素质目标:具备正确的社会主义核心价值观和道德法律意识;具备精益求精、追求卓越的工匠精神和严谨细致、踏实肯干的工作作风;具备良好的团队协作精神、协调能力、组织能力和管理能力。
知识目标:了解数控车床编程指令的功能,掌握数控车床各编程指令的结构和组成,掌握数控车床编程指令的使用方法和思路。
能力目标:能够准确编写加工程序,能够根据加工工艺要求完成零件的编程工作;能够掌握编程过程中的辅助编程指令的应用场合;能够正确地利用数控车床各个运动的坐标轴,做好基点的计算。
毛坯尺寸为: 的棒料 |
|
加工表面 | 数控车编程指令选用 |
---|---|
左侧R50.9外圆弧面 | |
5 2外沟槽面 | |
M30 2外螺纹面 | |
22,
30,
44外圆柱面及其C2 |
一、插补功能指令
(一)线性进给 G01
1.格 式
G01 X(U)_ Z(W) _ F_
2.说 明
X、Z:为绝对编程时终点在工件坐标系中的坐标。
U、W:为增量编程时终点相对于起点的位移量。
F:合成进给速度。
G01指令刀具以联动的方式,按F规定的合成进给速度,从当前位置按线性路线(联动直线轴的合成轨迹为直线)移动到程序段指令的终点。
G01是模态代码,可由G00、G02、G03 或G32 注销。
(二)圆弧进给G02/G03
2.格 式
G02/G03 X(U)_ Z(W)_ R_ (I_K_) F_
3.说 明
X、Z:为绝对编程时圆弧终点在工件坐标系中的坐标。
U、W:为增量编程时圆弧终点相对于起点的位移量。
F:合成进给速度。
G02/G03 指令刀具按顺时针/逆时针进行圆弧加工。
圆弧插补G02/G03 的判断,是在加工平面内,根据其插补时的旋转方向为顺时针/逆时针来区分的。加工平面为观察者迎着Y 轴的指向,所面对的平面。如图2.2.1所示。
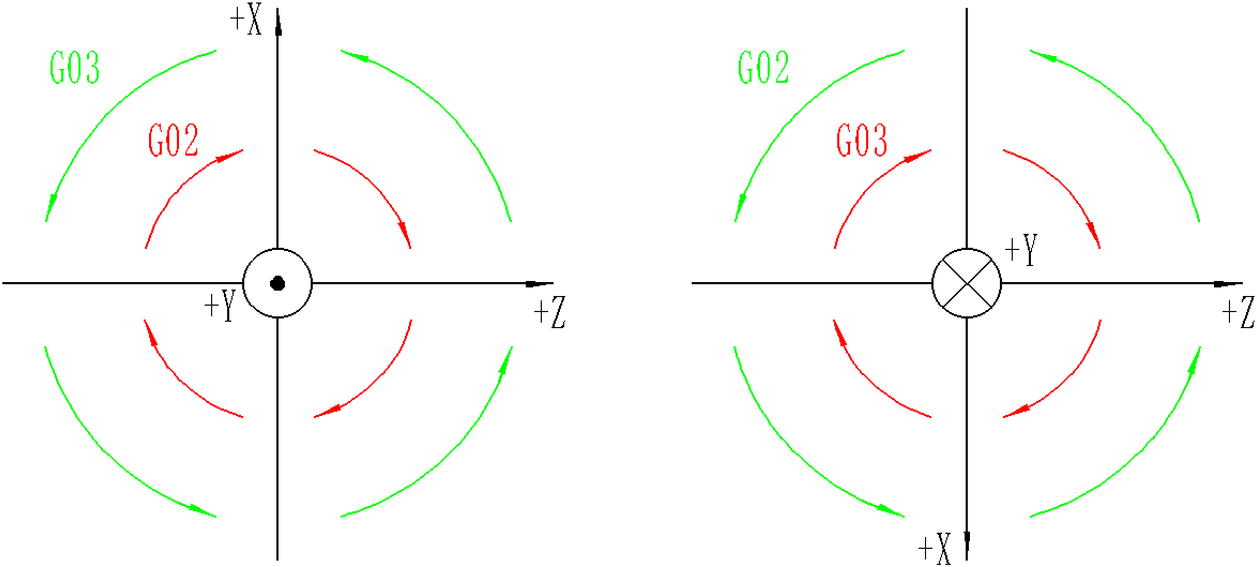
各参数含义如图2.2.2所示。
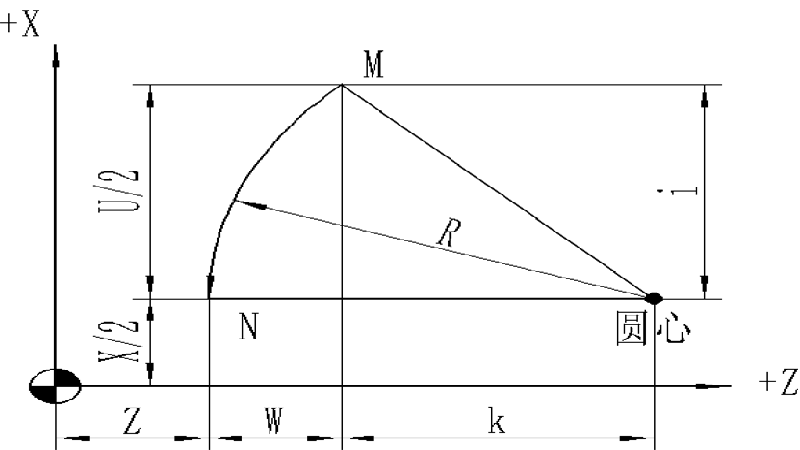
二、进给功能
(一)快速进给 G00
1.格 式
G00 X(U)_ Z(W)_
2.说 明
X、Z:为绝对编程时,快速定位终点在工件坐标系中的坐标。
U、W:为增量编程时,快速定位终点相对于起点的位移量。
G00 指令刀具相对于工件以各轴预先设定的速度,从当前位置快速移动到程序段指令的定位目标点; G00 指令中的快移速度由机床参数“快移进给速度”对各轴分别设定,不能用F 规定。
G00一般用于加工前快速定位或加工后快速退刀。快移速度可由面板上的快速修调按钮修正。G00为模态功能,可由G01、G02、G03 或G32 功能注销。
3.注意事项
在执行G00 指令时,由于各轴以各自速度移动,不能保证各轴同时到达终点,因而联动直线轴的合成轨迹不一定是直线。操作者必须格外小心,以免刀具与工件发生碰撞,常见的做法是,将X轴移动到安全位置,再放心地执行G00 指令。
三、螺纹切削(G32)
(一)单行程螺纹切削指令
1.格 式
G32 X(U)__Z(W)__F__
2.说 明
F–螺纹导程。
X(U)、 Z(W) - 螺纹切削的终点坐标值;起点和终点的X坐标值相同(不输入X或U)时,进行直螺纹切削;X省略时为圆柱螺纹切削,Z省略时为端面螺纹切削;X、Z均不省略时为锥螺纹切削。
