知识目标:了解数控车床仿真软件的功能,掌握数控仿真软件的使用方法,掌握数控仿真软件的各项功能。
一、斯沃模拟仿真软件基本使用方法介绍
(一 )数控车床FANUC系统操作面板
数控车床FANUC系统操作面板主要包括显示器、MDI键盘、“急停”按钮、功能键和机床控制面板几部分,界面如图3.1.1所示。
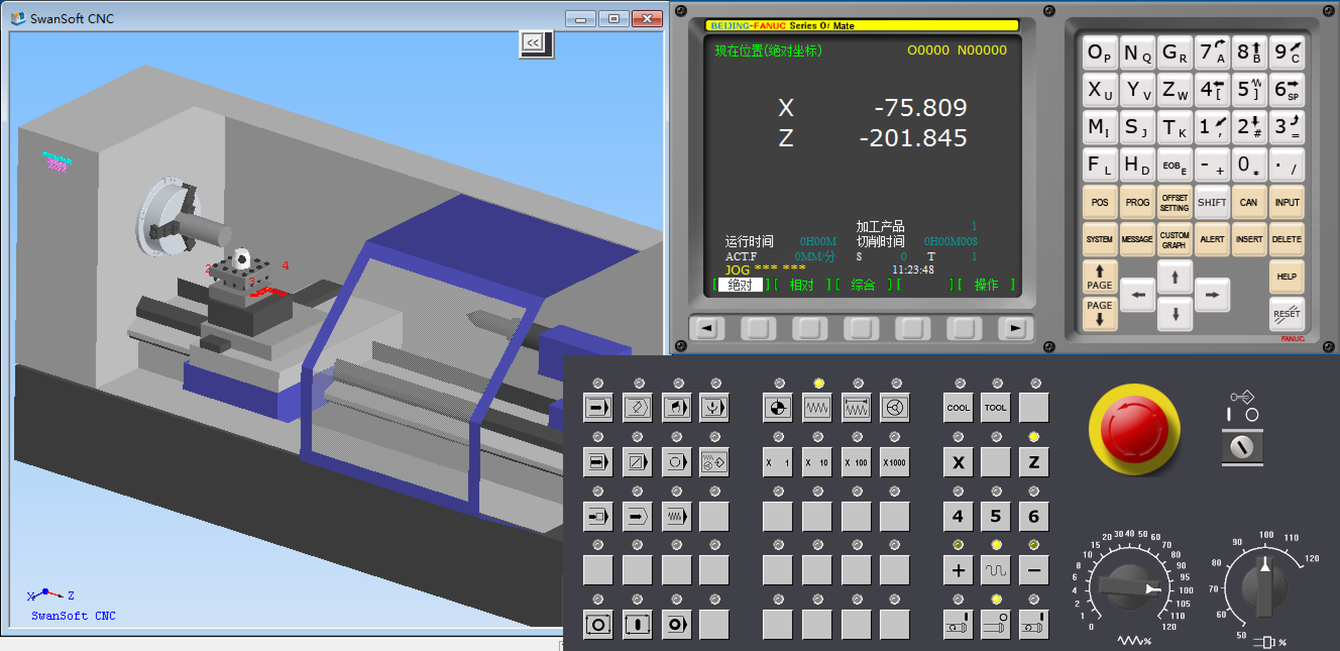
1.MDI键盘(地址/数字键)
MDI键盘用于字母、数字及其他字符的输入和修改,使用方法与计算机键盘相应键相似。键盘如图3.1.2所示。
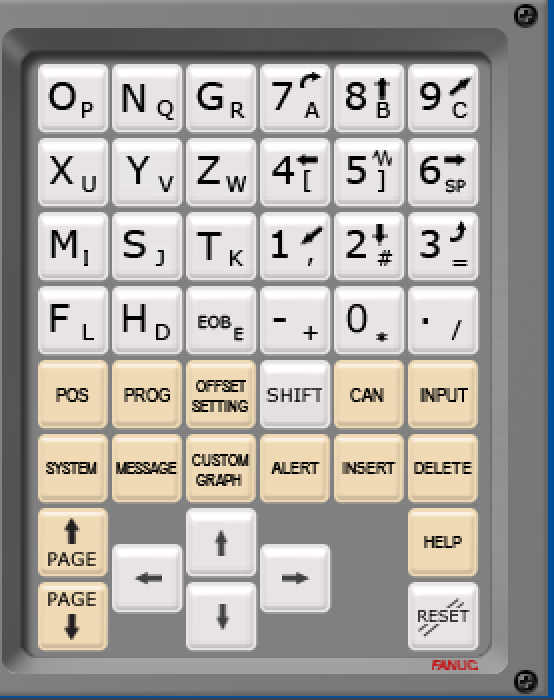
2.机床控制面板
车床手动操作主要由控制面板各功能键完成。
机床控制面板如图3.1.3所示。
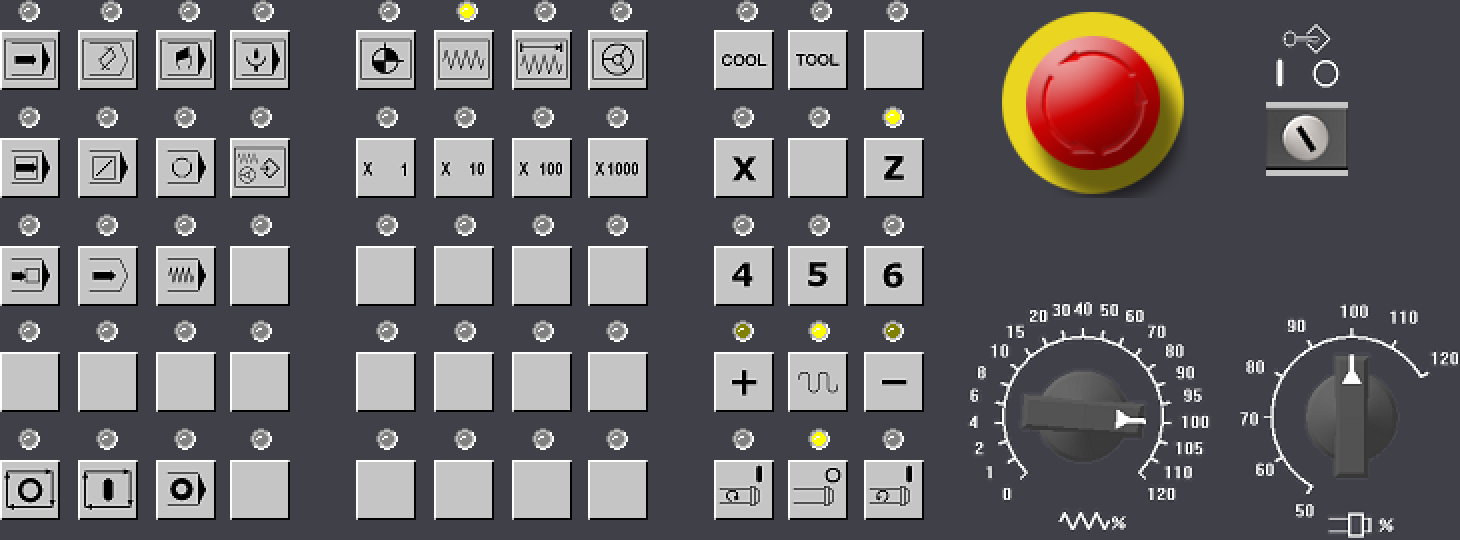
(1)点动进给。按一下手动按键,指示灯亮系统处于点动运行方式可点动移动机床坐标轴(下面以点动移动X轴为例说明)。
按压“+X”或“-X”按键指示灯亮,X轴将产生正向或负向连续移动;松开“+X” 或“-X”按键指示灯灭,X轴即减速停止用同样的操作方法使用“+Y”“-Y”“+Z”“–Z”按键可以使Y轴、Z轴产生正向或负向连续移动。
(2)点动快速移动。在点动进给时,若同时按压快进按键则产生相应轴的正向或负向快速运动。
(3)点动进给速度选择。在点动进给时,进给速率为系统参数最高快移速度的1/3乘以进给修调,选择的进给倍率、点动快速移动的速率为系统参数最高快移速度乘以快速修调选择的快移倍率,进给或快速修调倍率被置为100% 按一下“+”按键修调倍率递增10% ,按一下“-”按键修调倍率递减10%。
