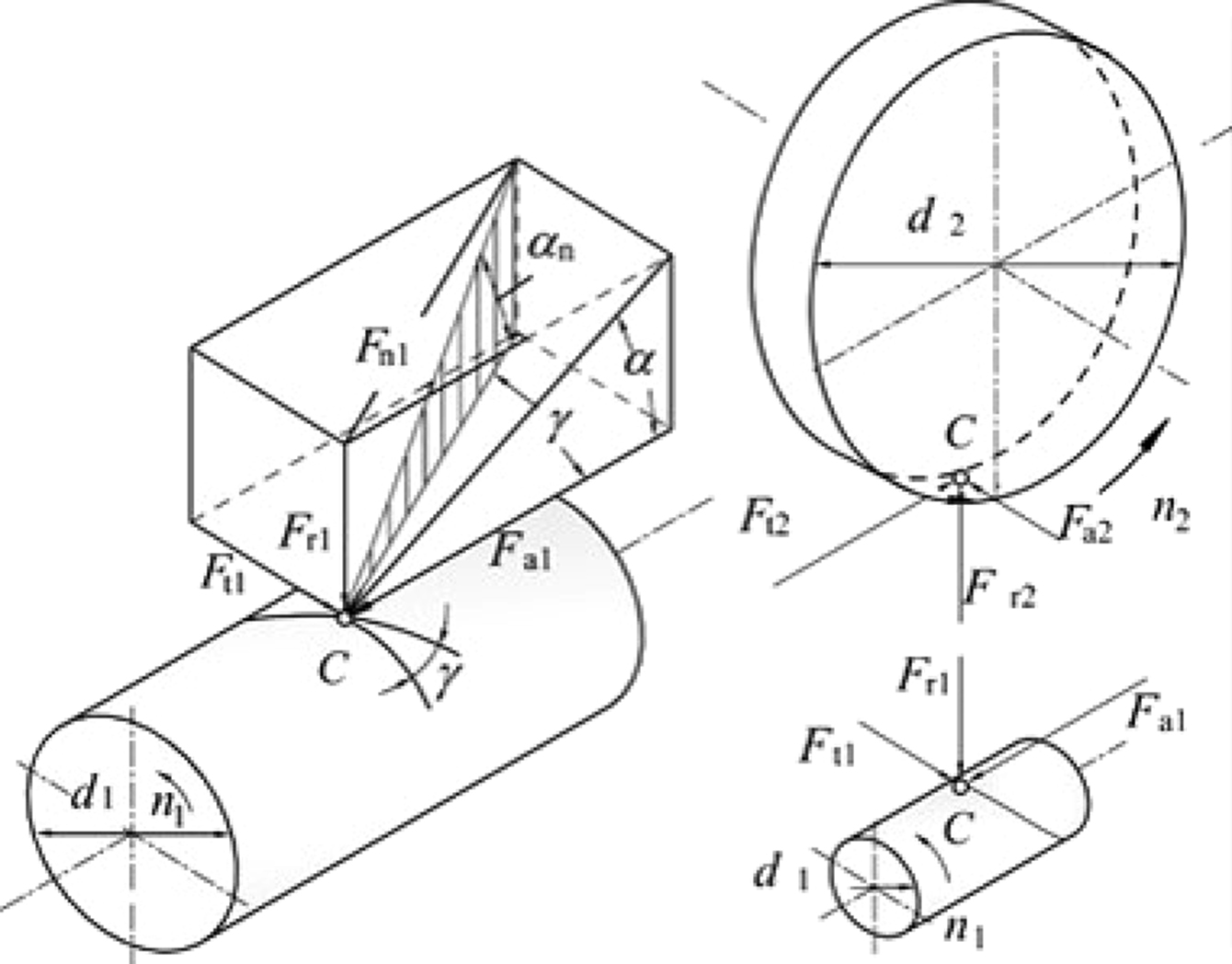
由于蜗杆和蜗轮轴交角为90°,根据作用力与反作用力原理,在不计摩擦力时,有以下关系:
式中,T1、T2分别为作用在蜗杆和蜗轮上的转矩(N·mm),T2=T1i η;η为蜗杆传动的效率。d1、d2分别为蜗杆和蜗轮的分度圆直径(mm),α为中间平面分度圆上的压力角,标准值为20°。
径向力Fr1和Fr2方向分别指向蜗杆和蜗轮的轮心。蜗杆轴向力Fa1的方向判别可套用判断斜齿轮轴向力的主动轮左右手法则。
三、设计准则
由于蜗轮材料强度、硬度低,失效总是先发生在蜗轮上,所以只对蜗轮轮齿做强度计算。目前,对于胶合和磨损的计算还缺乏成熟的方法,因此通常只是参照圆柱齿轮传动的计算方法,进行齿面接触疲劳强度和齿根弯曲疲劳强度的条件性计算,在选取材料的许用应力时适当考虑胶合和磨损的影响。
对于闭式蜗杆传动,通常按齿面接触疲劳强度来设计,并校核齿根弯曲疲劳强度(如果载荷平稳、无冲击,可以不校核)。
对于开式蜗杆传动,或传动时载荷变动较大,或蜗轮齿数z2大于90时,通常只需按齿根弯曲疲劳强度进行设计。
由于蜗杆传动时摩擦严重、发热大、效率低,对闭式蜗杆传动还必须作热平衡计算,以免发生胶合失效。
四、蜗杆传动的效率
闭式蜗杆传动的总效率与齿轮传动的总效率类似,即
式中,η1、η2、η3分别为考虑轮齿啮合齿面间摩擦损失时的效率、考虑油的搅动和飞溅损耗时的效率以及考虑轴承摩擦损失时的效率。
蜗杆传动的总效率,主要取决于啮合效率η1,其大小可近似地用螺旋副传动的效率公式计算。后两者的功率损失不大,一般取η2η3=0.95~0.97。因此,当蜗杆主动时,蜗杆传动的总效率为
式中,γ为蜗杆导程角(°),ρv为当量摩擦角,其值可根据材料和相对滑动速度vs由下表查取。fv为当量摩擦系数,fv=tanρv。
涡轮材料 | 锡青铜 | 无锡青铜 | ||||
---|---|---|---|---|---|---|
蜗杆齿面硬度 | HRC>45 | 其他情况 | HRC>45 | |||
滑动速度vs m/s | fv | ρv | fv | ρv | fv | ρv |