在编制切螺纹程序时应当带主轴脉冲编码器,因为螺纹切削开始是从检测出主轴上的位置编码器一转信号后才开始的,因此即使进行多次螺纹切削,零件圆周上的切削点仍然相同,工件上的螺纹轨迹也是相同的。从粗车到精车,用同一轨迹要进行多次螺纹切削,主轴的转速必须是一定的。当主轴转速变化时,有时螺纹会或多或少产生偏差。在螺纹切削方式下移动速率控制和主轴速率控制功能将被忽略。而且在进给保持按钮起作用时,其移动过程在完成一个切削循环后就停止了。
3.注意事项
四、固定循环指令
(一)外径/内径切削固定循环指令(G90)
1.柱面切削固定循环
(1)格式。
G90X(U)_____ Z(W)______ F ______
(2)说明。
X、Z:绝对编程时,为切削终点C在编程坐标系下的坐标。
U、W:增量值编程时,为切削终点C 相对于循环起点A的有向距离,其符号由轨迹1 和2 的方向确定。
F:切削进给速度。
(3)轨迹动作。
该指令执行如图2.2.3所示A→B→C→D→A 的轨迹动作。
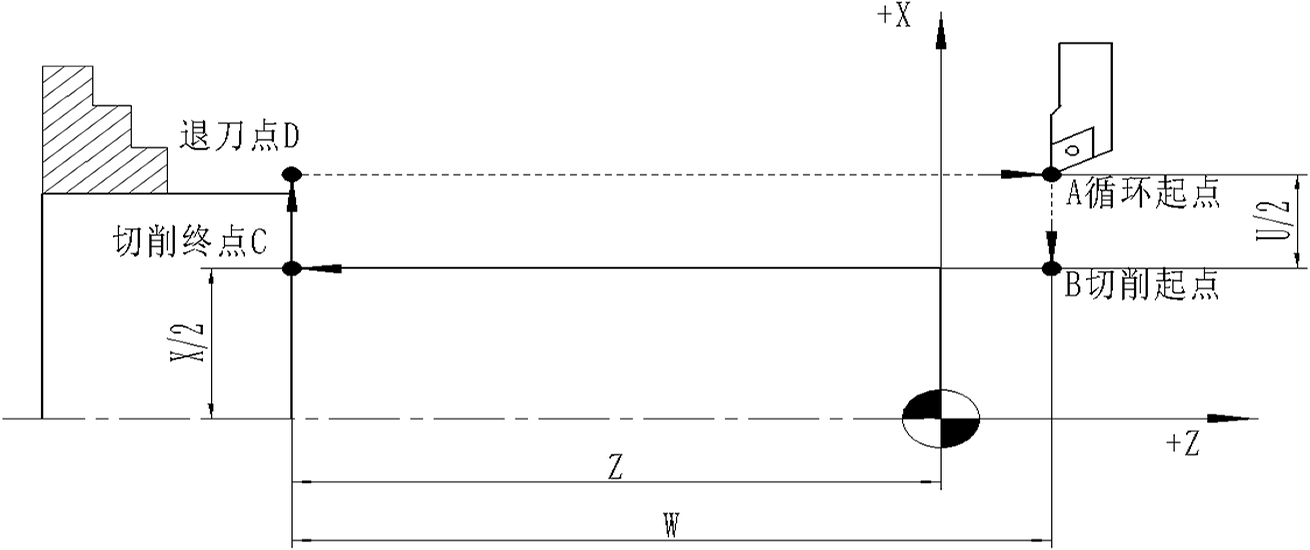
R──表示快速移动;F──表示由F代码指定的速度。
(4)指令应用。
如图2.2.4所示,毛坯尺寸为Φ50×70,用G90编程,编写出Φ40×30圆柱面的数控程序。
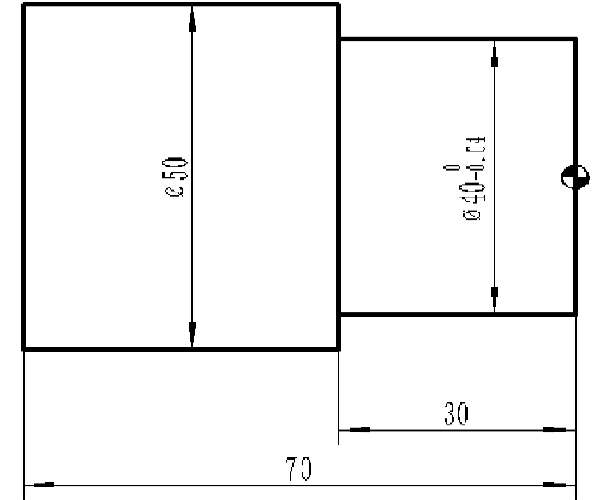
以FANUC系统为例进行编程,分三刀完成此表面的加工,前两次每次切深2mm,最后一次切深1mm,进给速度选择为100mm每分钟,主轴转速设定为500转每分钟,选择90度右偏外圆刀,设定工件右端面中心为编程原点。数控加工程序见表2-2-1所示。
程序内容 |
说明 |
备注 |
---|---|---|
O1 |
程序名称 |
|
N10 T0101 |
选择1号刀具 |
|
N20 M03 S500 G98 |
设定主轴转速,设定每分进给量 |
|
N30 G00 X100 Z100 |
快速定位 |
|
N40 X52 Z5 |
定位至循环点 |
|
N50 G90 X46 Z-30 F100 |
循环加工Φ46×30外圆柱面 |
|
N60 X42 |
循环加工Φ42×30外圆柱面 |
|
N70 X40 |
循环加工Φ40×30外圆柱面 |
|
N80 G00 X100 Z100 M05 |
快速退回,主轴停转 |
|
N90 M30 |
程序结束 |
2.锥面切削固定循环
(1)格式。
G90X(U)_____ Z(W)_____ R _____ F_____
(2)说明。
X、Z:绝对编程时,为切削终点C在编程坐标系下的坐标。
U、W:增量值编程时,为切削终点C 相对于循环起点A的有向距离,其符号由轨迹1 和2 的方向确定。
R:为切削起点B 与切削终点C 的半径差,其符号为差的符号。
F:切削进给速度。
(3)轨迹动作。
该指令执行如图2.2.5所示A→B→C→D→A 的轨迹动作。
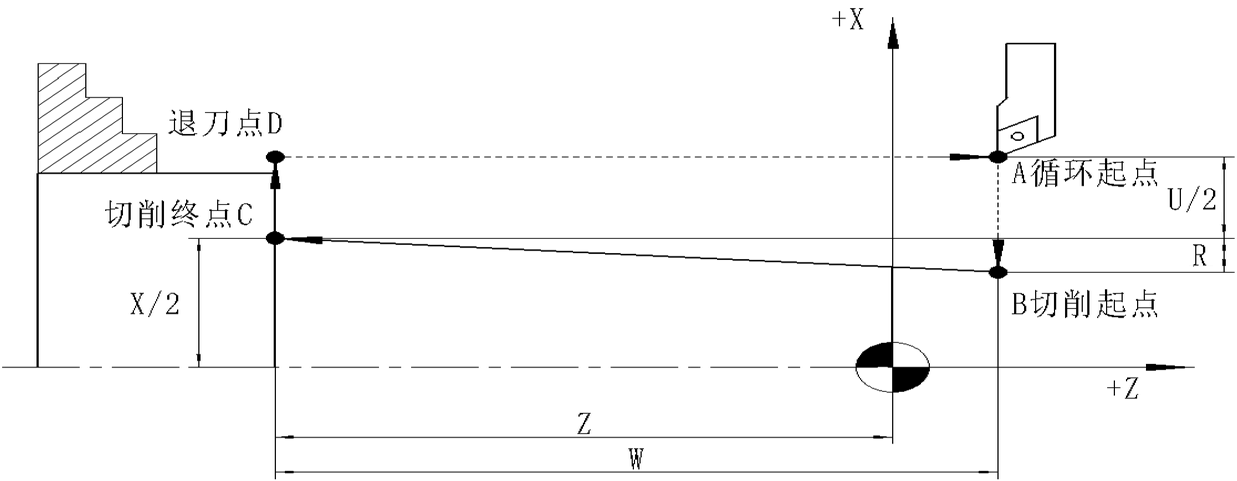
R──表示快速移动。 F──表示由F代码指定的速度。
(4)指令应用。
如图2.2.6所示,毛坯尺寸为Φ50×70,用G90编程,编写出大端直径为Φ40,小端直径为Φ34,锥长为30的圆锥面的数控程序。
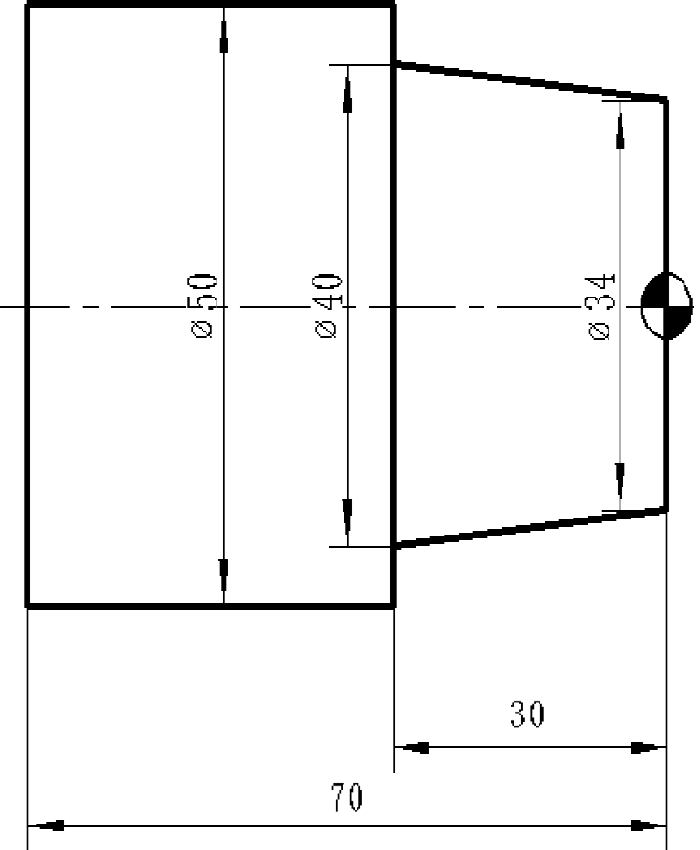
以FANUC系统为例进行编程,分三刀完成此表面的加工,前两次每次切深2mm,最后一次切深1mm,进给速度选择为100mm每分钟,主轴转速设定为500转每分钟,选择90度右偏外圆刀,设定工件右端面中心为编程原点,参考程序见表2-2-2所示。
程序内容 |
说明 |
备注 |
---|---|---|
O1 |