(4)增量进给。按一下控制面板上的增量按键指示灯亮,系统处于增量进给方式,可增量移动机床坐标轴(下面以增量进给X轴为例说明)。
按一下“+X ”或“-X”按键,指示灯亮X轴将向正向或负向移动一个增量值;再按一下“+X”或“-X”按键,X轴将向正向或负向继续移动一个增量值。用同样的操作方法。使用“+Z”“-Z”按键可以使Z轴向正向或负向移动一个增量值。
(5)主轴正反转及停止。在手动方式下,按一下主轴正转按键,指示灯亮,主电机以机床参数设定的转速正转; 按一下主轴反转按键,指示灯亮,主电机以机床参数设定的转速反转; 按一下主轴停止按键,指示灯亮,主电机停止运转。
(6)主轴速度修调。主轴正转及反转的速度,可通过主轴修调调节按压主轴修调右侧的100% ,按键指示灯亮,主轴修调倍率被置为100%, 按一下“+”,按键主轴修调倍率递增10%, 按一下“-”,按键主轴修调倍率递减10%,机械齿轮换挡时主轴速度不能修调。
(7) 机床锁住。机床锁住由机床控制面板上的机床锁住键完成。禁止机床所有运动在手动运行方式下按一下机床锁住按键,指示灯亮,再进行手动操作系统继续执行,显示屏上的坐标轴位置信息变化,但不输出伺服轴的移动指令所以机床停止不动。
(8) 轴锁住。Z 轴锁住由机床控制面板上的Z 轴锁住键完成。禁止进刀,在手动运行开始前按一下Z ,轴锁住按键指示灯亮,再手动移动Z 轴,Z 轴坐标位置信息变化,但Z 轴不运动。
(9)冷却启动与停止。在手动方式下,按一下冷却开/停冷却液开,默认值为冷却液关,再按一下又为冷却液关如此循环。
3.显示器和功能键
如图3.1.4所示。
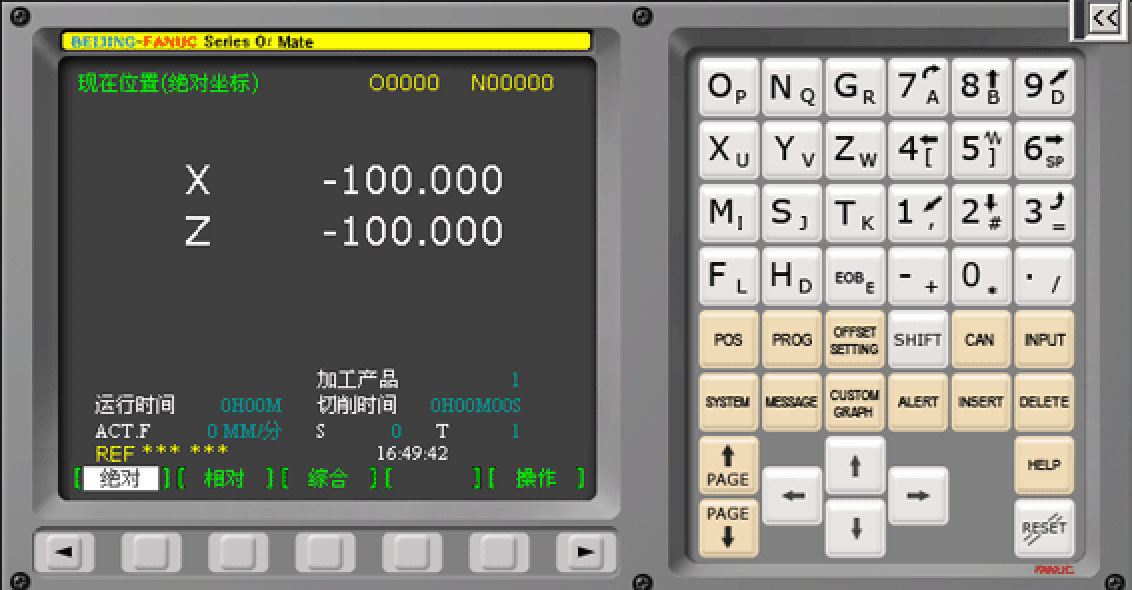