0.01 | 0.11 | 6.28˚ | 0.12 | 6.84˚ | 0.18 | 10.2˚ |
0.1 | 0.08 | 4.57˚ | 0.09 | 5.14˚ | 0.13 | 7.4˚ |
0.5 | 0.055 | 3.15˚ | 0.065 | 3.72˚ | 0.09 | 5.14˚ |
1 | 0.045 | 2.58˚ | 0.055 | 3.15˚ | 0.07 | 4˚ |
2 | 0.035 | 2˚ | 0.045 | 2.58˚ | 0.055 | 3.15˚ |
3 | 0.028 | 1.6˚ | 0.035 | 2˚ | 0.045 | 2.58˚ |
4 | 0.024 | 1.37˚ | 0.031 | 1.78˚ | 0.04 | 2.29˚ |
5 | 0.022 | 1.26˚ | 0.029 | 1.66˚ | 0.035 | 2˚ |
8 | 0.018 | 1.03˚ | 0.026 | 1.49˚ | 0.03 | 1.72˚ |
10 | 0.016 | 0.92˚ | 0.024 | 1.37˚ | ||
15 | 0.014 | 0.8˚ | 0.02 | 1.15˚ | ||
24 | 0.013 | 0.74˚ |
蜗杆传动效率在一定范围内随γ增大而增大,所以在传递动力中多采用多头蜗杆。但是当γ过大会增加制造困难,而且效率随γ增长速度变缓,所以在使用中一般取γ≤27°。当γ≤ρv时,蜗杆传动具有反传动自锁性,但效率很低。
在初步估算时,蜗杆传动的总效率可取下列近似数值:
闭式传动
z1=2 η=0.75~0.82
z1=4 η=0.82~0.92
自锁时 η<0.5
开式传动
五、蜗杆传动的强度计算
针对蜗杆传动失效形式及设计准则,蜗杆传动的强度计算包括:(1)蜗轮齿面的接触疲劳强度计算;(2)蜗轮轮齿弯曲疲劳强度计算;(3)热平衡计算。蜗杆轴本身的强度和刚度校核分别按照轴的强度和刚度校核方法处理。
(一)蜗轮齿面接触疲劳强度计算