程序名称 |
|
N10 T0101 |
选择1号刀具 |
|
N20 M03 S500 G98 |
设定主轴转速,设定每分进给量 |
|
N30 G00 X100 Z100 |
快速定位 |
|
N40 X52 Z5 |
定位至循环点 |
|
N50 G90 X46 Z-30 R-3.5 F100 |
循环加工大端Φ46外圆锥面 |
|
N60 X42 |
循环加工大端Φ42外圆锥面 |
|
N70 X40 |
循环加工大端Φ40外圆锥面 |
|
N80 G00 X100 Z100 M05 |
快速退回,主轴停转 |
|
N90 M30 |
程序结束 |
(二)端面车削固定循环指令(G94)
1.平端面切削固定循环
(1)格式。
G94X(U)____ Z(W)____ F____
(2)说明。
X、Z:绝对编程时,为切削终点C在编程坐标系下的坐标。
U、W:增量值编程时,为切削终点C 相对于循环起点A的有向距离,其符号由轨迹1 和2 的方向确定。
F:切削进给速度。
(3)轨迹动作。
该指令执行如图2.2.7 所示A→B→C→D→A 的轨迹动作。
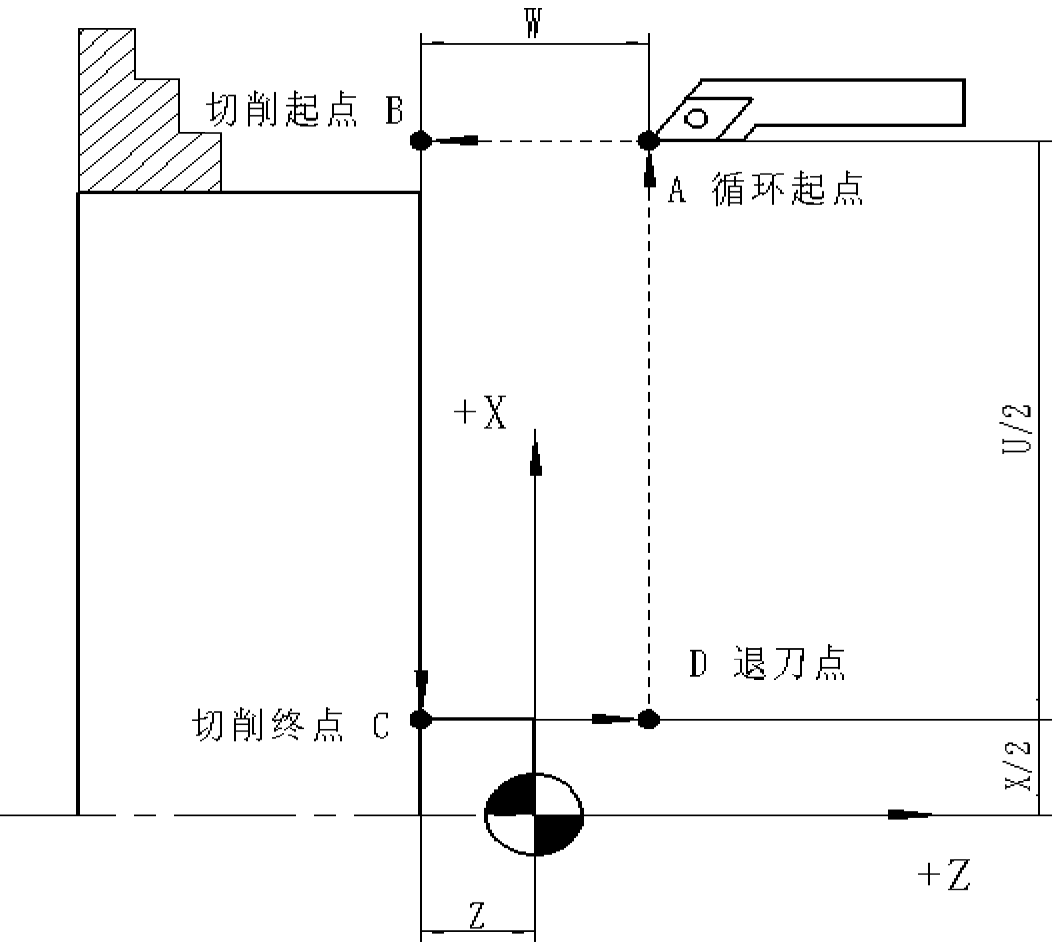
R──表示快速移动。F──表示由F代码指定的速度。
(4)指令应用。
毛坯尺寸为Φ50×70,用G94编程,编写出车平端面的数控程序。
以FANUC系统为例进行编程,进给速度选择为50mm/min,主轴转速设定为500转/min,选择端面刀,设定工件右端面中心为编程原点,参考程序见表2-2-3所示。
程序内容 |
说明 |
备注 |
---|---|---|
O1 |
程序名称 |
|
N10 T0202 |
选择2号刀具 |
|
N20 M03 S500 G98 |
设定主轴转速,设定每分进给量 |
|
N30 G00 X100 Z100 |
快速定位 |
|
N40 X52 Z5 |
定位至循环点 |
|
N50 G94 X0 Z0 F50 |
循环加工平端面 |
|
N60 G00 X100 Z100 M05 |
快速退回,主轴停转 |
|
N70 M30 |
程序结束 |
2.锥端面切削固定循环
(1)格式。
G94X(U) ____ Z(W)____ R ____ F ____
(2)说明。
X、Z:绝对编程时,为切削终点C在编程坐标系下的坐标。
U、W:增量值编程时,为切削终点C 相对于循环起点A的有向距离,其符号由轨迹1 和2 的方向确定。
F:切削进给速度。
R:为切削起点B 相对于切削终点C 的Z 向有向距离。
(3)轨迹动作。
该指令执行如图2.2.8所示A→B→C→D→A 的轨迹动作。
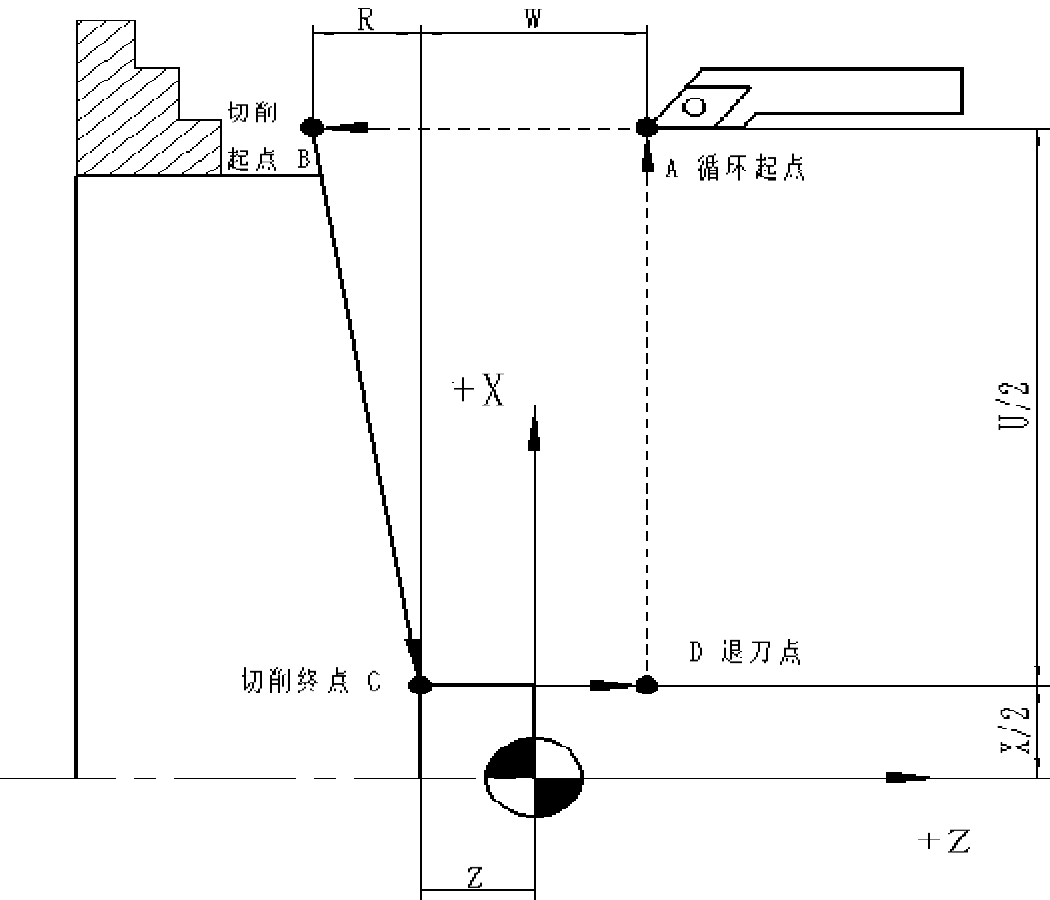
R──表示快速移动。F──表示由F代码指定的速度。
(4)指令应用。
如图2.2.9所示,毛坯尺寸为Φ50×47,用G94编程,编写出车锥端面的数控程序。
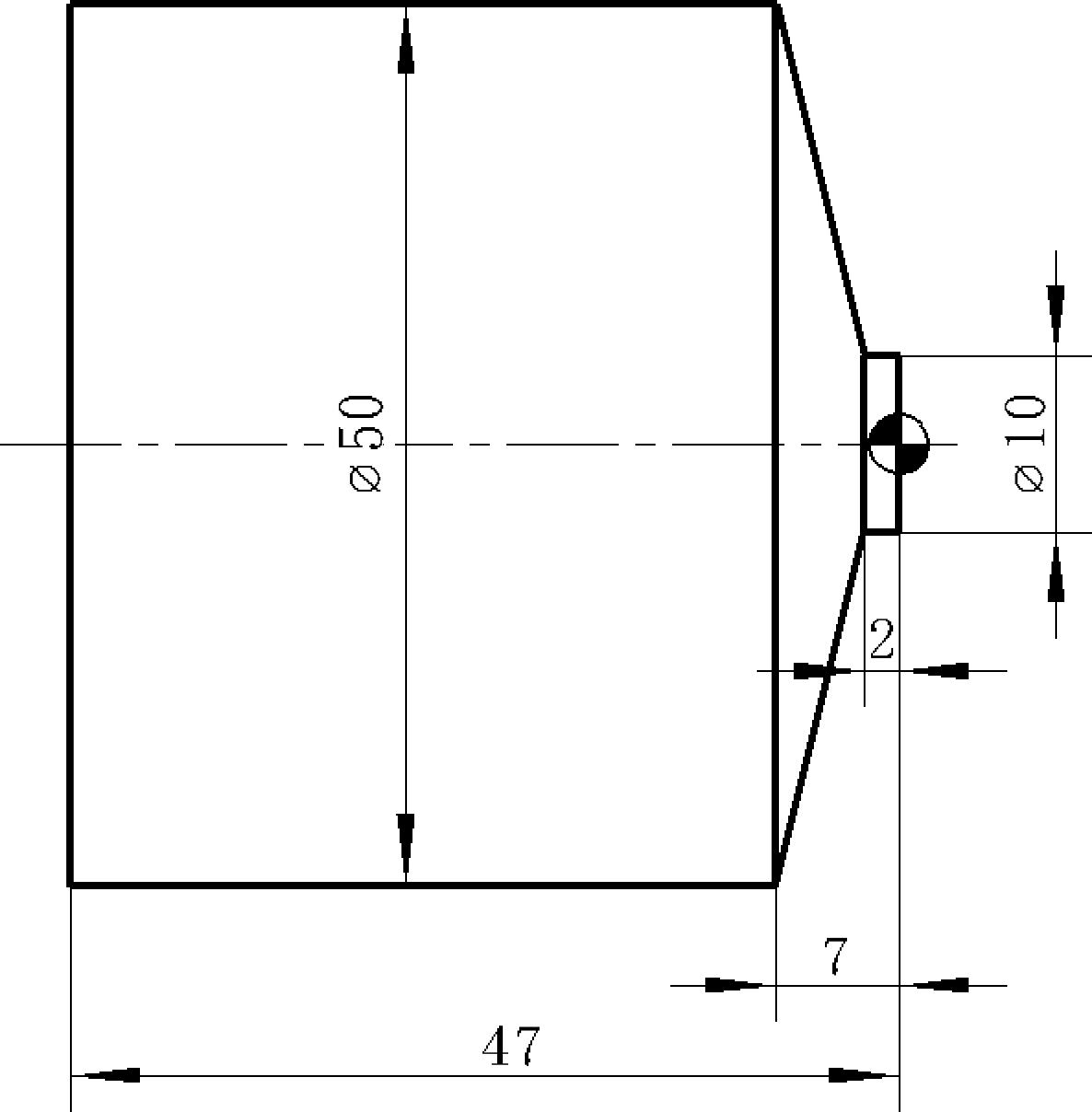
以FANUC系统为例进行编程,进给速度选择为50mm/min,主轴转速设定为500转/min,选择端面刀,前两次切深为3mm,最后一次切深为1mm,设定工件右端面中心为编程原点,参考程序见表2-2-4所示。
程序内容 |
说明 |
备注 |
---|---|---|
O1 |
程序名称 |
|
N10 T0202 |
选择2号刀具 |
|
N20 M03 S500 G98 |
设定主轴转速,设定每分进给量 |
|