(1)图形显示窗口。可以根据需要,用功能键F9设置窗口的显示内容。
(2)菜单命令条。通过菜单命令条中的功能键F1~F10 来完成系统功能的操作。每个主菜单下又由多个子菜单组成。
(3)运行程序索引。
(4)自动加工中的程序名和当前程序段行号。
(5)选定坐标系下的坐标值。坐标系可在机床坐标系/工件坐标系/相对坐标系之间切换;显示值可在指令位置/实际位置/剩余进给/跟踪误差/负载电流/补偿值之间切换。
(6)工件坐标零点。工件坐标系零点在机床坐标系下的坐标。
(7)倍率修调。
1)主轴修调当前主轴修调倍率。
2)进给修调当前进给修调倍率。
3)快速修调当前快进修调倍率。
(8)辅助机能。自动加工中的M、S 、T 代码。
(9)当前加工程序行。当前正在或将要加工的程序段。
(10)当前加工方式系统运行状态及当前时间。
1)工作方式:系统工作方式根据机床控制面板上相应按键的状态可在自动(运行)、单段(运行)、手动(运行 )、增量(运行)、回零、急停、复位等之间切换。
2)运行状态:系统工作状态在“运行正常”和“出错” 间切换。
3)系统时钟:当前系统时间。
4.“急停”按钮
面板右上角最大的红色按钮,主要用于控制操作面板的开关,可随时停止机床的运动。
(二)选择机床和数控系统
进入斯沃仿数控仿真软件,选择FANUC-0iT系统如图3.1.5(a)和(b)图所示。
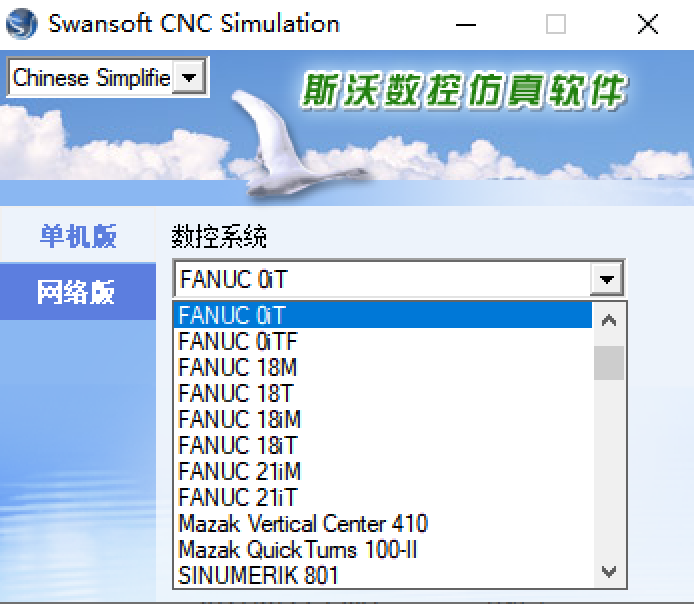
(三)刀具选择
进入数控加工仿真系统,在工艺流程主菜单进入车刀刀库子菜单下选择各种刀具,并设置刀具相应各参数如图所示,然后选择确定按钮,就可以将各把车刀装在刀架上, 选择刀具如图3.1.6所示。