蜗轮齿面基础疲劳强度的计算可以参照斜齿轮的计算方法进行,按节点处的啮合条件计算齿面的接触应力,可以推导出蜗轮齿面接触疲劳强度的校核公式为 :
上式适用于钢制蜗杆对青铜或铸铁蜗轮(齿圈)配对。经整理得蜗轮轮齿面接触疲劳强度的设计公式为
式中,K为载荷系数,K=1~1.4,当载荷平稳,滑动速度V2≤3m/s,7级以上精度时取较小值,否则取大值;T2为涡轮转矩,单位为N·mm;[ρH]为涡轮材料的许用接触应力,单位为MPa。
(二)蜗轮齿根弯曲疲劳强度计算
蜗轮轮齿的弯曲疲劳强度取决于轮齿模数的大小,但是轮齿齿形比较复杂,且在于中间平面距离不同截面上的齿厚并不相同,因此,弯曲疲劳强度难以精确计算,只能进行条件性的概略估算。蜗轮齿根弯曲强度的校核公式为
设计公式为
式中,Yβ为螺旋角因数,;YFS为蜗轮复合齿形因数,同齿轮的复合齿形因数,与轮齿形状有关,与模数无关。
(三)蜗杆传动的热平衡计算
蜗杆传动的效率低,发热量大,因而使蜗杆、蜗轮和箱体的温度升高。另一方面,由于热量会从箱体表面散发到周围大气中,最后使箱体温度保持于某一温度t1,此时蜗杆传动产生的热量与箱体散发的热量相等而保持平衡。对于箱体的这种平衡温度t1,通常要求不超过95℃,以免润滑变稀,承载油膜破坏而使齿面易产生胶合。因此,对闭式蜗杆传动应进行热平衡计算。
若蜗杆传动转化为热量所消耗的功率为Ps(W),则
经箱体散发热量的相当功率为Pc(W),则
在平衡状态下,Ps=Pc,推导出热平衡时润滑油的工作温度t1的计算公式
式中,P1
K
η
A
t2
t1
[t1]
如果工作温度t1超过了许用温度[t1],首先考虑在不改变箱体尺寸的前提下,增加散热面积,如在箱体外壁增加散热片。若仍不满足要求,可采用下列强制冷却的措施,提高散热能力:
(1)如下图a所示,在蜗杆轴端增设风扇,提高散热系数。这是最简单的强制冷却的方法,散热系数K可达到21~28W/(m2·℃)。
(2)如下图b所示,在箱体内装蛇形管,通过循环水冷却润滑油。冷水通过蛇形管可带走润滑油热量,降低油温,达到强制冷却的目的。
(3)如下图c所示,采用循环压力喷油冷却。
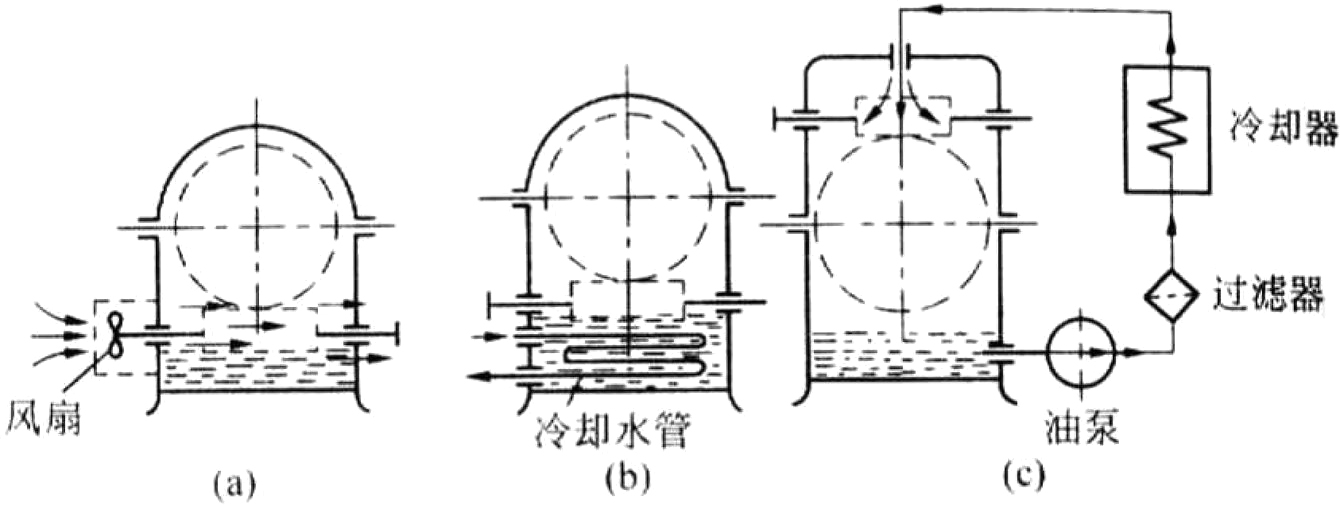