N30 G00 X100 Z100 |
快速定位 |
|
N40 X52 Z5 |
定位至循环点 |
|
N50 G94 X10 Z2 R-5 F50 |
循环加工锥端面 |
|
N60 Z-1 |
循环加工锥端面 |
|
N70 Z-2 |
循环加工锥端面 |
|
N80 G00 X100 Z100 M05 |
快速退回,主轴停转 |
|
N90 M30 |
程序结束 |
(三)螺纹车削简单循环指令(G92)
1.直螺纹切削固定循环
(1)格式。
G92X(U)____ Z(W)____ F ____
(2)说明。
X、Z:绝对编程时,为螺纹终点C 在编程坐标系下的坐标。
U、W:为螺纹终点C 相对于循环起点A的有向距离,图形中用U、W 表示。
F:螺纹导程。
(3)轨迹动作。
该指令执行如图2.2.10所示A→B→C→D→A 的轨迹动作。
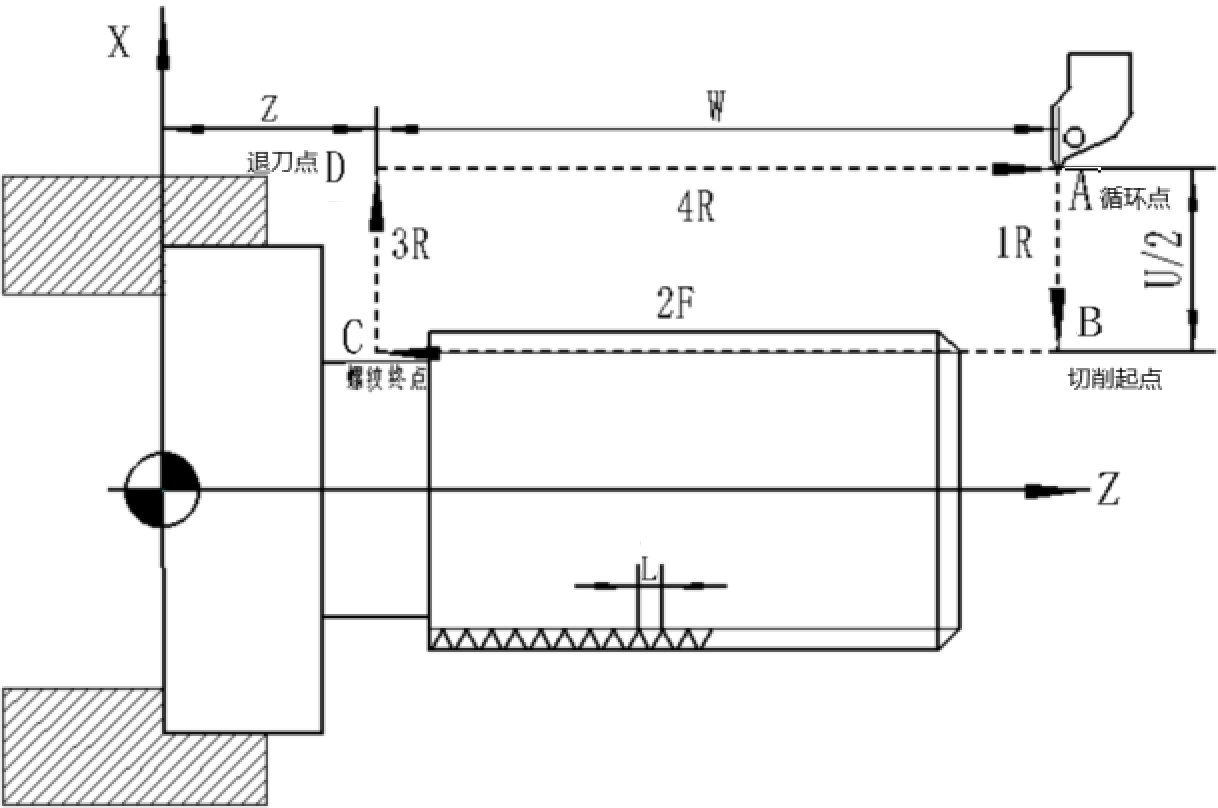
R──表示快速移动。F──表示由F代码指定的速度。
(4)指令应用。
如图2.2.11所示,毛坯尺寸为Φ50×75,用G92编程,其他表面已加工完成,仅需编写出M30×2圆柱螺纹的数控程序。
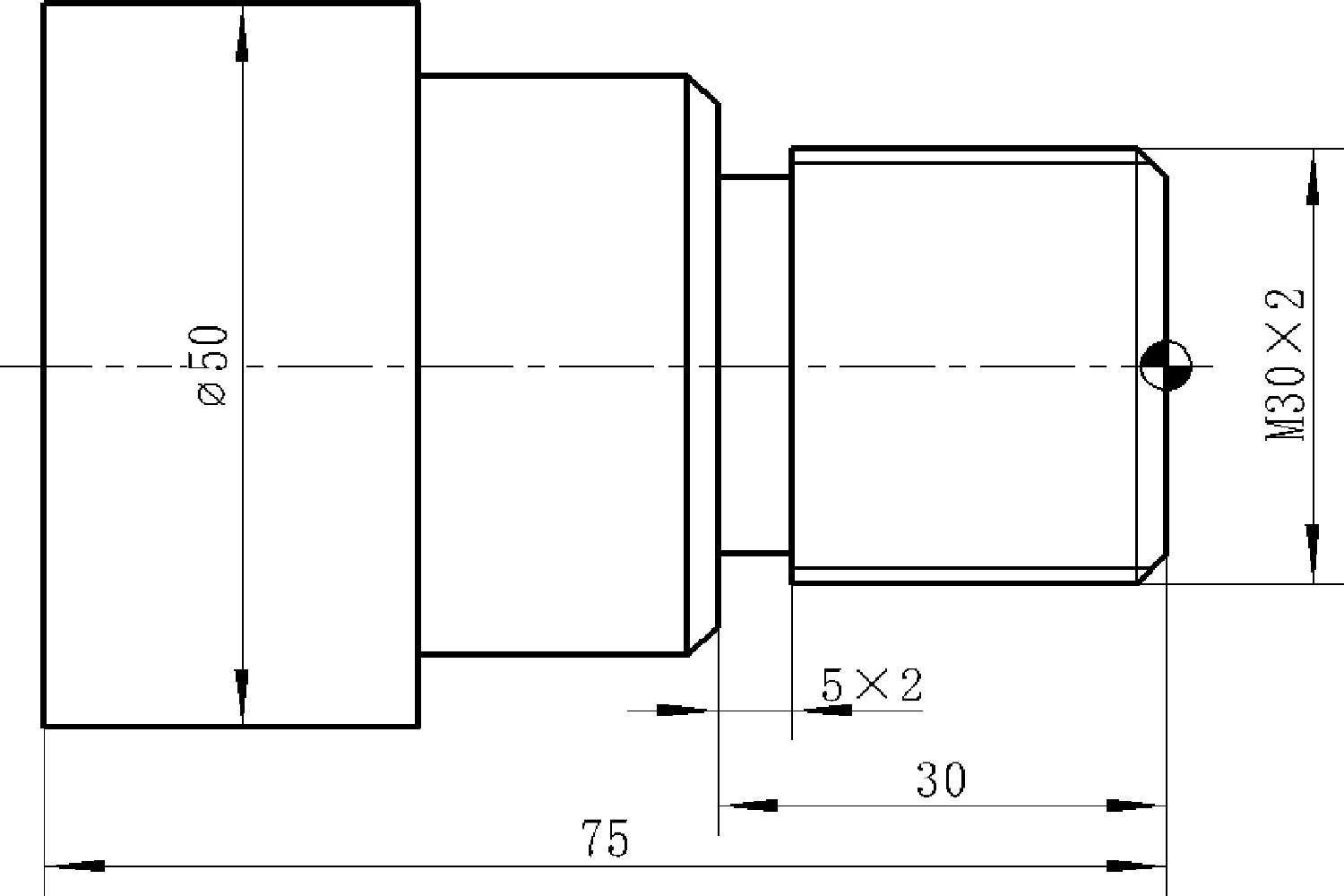
以FANUC系统为例进行编程,主轴转速设定为500转每分钟,选择外螺纹刀,螺纹进给次数及切削深度可以参考螺纹进给次数及切削深度表,见表2-2-5;车削外螺纹公称直径时,根据塑性材料变形的特点,须事先将该直径车小0.1-0.2mm左右;按经验公式,外螺纹小径d小=公称直径d公-(1.2~1.3)螺距P,参考程序见表2-2-6所示。
米制螺纹 |
||||||||
---|---|---|---|---|---|---|---|---|
螺距 |
1.0 |
1.5 |
2.0 |
2.5 |
3.0 |
3.5 |
4.0 |
|
牙深(半径量) |
0.649 |
0.974 |
1.299 |
1.624 |
1.949 |
2.273 |
2.598 |
|
切削次数及吃刀量 |
1次 |
0.7 |
0.8 |
0.9 |
1.0 |
1.2 |
1.5 |
1.5 |
2次 |
0.4 |
0.6 |
0.6 |
0.7 |
0.7 |
0.7 |
0.8 |
|
3次 |
0.2 |
0.4 |
0.6 |
0.6 |
0.6 |
0.6 |
0.6 |
|
4次 |
0.16 |
0.4 |
0.4 |
0.4 |
0.6 |
0.6 |
||
5次 |
0.1 |
0.4 |
0.4 |
0.4 |
0.4 |
|||
6次 |
0.15 |
0.4 |
0.4 |
0.4 |
||||
7次 |
0.2 |
0.2 |
0.4 |
|||||
8次 |
0.15 |
0.3 |
||||||
9次 |
0.2 |
程序内容 |
说明 |
备注 |
---|---|---|
O1 |
程序名称 |
|
N10 T0303 |
选择3号刀具 |
|
N20 M03 S500 G98 |
设定主轴转速,设定每分进给量 |
|
N30 G00 X100 Z100 |
快速定位 |
|
N40 X35 Z5 |
定位至循环点 |
|
N50 G92 X29. 1 Z-27 F2 |
循环加工直径X29. 1 长度27的 |
|
N60 X28.5 |
循环加工直径X28.5 长度27的 |
|
N70 X27.9 |
循环加工直径X27.9 长度27的 |
|