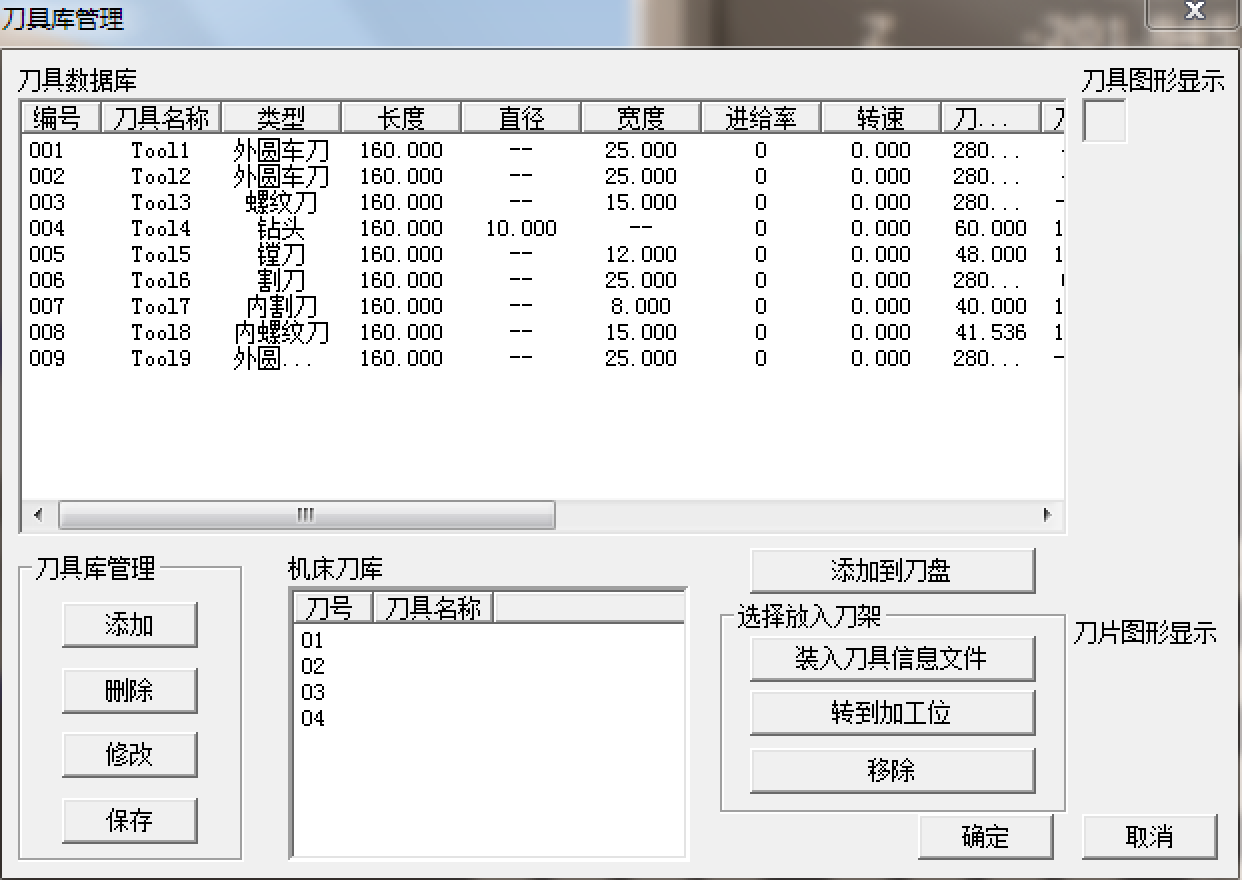
当默认刀具参数不符合要求时,可以对刀具进行修改,如图3.1.7所示。
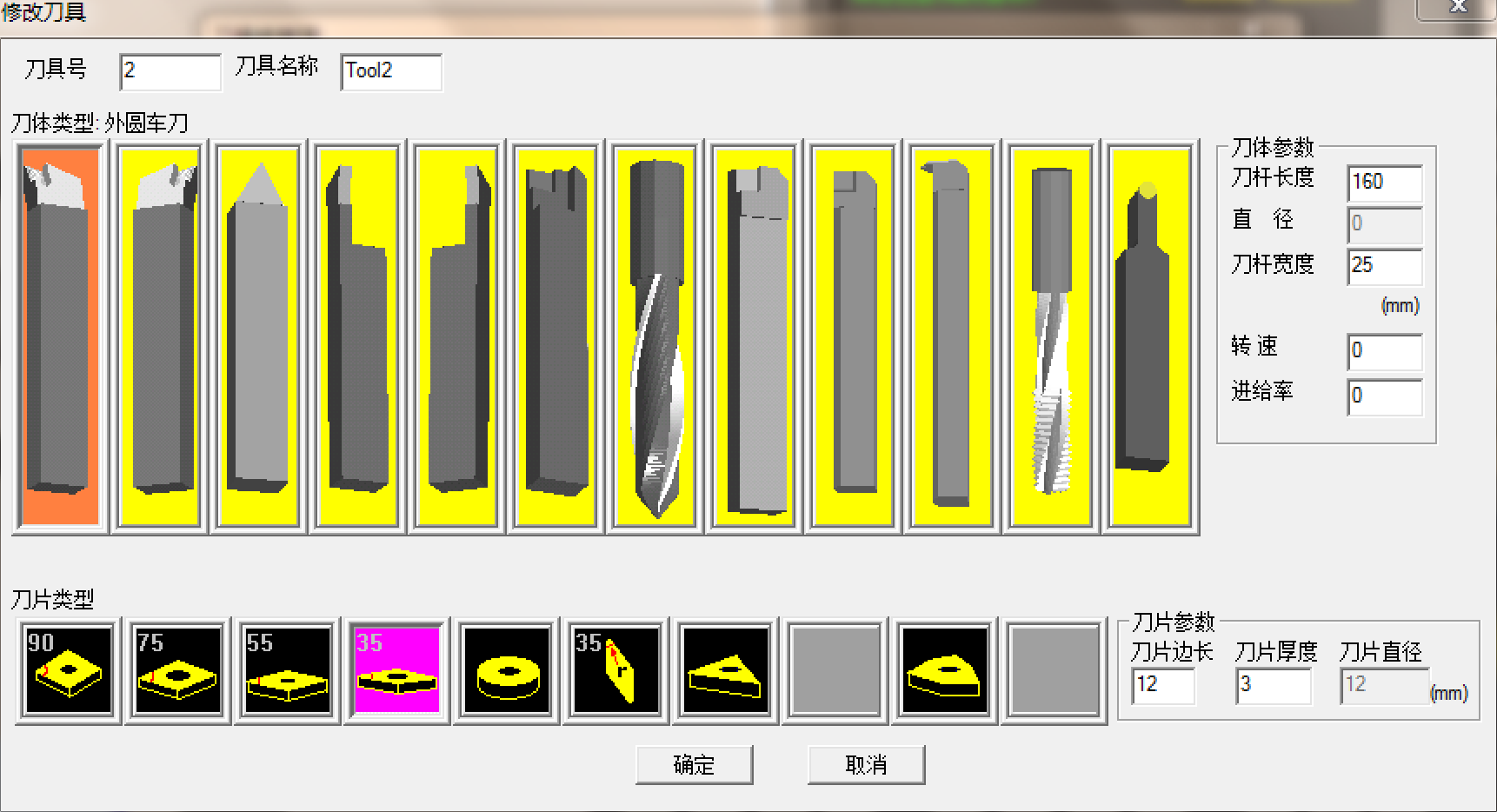
刀具选择并修改好后,将刀具放置1号刀位,单击确定后,显示如图3.1.8所示。
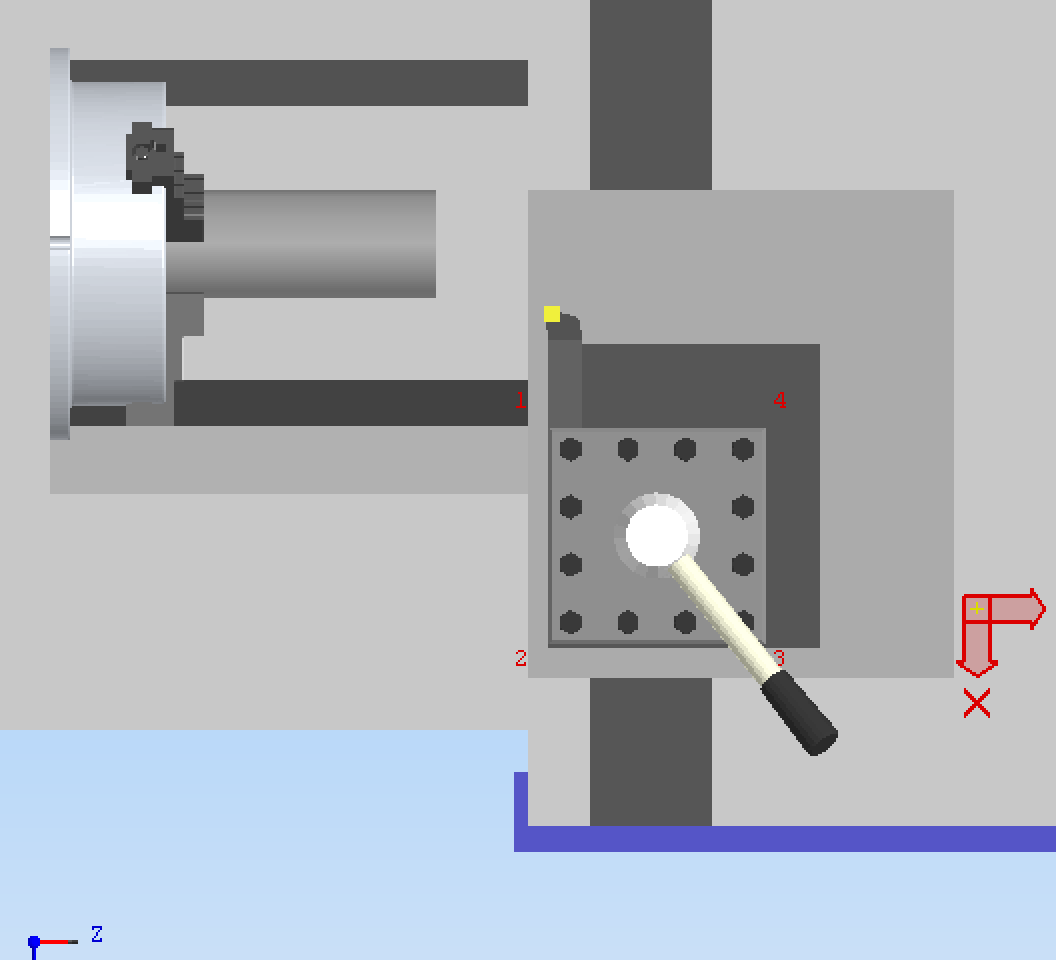
(四)毛坯选择
进入数控加工仿真系统,在工艺流程主菜单进入选择毛坯子菜单下按下新毛坯按钮,选择毛坯外径、内径、高、材料和夹具如图3.1.9所示,然后按确定按钮,再选择安装此毛坯即可将该毛坯装在卡盘上,最后调整伸出长度后加紧,如图3.1.9所示。
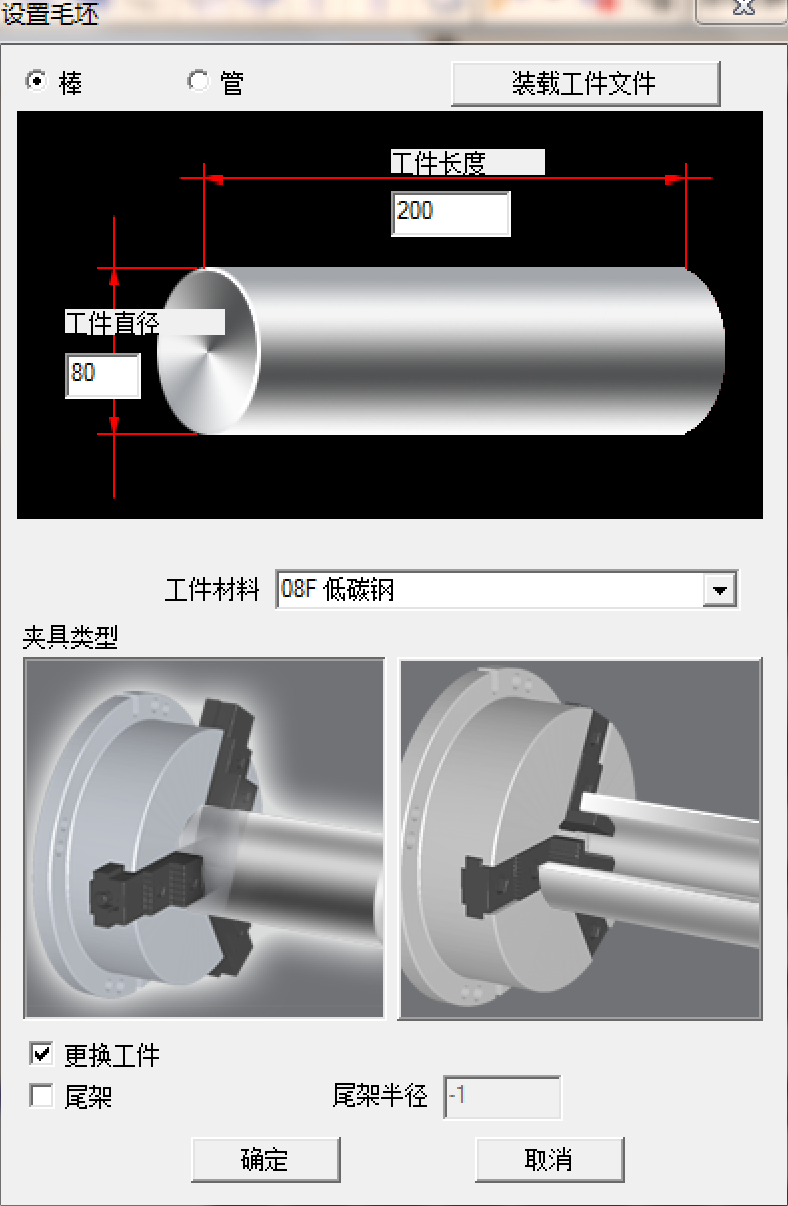
(五)数控车床模拟对刀方法介绍
1.常用数控刀具的几何形状
常用数控车削刀具如图3.1.10所示。常用外轮廓刀具如图3.1.10(a)所示。
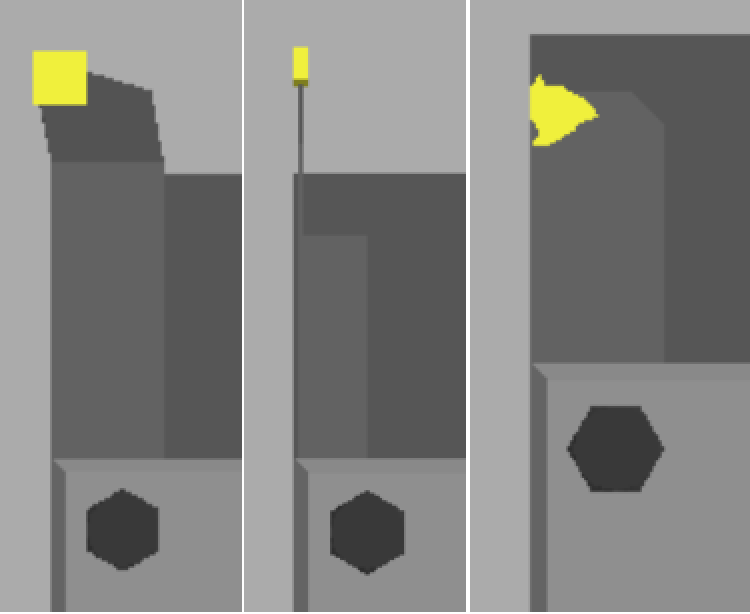
常用内轮廓刀具如图3.1.10(b)所示。

2.工件的装夹、刀具安装与操作
(1)工件装夹。
数控车床的夹具主要有卡盘和尾座。在工件安装时,首先根据加工工件尺寸选择卡盘,再根据其材料及切削余量的大小调整好卡盘卡爪夹持直径、行程和夹紧力。如有需要,可在工件尾座打中心孔,用顶尖顶紧。使用尾座时应注意其位置、套筒行程和夹紧力的调整。工件要留有一定的夹持长度,其伸出长度要考虑零件的加工长度及必要的安全距离。工件中心尽量与主轴中心线重合。如所要夹持部分已经经过加工,必须在外圆上包一层铜皮,以防止外圆面损伤。