N80 X27.5 |
循环加工直径X27.5 长度27的 |
|
N90 X27.4 |
循环加工直径X27.4 长度27的 |
|
N100 G00 X100 Z100 M05 |
快速退回,主轴停转 |
|
N110 M30 |
程序结束 |
2.锥螺纹切削固定循环
(1)格式。
G92X(U)____ Z(W)____ R ____ F____
(2)说明。
X、Z:绝对编程时,为螺纹终点C 在编程坐标系下的坐标。
U、W:增量值编程时,为螺纹终点C 相对于循环起点A的有向距离,图形中用U、W 表示。
R:为螺纹起点B 与螺纹终点C 的半径差,其符号为差的符号。
F:螺纹导程。
(3)轨迹动作。
该指令执行如图2.2.12所示A→B→C→D→A 的轨迹动作。
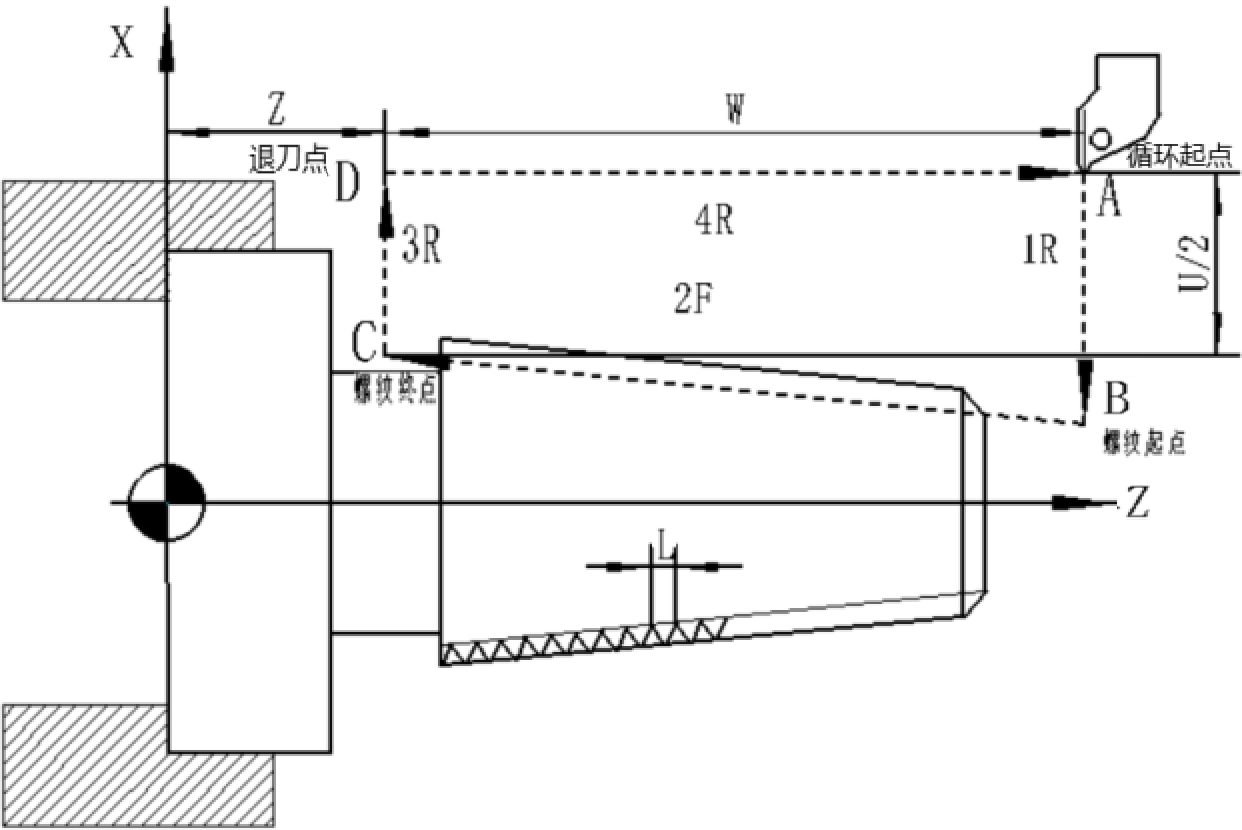
R──表示快速移动。F──表示由F代码指定的速度。
(4)指令应用。
如图2.2.13所示,毛坯尺寸为Φ50×75,用G92编程,其他表面已加工完成,仅需编写出M30×2圆锥螺纹的数控程序,参考程序见表2-2-7所示。
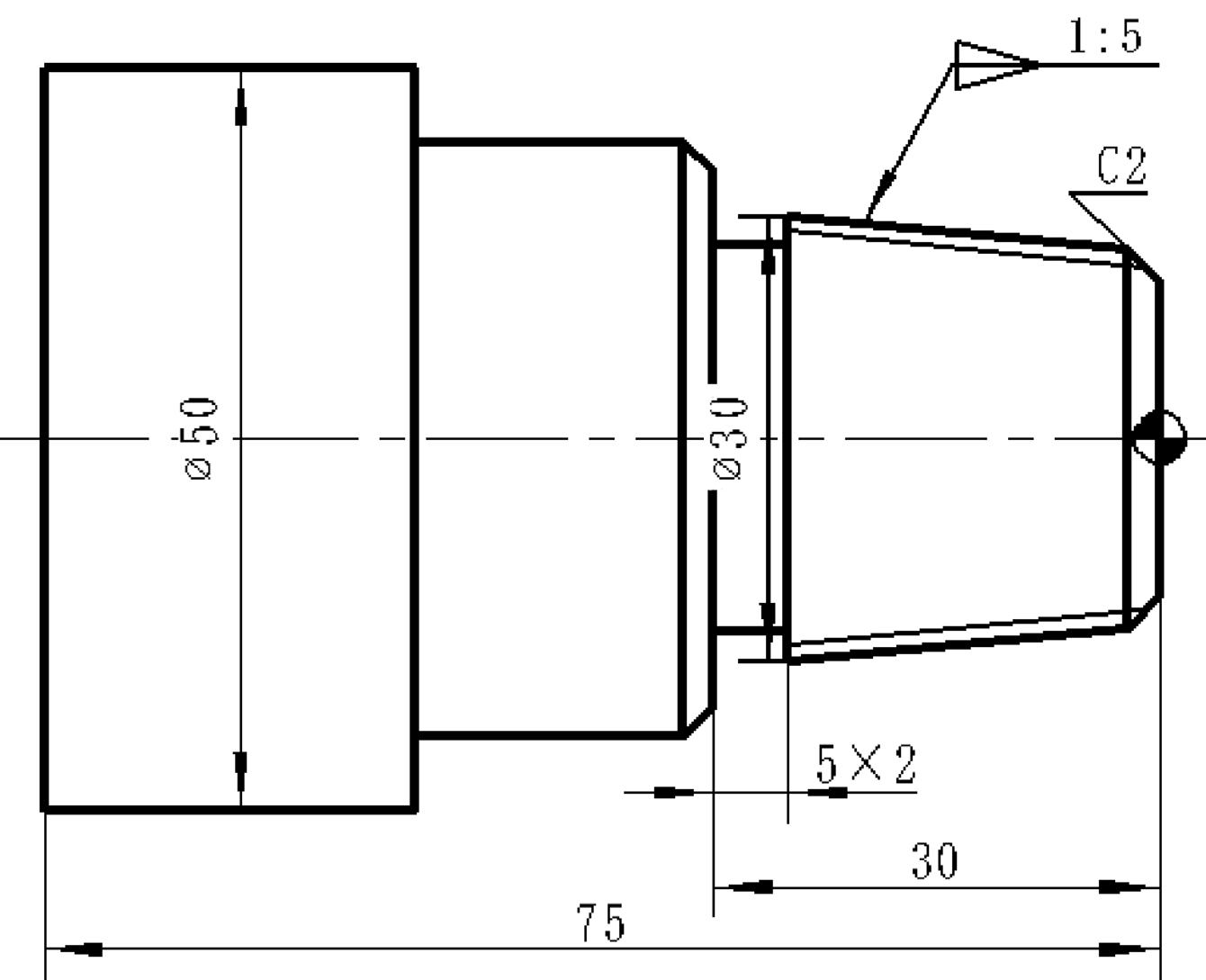
程序内容 |
说明 |
备注 |
---|---|---|
O1 |
程序名称 |
|
N10 T0303 |
选择3号刀具 |
|
N20 M03 S500 G98 |
设定主轴转速,设定每分进给量 |
|
N30 G00 X100 Z100 |
快速定位 |
|
N40 X35 Z5 |
定位至循环点 |
|
N50 G92 X29. 1 Z-27 R-3.2 F2 |
循环加工直径X29. 1 长度27的 |
|
N60 X28.5 |
循环加工直径X28.5 长度27的 |
|
N70 X27.9 |
循环加工直径X27.9 长度27的 |
|
N80 X27.5 |
循环加工直径X27.5 长度27的 |
|
N90 X27.4 |
循环加工直径X27.4 长度27的 |
|
N100 G00 X100 Z100 M05 |
快速退回,主轴停转 |
|
N110 M30 |
程序结束 |
五、复合循环指令
(一)内外径车削复合循环指令(G71)
1.格 式
G71 U(△d)__ R(e)__
G71 P(ns)__ Q(nf)__ U(△ u)__ W(△ w)__ F__
2.说 明
△d:切削深度(每次切削量),半径值。
e:每次退刀量。
ns:精加工路径第一程序段(即图中的AA')的顺序号。
nf:精加工路径最后程序段(即图中的B‘B)的顺序号。
△u:X 方向精加工余量,直径值,加工孔时为负值。
△w:Z 方向精加工余量的距离及方向。
3.轨迹动作
如图2.2.14所示。
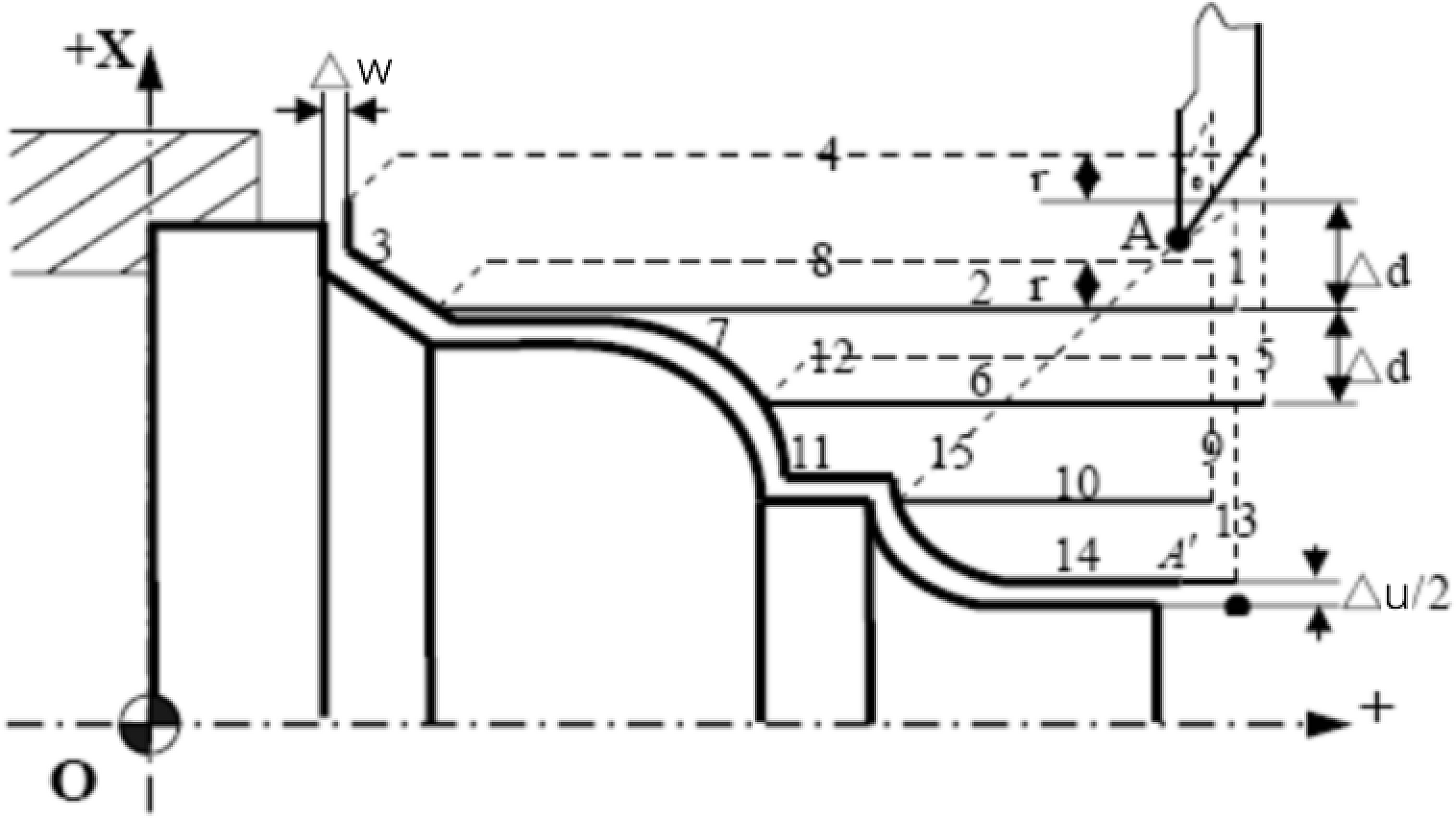
4.指令应用
如图2.2.15所示,毛坯尺寸为Φ60×120,用G71编程,编写出数控程序见表2-2-8所示。
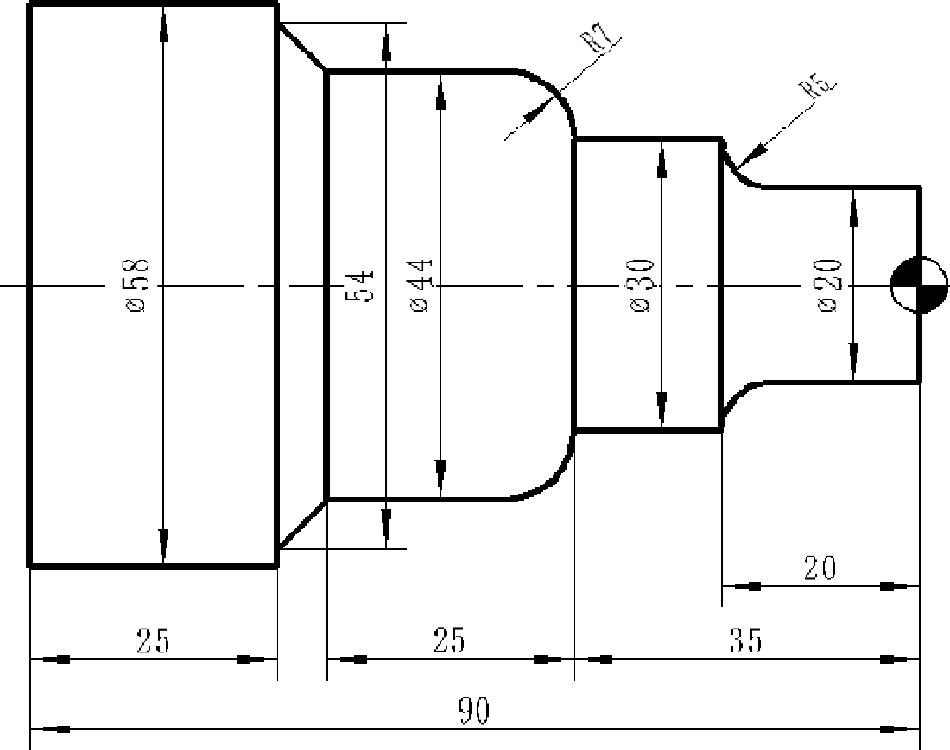
程序内容 |
说明 |
备注 |
---|---|---|
O1 |
程序名称 |
|
N10 T0101 |
选择1号刀具 |
|
N20 M03 S500 G98 |
设定主轴转速,设定每分进给量 |
|
N30 G00 X100 Z100 |
快速定位 |
|
N40 X65 Z5 |
定位至循环点 |
|
N50 G71 U2 R1 |
设定切深2mm,退刀1mm |