(2)刀具的安装。
根据工件及加工工艺的要求选择合理的刀具和刀片。首先将刀片安装在刀杆上,再将刀杆依次安装到刀架上,之后通过刀具干涉和加工行程图检查刀具安装尺寸。
(3)注意事项。
1)安装前保证刀杆及刀片定位面清洁,无损伤。
2)将刀杆安装在刀架上时,应保证刀杆方向正确。
3)安装刀具时需注意使刀尖等高于主轴的回转中心。
4)车刀不能伸出过长,以免干涉或因悬伸过长而降低刀杆的。
(4)手动换刀。
数控车床的自动换刀装置,可通过程序指令使刀架自动转位,通过[MDI]和[自动]按钮加工程序均可,也可通过面板手动控制刀架换刀。
(5)对刀。(本操作过程需在仿真软件上边演示边讲述)
对刀的目的是确定编程原点在机床坐标系中的位置,对刀点可以设定在零件、夹具或机床上,对刀时应使对刀点与刀位点重合。虽然每把刀具的刀尖不在同一点上,但通过刀补,可使刀具的刀位点都重合在某一理想位置上。编程人员只按工件的轮廓编制加工程序即可,而不用考虑不同刀具长度和刀尖半径的影响。
1)T0101 外圆刀(1号刀)对刀。
①按下[MDI],进入[MDI]模式,在MDI 功能子菜单下,按F6 进入MDI 运行方式,通过操作面板在光标闪动处输入“T0101;M03 S500;”,按[Enter]键,将程序插入。再按[循环启动]按钮,执行程序,换1号刀,按使主轴正转,转速500r/min左右。
②在手动或增量状态下将刀具移至工件附近(靠近时倍率要小些),手动用1号刀车削外圆。切削一小段足够卡尺测量外径的长度后,保持X轴不变,按[+Z]向按键,使车刀沿+Z向退出,按下[主轴停]按钮,此时主轴停止转动。测量所切部分的外径,例如车削外径为56.1656mm,则进入[MDI],再按下[刀偏表]按钮,光标移至刀编号为0001的试切直径处,键盘输入对应的测量X值如56.1656, 然后按[Enter]键,完成1号刀X向对刀。试切外圆如图3.1.11所示。