|
N60 G71 P70 Q160 U0.5W0.1F100 |
设定精加工循环为N70至N160,并留精加工余量直径方向为0.5mm,长度方向为0.1mm,粗加工进给速度为100mm每分钟。 |
|
N70 G00 X20 |
精加工轮廓 |
|
N80 G01 Z-15 F50 |
精加工轮廓 |
|
N90 G02 X30 Z-20 R5 |
精加工轮廓 |
|
N100 G01 Z-35 |
精加工轮廓 |
|
N110 G03 X44 Z-42R7 |
精加工轮廓 |
|
N120 G01 Z-60 |
精加工轮廓 |
|
N130 X54 Z-70 |
精加工轮廓 |
|
N140 X58 |
精加工轮廓 |
|
N150 Z-90 |
精加工轮廓 |
|
N160 G01 X65 |
精加工轮廓 |
|
N170 G00 X100 Z100 M05 |
快速退回,主轴停转 |
|
N180 M30 |
程序结束 |
(二)端面车削复合循环指令(G72)
1.格 式
G72 W(△d)__ R(e)__
G72 P(ns)__ Q(nf)__ U(△ u)__ W(△ w)__ F__
2.说 明
△d:切削深度,指定时不加符号。
e:每次退刀量。
ns:精加工路径第一程序段(即图中的AA')的顺序号。
nf:精加工路径最后程序段(即图中的B‘B)的顺序号。
△u:X 方向精加工余量,直径值,加工孔时为负值。
△w:Z 方向精加工余量的距离及方向。
3.轨迹动作
如图2.2.16所示。
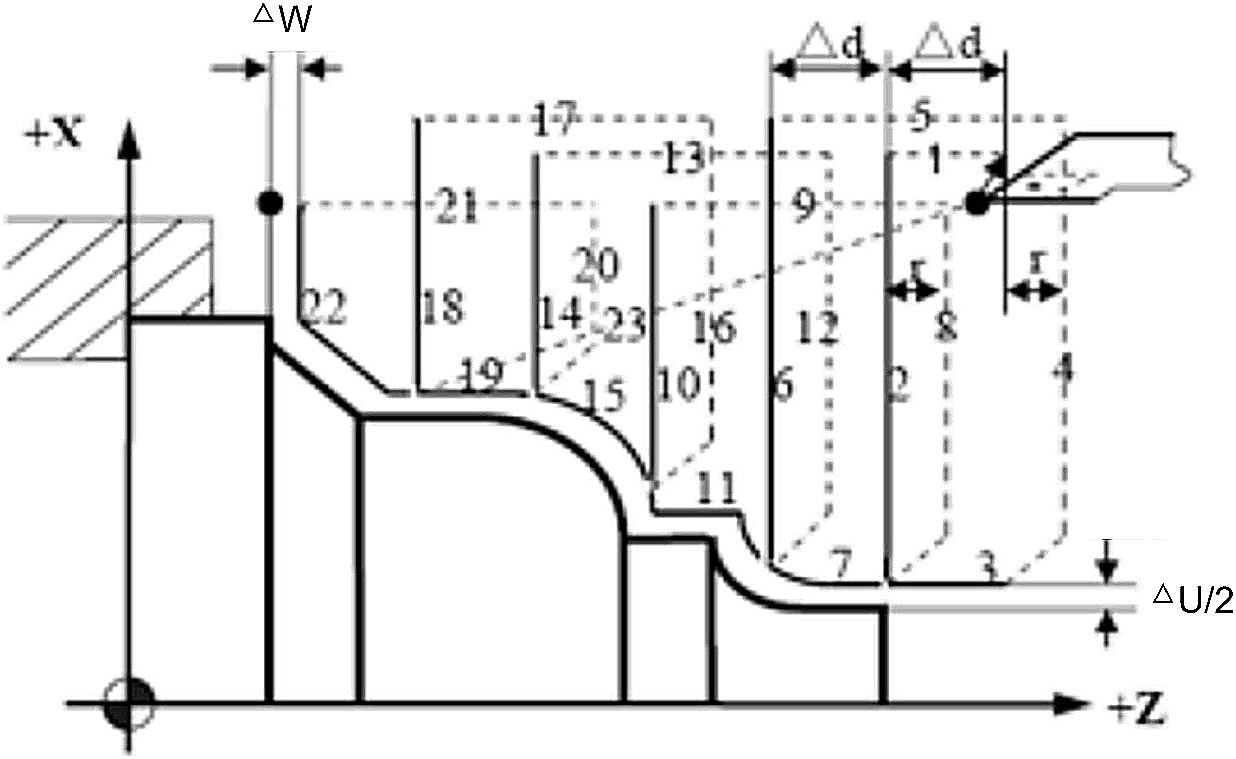
4.指令应用
如图2.2.17所示,毛坯尺寸为Φ105×70,用G72编程,编写出数控程序见表2-2-9所示。
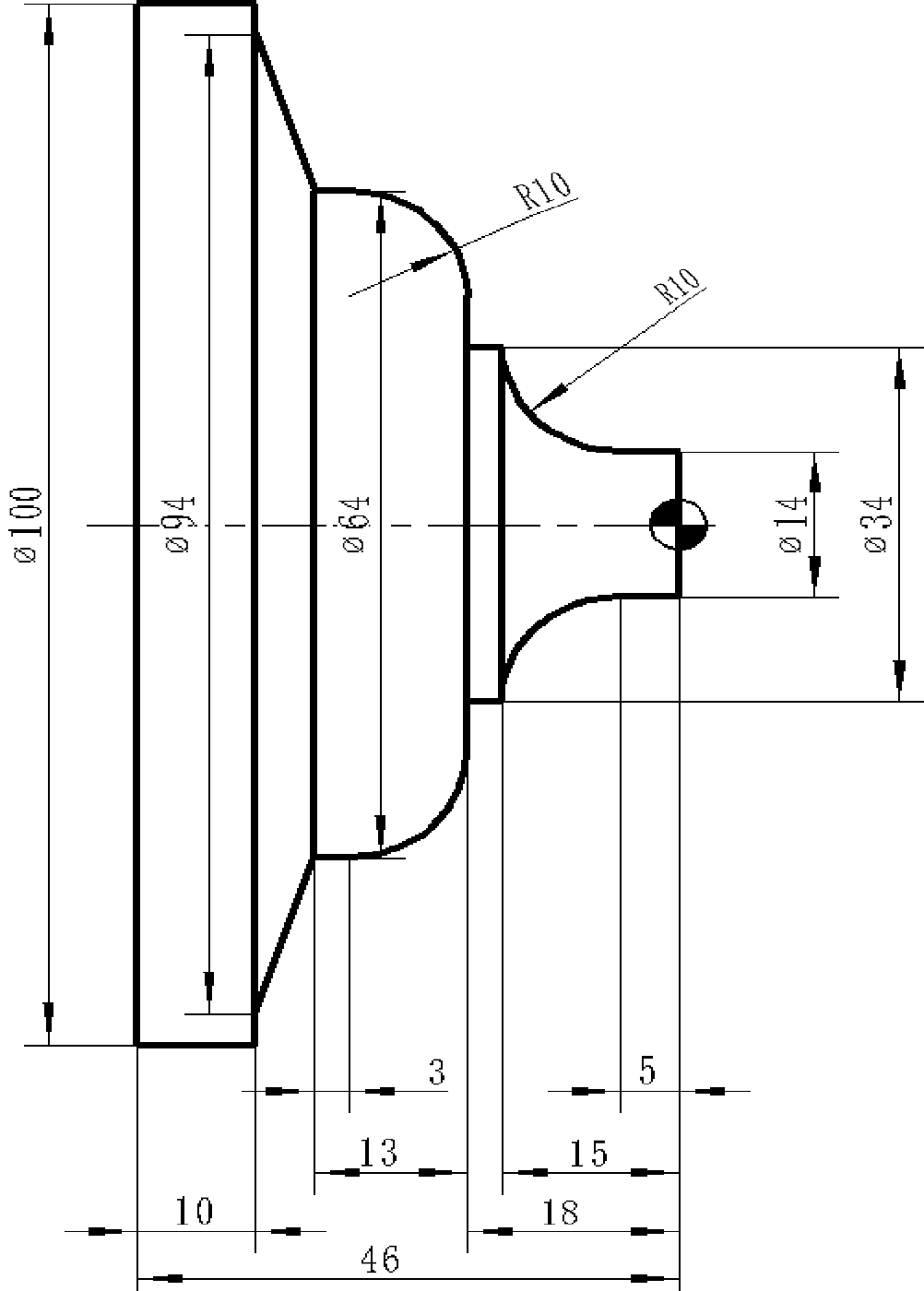
程序内容 |
说明 |
备注 |
---|---|---|
O1 |
程序名称 |
|
N10 T0101 |
选择1号刀具 |
|
N20 M03 S500 G98 |
设定主轴转速,设定每分进给量 |
|
N30 G00 X150 Z100 |
快速定位 |
|
N40 X107 Z5 |
定位至循环点 |
|
N50 G72 U2 R1 |
设定切深2mm,退刀1mm |
|
N60 G72 P70 Q170 U0.5W0.1F100 |
设定精加工循环为N70至N170,并留精加工余量直径方向为0.5mm,长度方向为0.1mm,粗加工进给速度为100mm每分钟。 |
|
N70 G00 Z-46 |
精加工轮廓 |
|
N80 G01 X100 F50 |
精加工轮廓 |
|
N90 G01 Z-36 |
精加工轮廓 |
|
N100 X94 |
精加工轮廓 |
|
N110 X64 Z-31 |
精加工轮廓 |
|
N120 Z-28 |
精加工轮廓 |
|
N130 G03 X44 Z-18 R10 |
精加工轮廓 |
|
N140 G01 X34 |
精加工轮廓 |
|
N150 Z-15 |
精加工轮廓 |
|
N160 G02 X14 Z-5 R10 |
精加工轮廓 |
|
N170 G01 Z5 |
精加工轮廓 |
|
N180 G00 X150 Z100 M05 |
快速退回,主轴停转 |
|
N190 M30 |
程序结束 |
(三)轮廓车削复合循环指令(G73)
1.格 式
G73 U(△i) __W(△k)__ R(△d)__