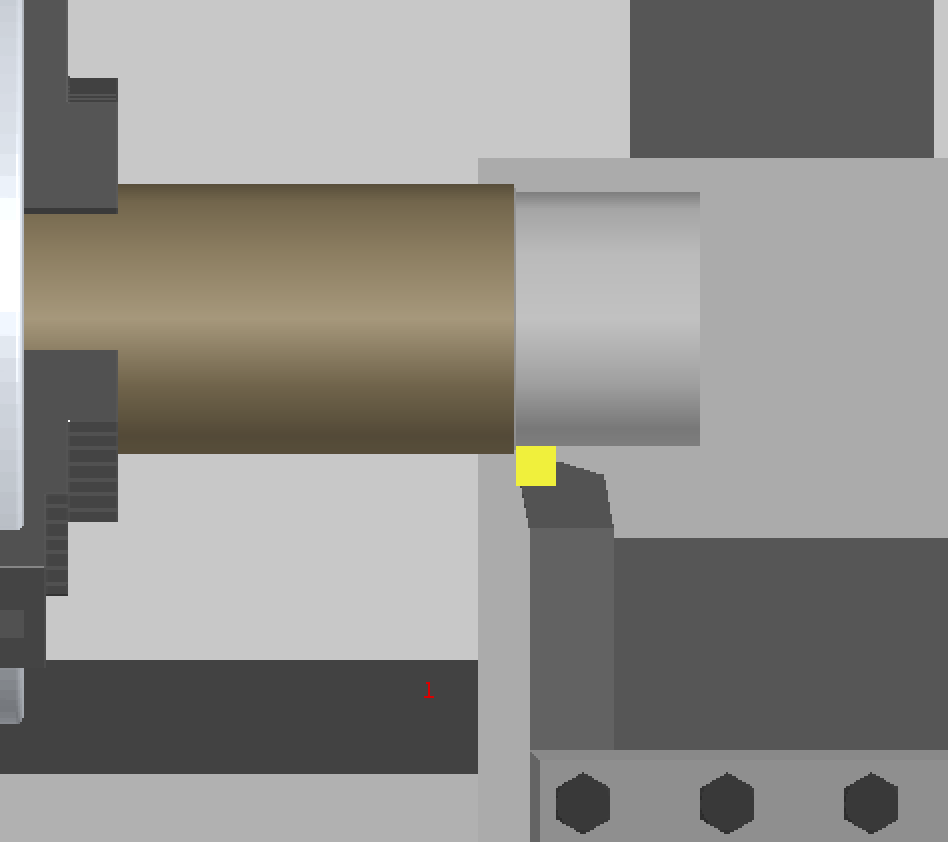
测量试切外圆直径如图3.1.12所示。
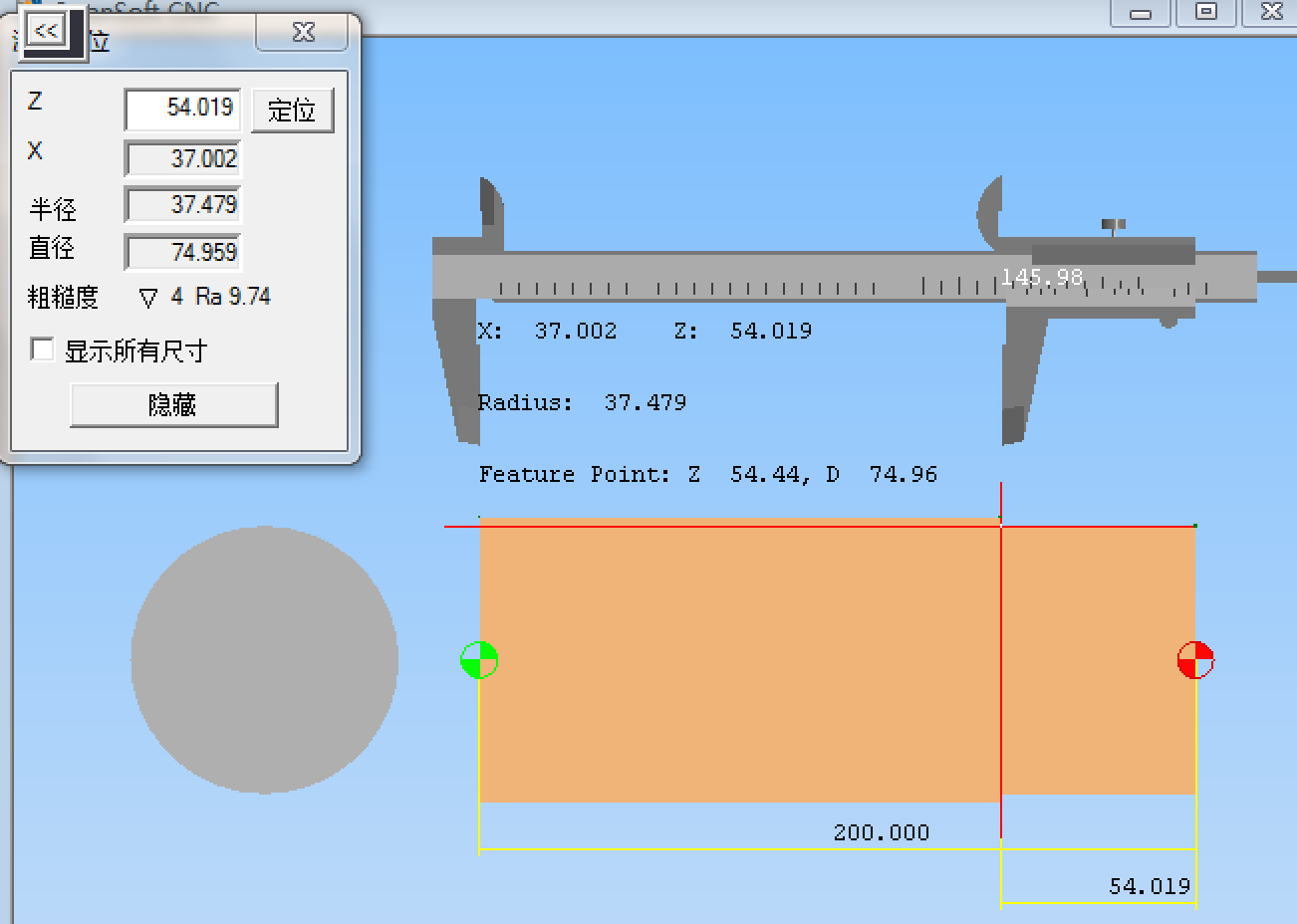
输入试切外圆直径,设置X向补正如图3.1.13所示。
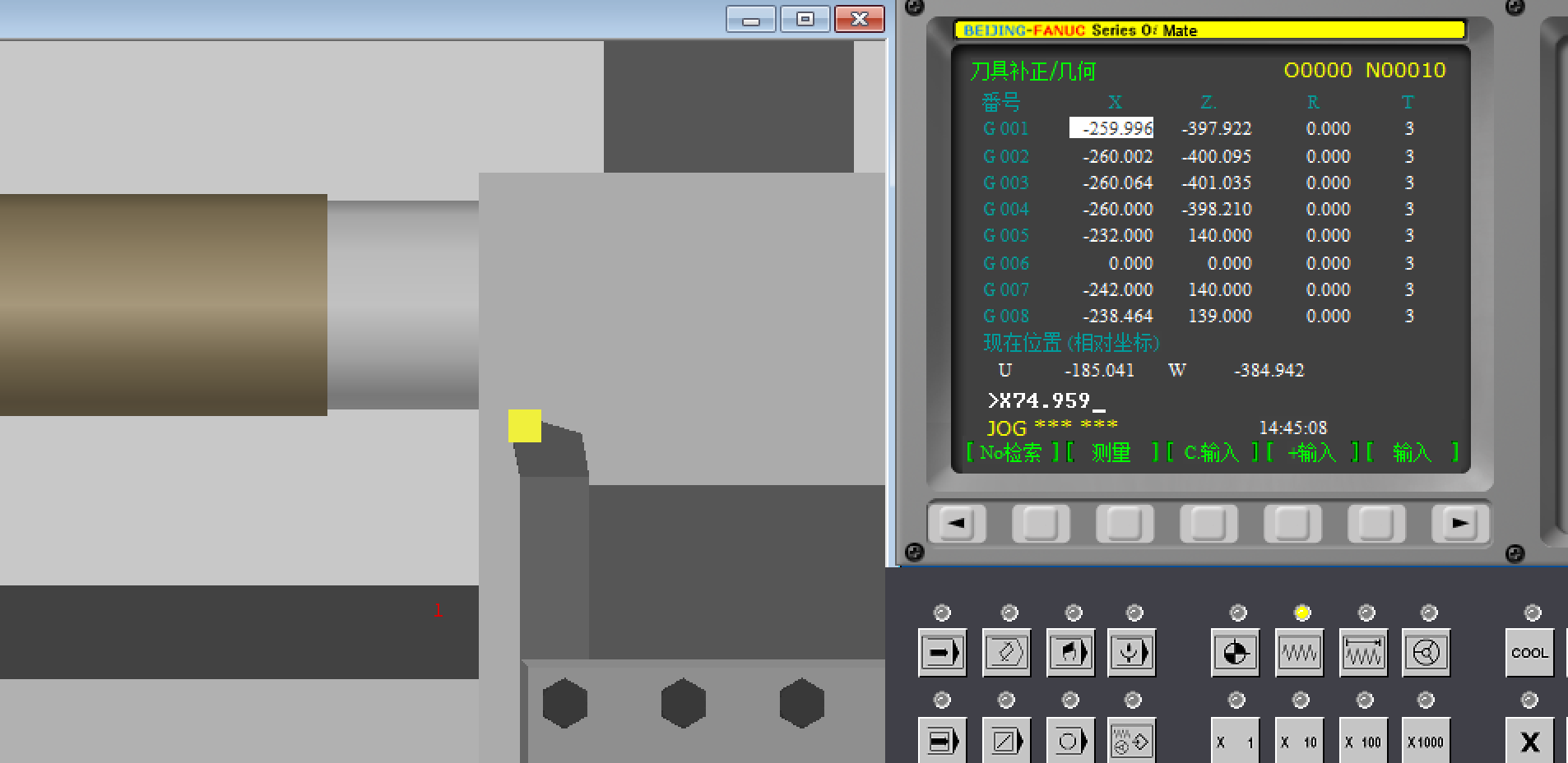
③再次启动主轴正转,切削端面,切削完毕,保持Z轴不变,按[+X]向按键,使车刀沿+X退刀,让主轴停止转动。
④进入刀偏表,光标移至刀编号为0001的试切长度处,键盘输入对应的Z值 “0”,然后按[Enter]键,即完成1号刀Z向对刀。如图3.1.14所示。
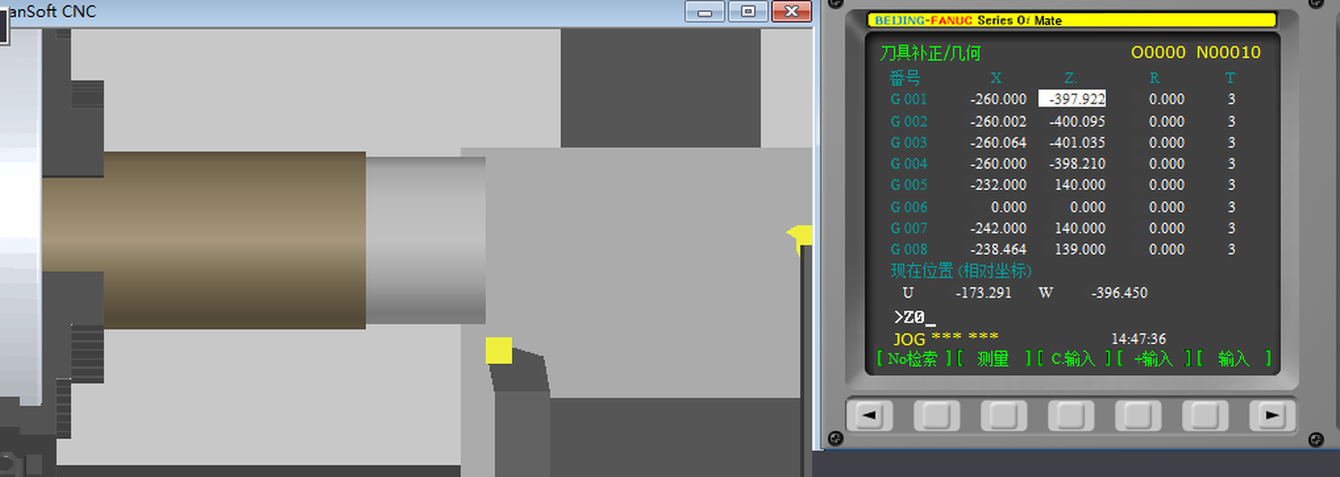
⑤1号刀对刀完毕,将刀架移开,退至换刀位置附近。
2)T0202 外切槽刀(2号刀)对刀。
①在MDI方式下,调2号刀,按[主轴正转]按钮,使主轴旋转。
②在手动方式下,将刀具移至工件附近,越近时倍率要越小,使2号刀的左刀尖(刀位点)与已加工好的工件端面平齐,并接触工件的外圆,听见摩擦声或有微小铁屑。
③在刀偏表中,光标移至刀编号为0002的试切直径和试切长度处,键盘分别输入对应的Z0和X56.1656 的数值,然后按[Enter]键,使主轴停止,完成2号刀Z向和X向对刀。
④完成2号刀对刀后,刀架移开,退到换刀位置,使主轴停转。
2号刀对刀如图3.1.15所示。