G73 P(ns)__ Q(nf) __U(△u)__ W(△w) __F__
2.说 明
△i:X向最大总切削深度,半径值。
△k:Z向最大总切深量。
△d:重复加工次数。
ns:精加工路径第一程序段(即图中的AA')的顺序号。
nf:精加工路径最后程序段(即图中的B‘B)的顺序号。
△u:X 方向精加工余量,直径值,加工孔时为负值。
△w:Z 方向精加工余量的距离及方向。
3.轨迹动作
如图2.2.18所示。
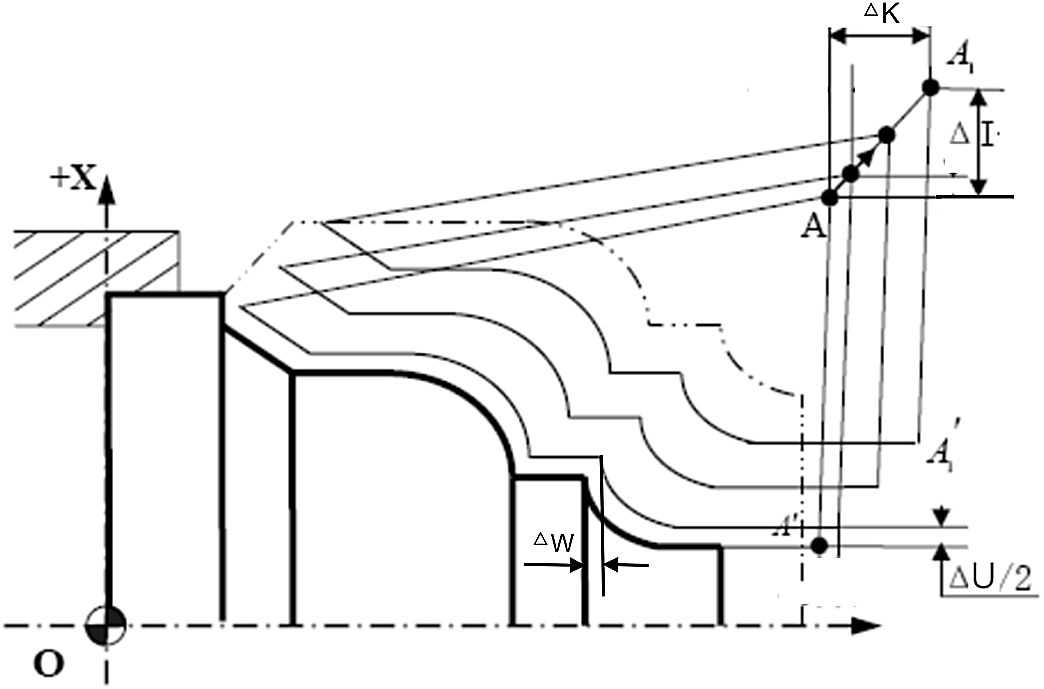
4.指令应用
如图2.2.19所示,毛坯尺寸为Φ60×120,用G73编程,编写出数控程序见表2-2-10所示。
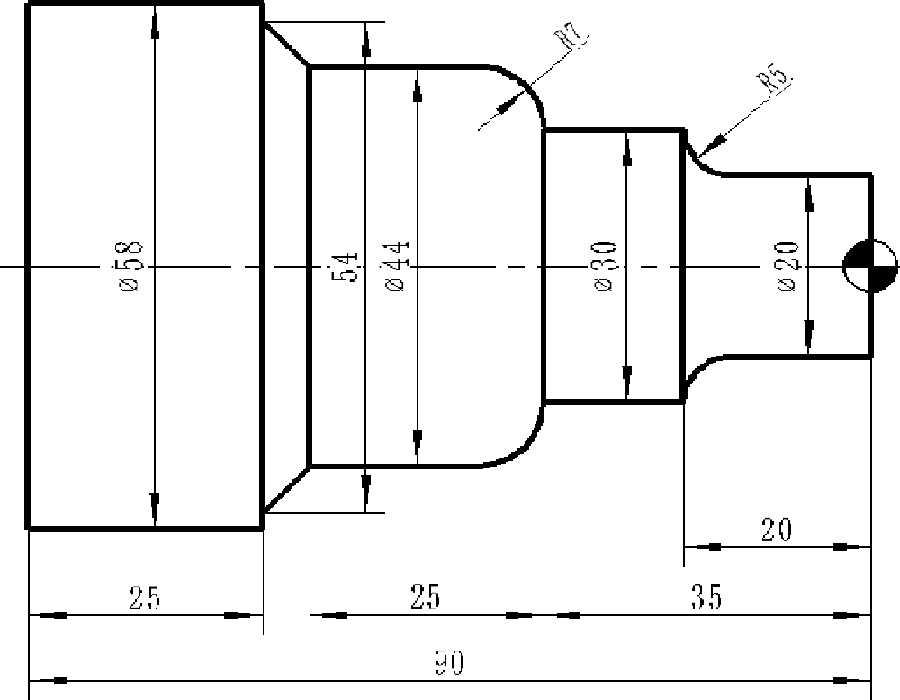
程序内容 |
说明 |
备注 |
---|---|---|
O1 |
程序名称 |
|
N10 T0101 |
选择1号刀具 |
|
N20 M03 S500 G98 |
设定主轴转速,设定每分进给量 |
|
N30 G00 X100 Z100 |
快速定位 |
|
N40 X65 Z5 |
定位至循环点 |
|
N50 G73 U5 W5 R5 |
设定切深2mm,退刀1mm |
|
N60 G73 P70 Q160 U0.2 W0.1F100 |
设定精加工循环为N70至N160,并留精加工余量直径方向为0.5mm,长度方向为0.1mm,粗加工进给速度为100mm每分钟。 |
|
N70 G00 X20 |
精加工轮廓 |
|
N80 G01 Z-15 F50 |
精加工轮廓 |
|
N90 G02 X30 Z-20 R5 |
精加工轮廓 |
|
N100 G01 Z-35 |
精加工轮廓 |
|
N110 G03 X44 Z-42R7 |
精加工轮廓 |
|
N120 G01 Z-60 |
精加工轮廓 |
|
N130 X54 Z-70 |
精加工轮廓 |
|
N140 X58 |
精加工轮廓 |
|
N150 Z-90 |
精加工轮廓 |
|
N160 G01 X65 |
精加工轮廓 |
|
N170 G00 X100 Z100 M05 |
快速退回,主轴停转 |
|
N180 M30 |
程序结束 |
(四)螺纹车削复合循环指令(G76)
1.格 式
G76 P(m)__( r)__(a)__ Q(△dmin)__ R(d)__
G76 X(u)__ Z(w)__ R(i)__ P(k)__ Q(△d)__ F(l)__
2.说 明
m:精车削次数,必须用两位数,范围从01-99。
r:螺纹末端倒角量,必须用两位数表示,范围从00-99。
a:刀尖的角度。
△dmin :最小切削深度。
d:精加工余量,孔加工时为负。
X,Z:绝对值编程时,为有效螺纹终点C 的坐标。
U,W:增量值编程时,为有效螺纹终点C 相对于循环起点A 的有向距离。
i:螺纹两端的半径差。
k:螺纹高度。
△d:第一次切削深度(半径值)。
F(l):螺纹导程。
每次递减切削深度如图2.2.20所示。
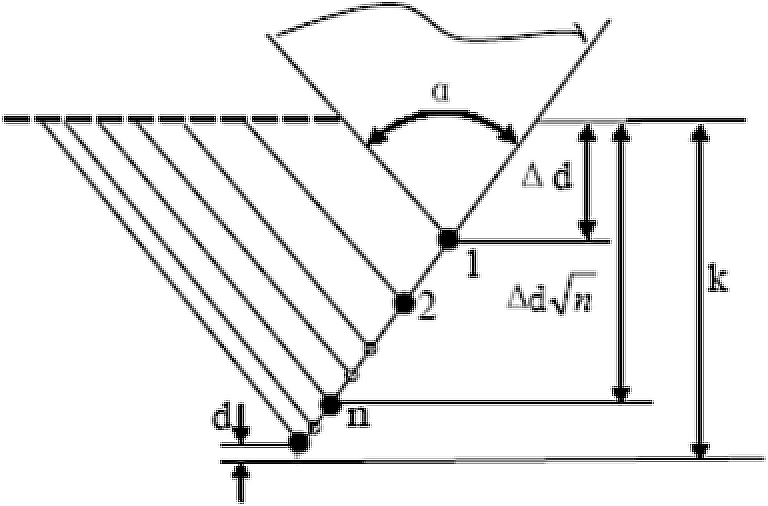
4.轨迹动作
如图2.2.21所示。
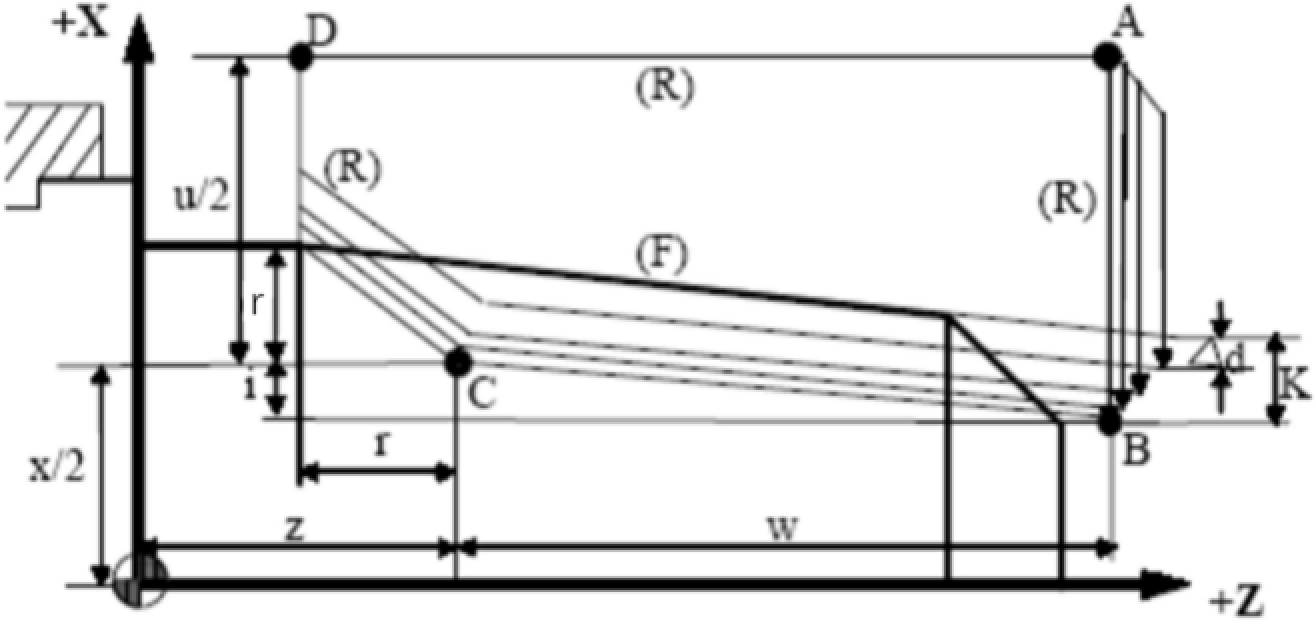
5.指令应用
如图2.2.22所示,毛坯尺寸为Φ50×100,用G76编程,编写出下图的螺纹数控程序见表2-2-11所示。
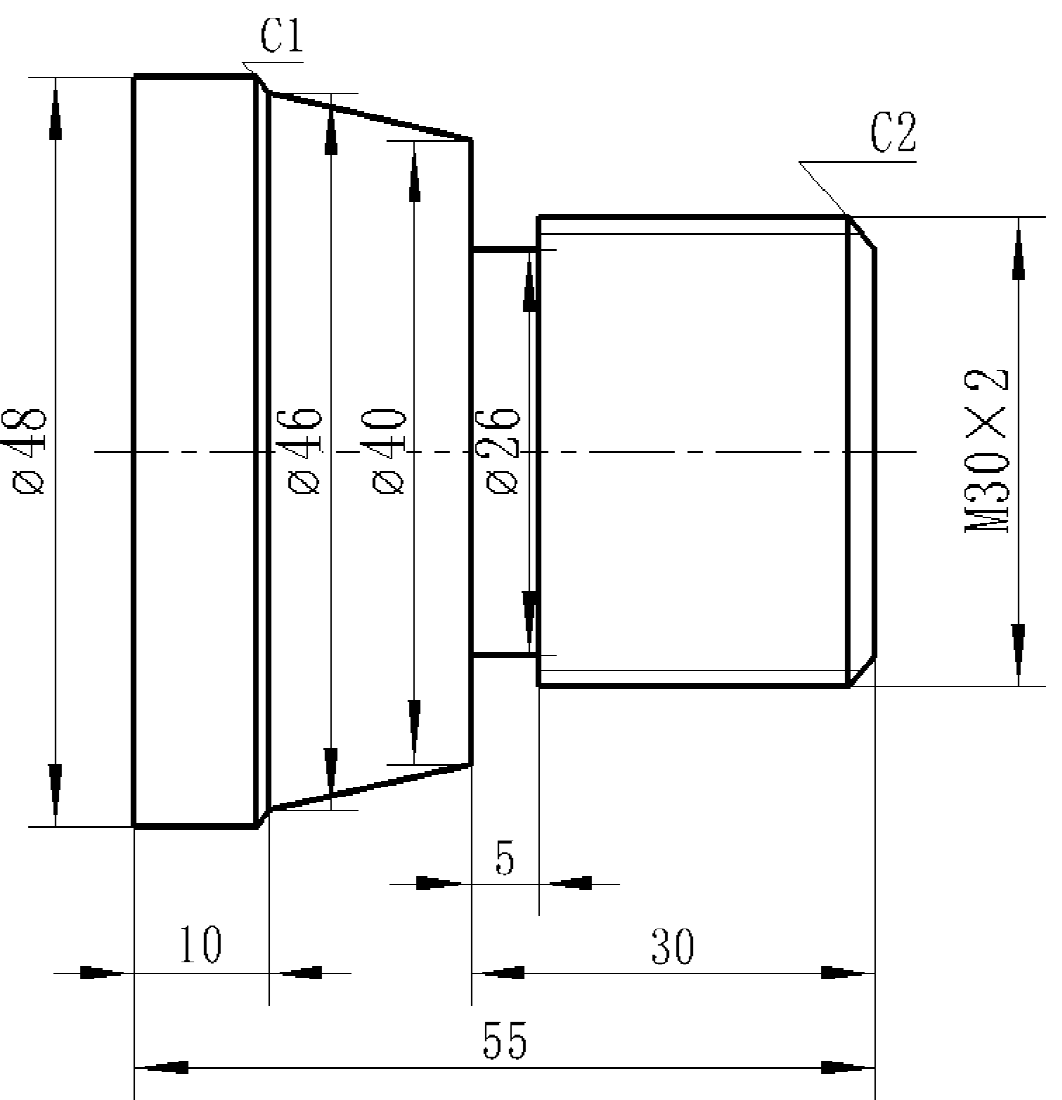
程序内容 |
说明 |
备注 |