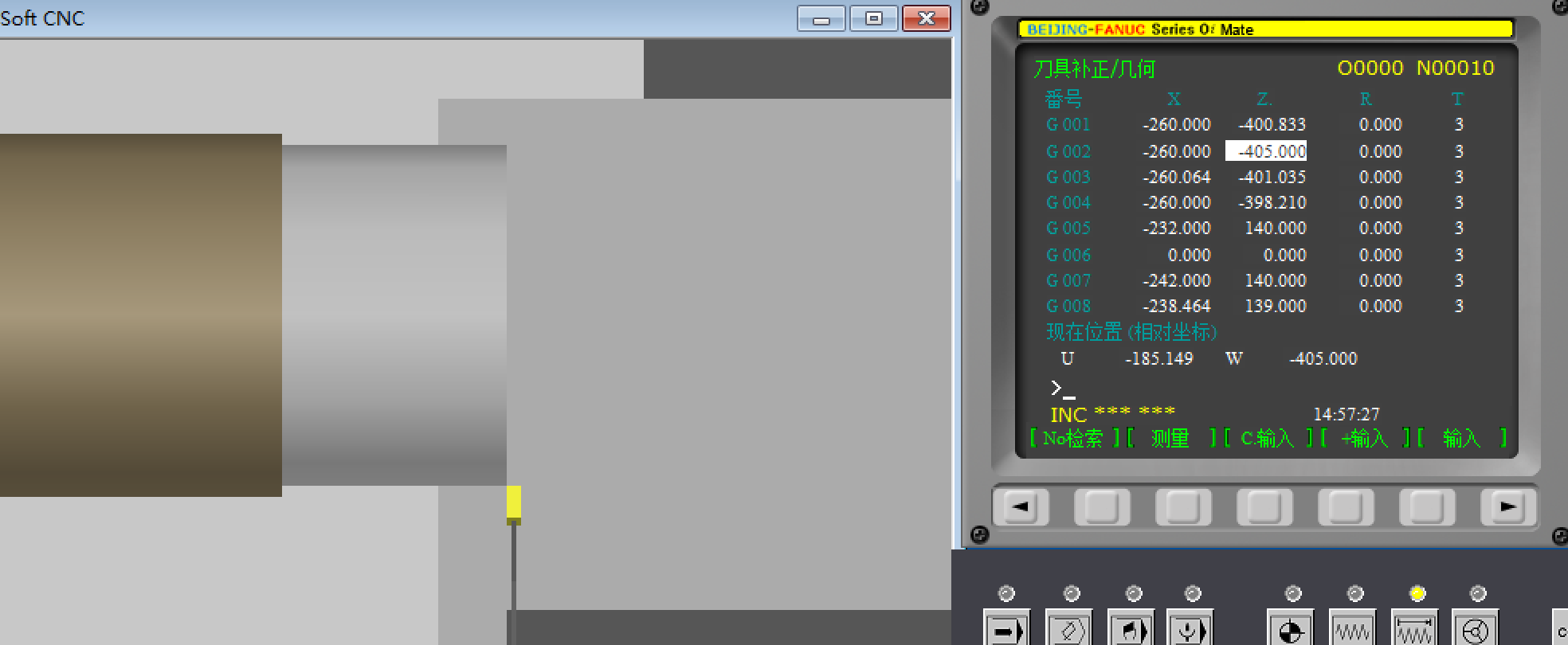
3)T0303 外螺纹刀(3号刀)对刀。
①在MDI方式下,调3号刀,按[主轴正转]按钮,使主轴旋转。
②在手动状态下将刀具移至工件附近,越近时倍率要越小,使3号刀的刀尖与已加工好的工件端面平齐,并接触工件的外圆,听见摩擦声或有微小铁屑。
③在刀偏表中,光标移至刀编号为0003的试切直径和试切长度处,键盘分别输入对应的Z0和X56.1656 的数值,然后按[Enter]键,使主轴停止,完成3号刀Z向和X向对刀。
④刀架移开,退到换刀位置,主轴停转。
3号刀对刀如图3.1.16所示。
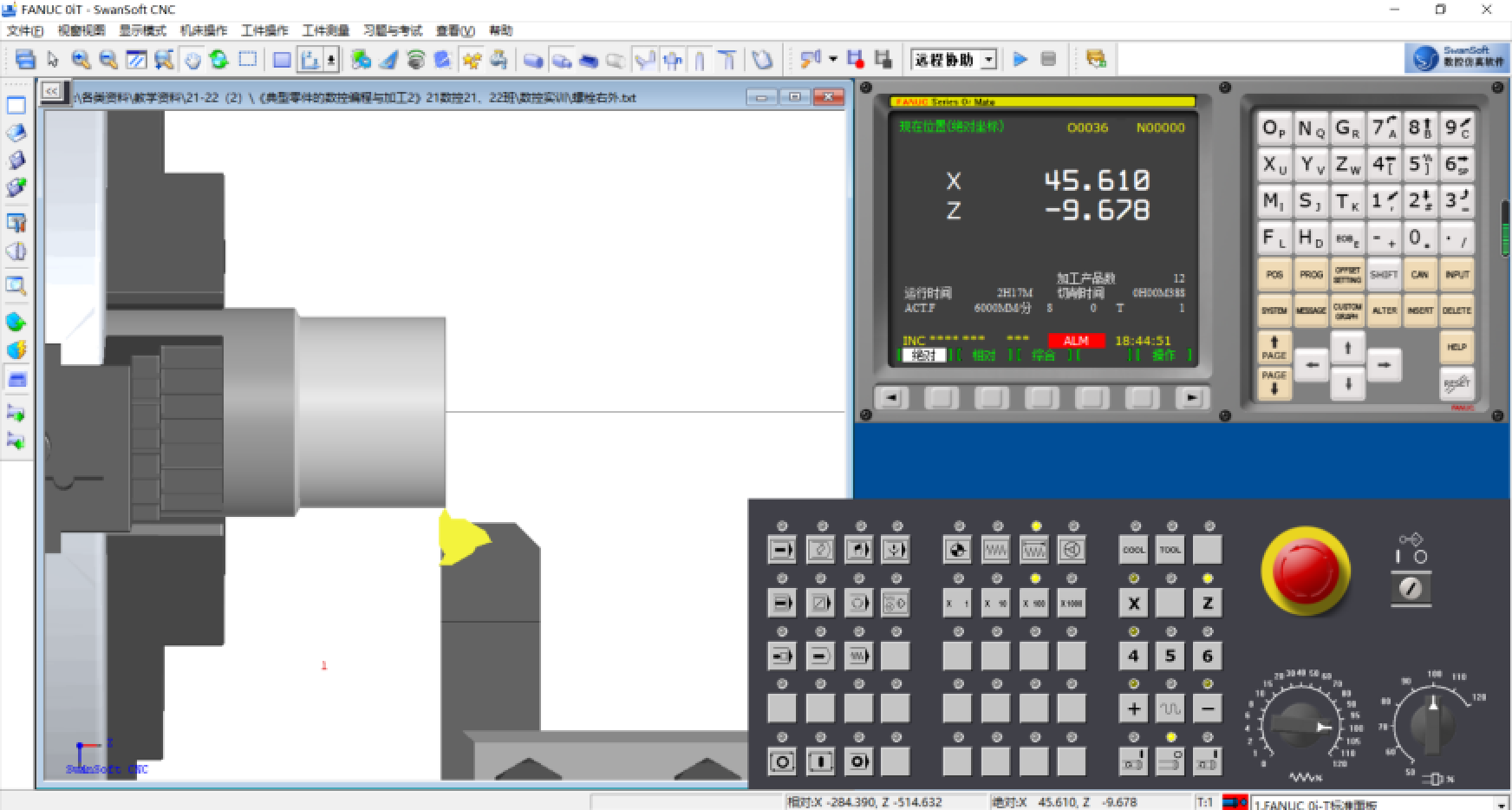
4)T0404 内孔刀(4号刀)对刀。
①按下[MDI],进入[MDI]模式,在MDI 功能子菜单下,按F6 进入MDI 运行方式,通过操作面板在光标闪动处输入“T0404;M03 S500;”,按[Enter]键,将程序插入。再按[循环启动]按钮,执行程序,换4号刀,按使主轴正转,转速500r/min左右。
②在手动或增量状态下将刀具移至工件附近(靠近时倍率要小些),手动用4号刀车削外圆。切削一小段足够卡尺测量外径的长度后,保持X轴不变,按[+Z]向按键,使车刀沿+Z向退出,按下[主轴停]按钮,此时主轴停止转动。测量所切部分的内径,例如车削内径为30.19mm,则进入[MDI],再按下[刀偏表]按钮,光标移至刀编号为0004的试切直径处,键盘输入对应的测量X值如27.164, 然后按[Enter]键,完成4号刀X向对刀。试切内孔如图3.1.17所示。
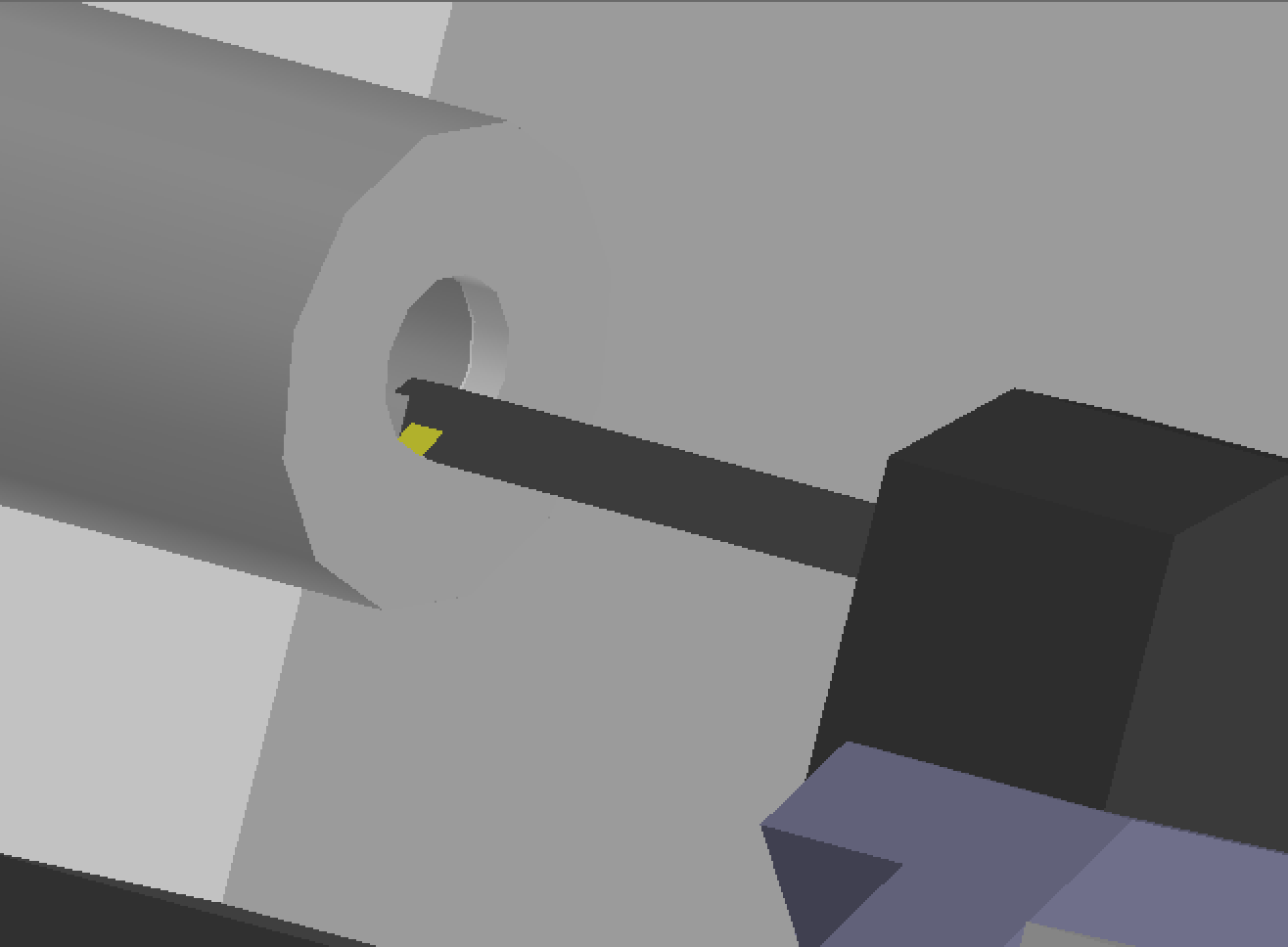