---|---|---|
O1 |
程序名称 |
|
N10 T0303 |
选择3号刀具 |
|
N20 M03 S500 G98 |
设定主轴转速,设定每分进给量 |
|
N30 G00 X100 Z100 |
快速定位 |
|
N40 X35 Z5 |
定位至循环点 |
|
N50 G76 P010260 Q100 R0.1 |
设定螺纹循环参数 |
|
N60 G76 X27.4 Z-27 R0 P1300 Q0.5 F2 |
设定螺纹牙底参数 |
|
N170 G00 X100 Z100 M05 |
快速退回,主轴停转 |
|
N180 M30 |
程序结束 |
(五)精车循环指令
G71,G72,G73 粗切后,用下面的指令实现精加工。
1.格 式
G70 P(ns)__ Q(nf)__
2.说 明
(ns):精加工程序第一个程序段的顺序号。
(nf):精加工程序最后一个程序段的顺序号。
3.注意事项
(1) 在 G71,G72,G73 程序段中规定的 F,S 和 T 功能无效,但在执行G70 时顺序号“ns”和“nf”之间指定的 F,S 和 T 有效。
(2) 当 G70 循环加工结束时,刀具返回到起点并读下一个程序段。
(3) G70 到 G73 中 ns 到 nf 间的程序段不能调用子程序。
五、刀具补偿功能
(一)刀尖圆弧半径补偿功能
1.格 式
G40/G41/G42 G00/G01__ X__ Z__
刀尖半径加工过程如图2.2.23所示。
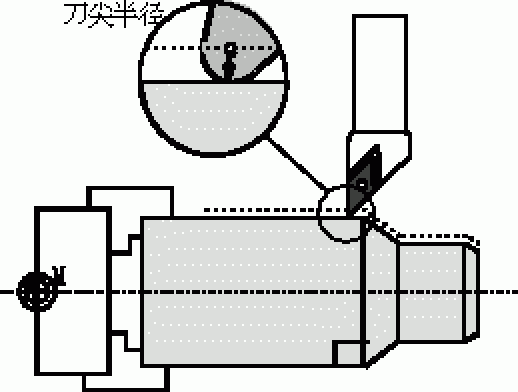
2.说 明
G41:左刀补,刀具从程序路径左侧移动。
G42:右刀补,刀具从程序路径右侧移动。
G40:取消补偿。
补偿的原则取决于刀尖圆弧中心的动向,它总是与切削表面法向里的半径矢量不重合。因此,补偿的基准点是刀尖中心。通常,刀具长度和刀尖半径的补偿是按一个假想的刀刃为基准,因此为测量带来一些困难。把这个原则用于刀具补偿,应当分别以 X 和 Z 的基准点来测量刀具长度刀尖半径 R,以及用于假想刀尖半径补偿所需的刀尖形式数(0-9),如图2.2.24所示。
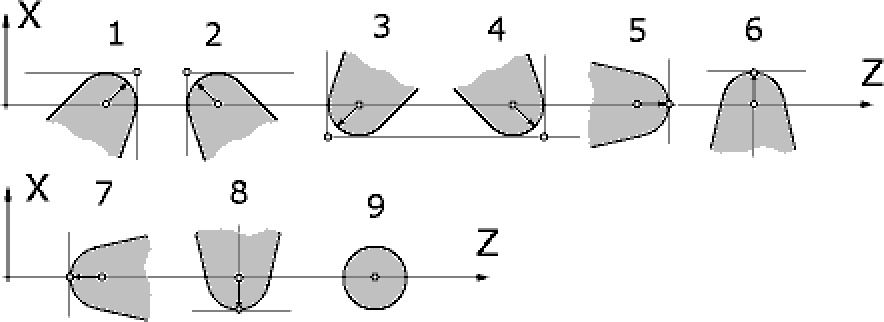
3.注意事项
“刀尖半径偏置” 应当用 G00 或者 G01功能来下达命令或取消。不论这个命令是不是带圆弧插补,刀不会正确移动,导致它逐渐偏离所执行的路径。因此,刀尖半径偏置的命令应当在切削进程启动之前完成; 并且能够防止从工件外部起刀带来的过切现象。反之,要在切削进程之后用移动命令来执行偏置的取消过程。
评价内容 |
分值 |
自评(20%) |
互评(20%) |
教师评价(60%) |
得分 |
|
---|---|---|---|---|---|---|
工作过程 |
学习态度 |
20 |
||||
通识知识 |
20 |
|||||
关键能力 |
20 |
|||||
工作成果 |
成果质量 |
40 |
||||
合计 |
1.充分利用多媒体教学,配合动画演示,解决了数控车常用编程指令教学的重点,结合小组讨论学习法,克服了本节的教学难点。
2.“精益求精的大国工匠精神”贯穿教学全过程,切实做到了对学生素质目标的培养。
3.学生在完成任务的过程,鼓励学生担当不同的角色,利用角色扮演法,增强学生的工作责任心,增强小组成员间的协作能力,组织能力和管理能力,调动学生的积极性,充分体现以学生为主体的教学特点。
4.学生对数控车常用编程指令的应用方法有待进一步的提高,以便快速编写出数控程序。