测量内孔直径如图3.1.18所示。
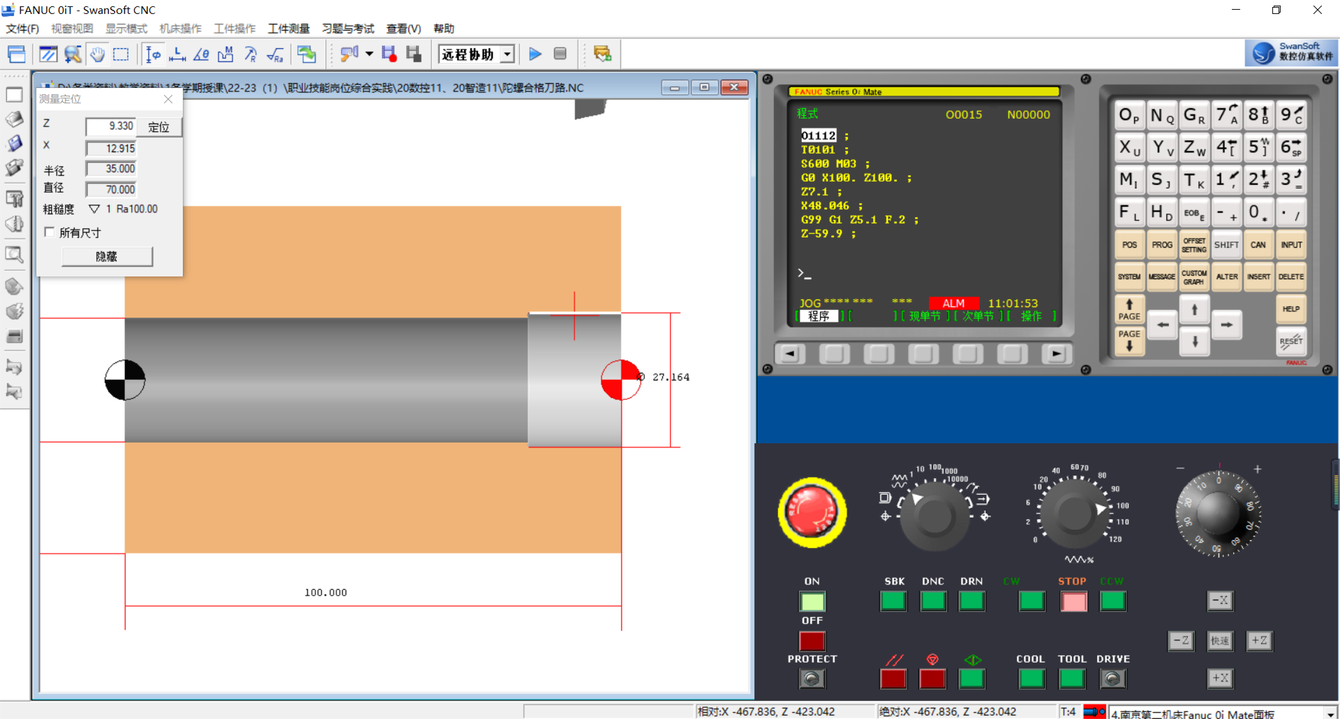
将测量出的内孔直径,输入到4号刀具的形状补偿表里,设置X向补正,如图3.1.19所示。
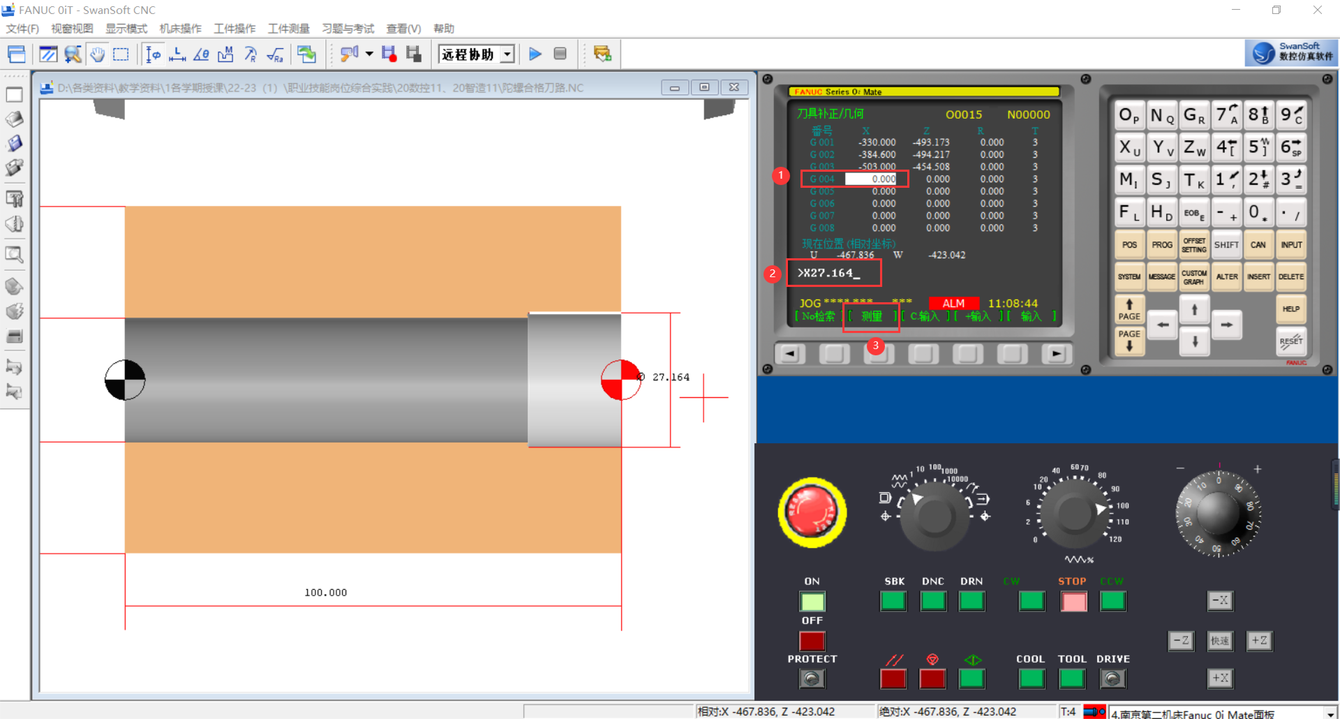
③再次启动主轴正转,切削端面,切削完毕,保持Z轴不变,按[+X]向按键,使车刀沿+X退刀,让主轴停止转动。
④进入刀偏表,光标移至刀编号为0004的试切长度处,键盘输入对应的Z值 “0”,然后按[Enter]键,即完成4号刀Z向对刀。如图3.1.20所示。
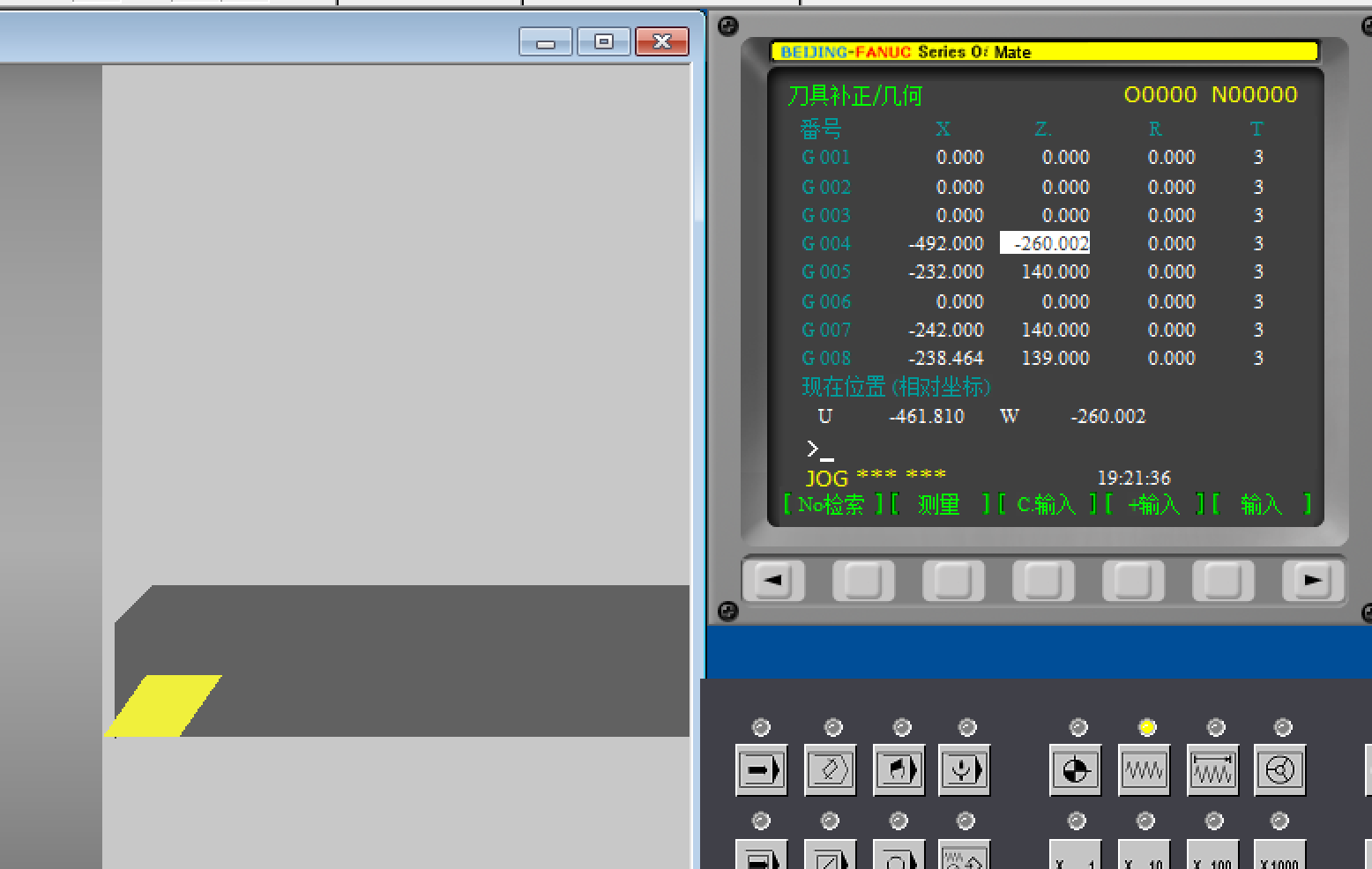
⑤4号刀对刀完毕,将刀架移开,退至换刀位置附近。
5)T0505 内切槽刀(5号刀)对刀。
①在MDI方式下,调5号刀,按[主轴正转]按钮,使主轴旋转。
②在手动方式下,将刀具移至工件附近,越近时倍率要越小,使5号刀的左刀尖(刀位点)与已加工好的工件端面平齐,并接触工件的内孔,听见摩擦声或有微小铁屑。
③在刀偏表中,光标移至刀编号为0005的试切直径和试切长度处,键盘分别输入对应的Z0和X30.19的数值,然后按[Enter]键,使主轴停止,完成5号刀Z向和X向对刀。
④完成2号刀对刀后,刀架移开,退到换刀位置,使主轴停转。
5号刀对刀如图3.1.21所示。
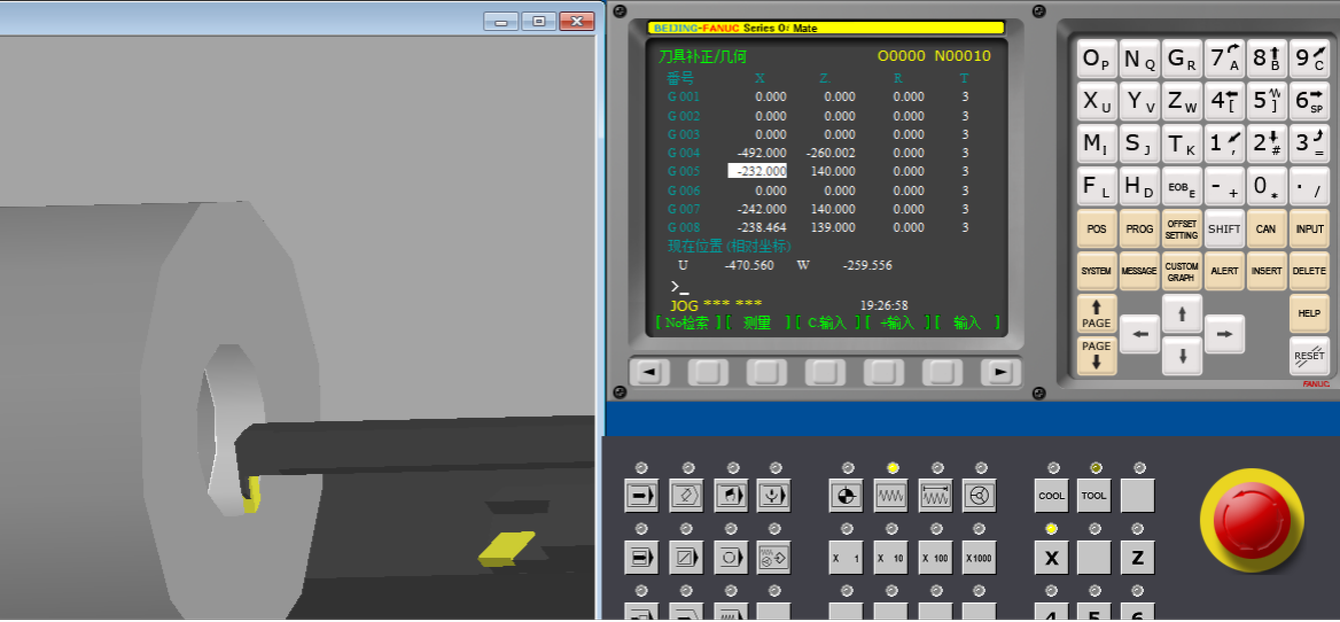
6)T0606 内螺纹刀(6号刀)对刀。
①在MDI方式下,调6号刀,按[主轴正转]按钮,使主轴旋转。
②在手动状态下将刀具移至工件附近,越近时倍率要越小,使6号刀的刀尖与已加工好的工件端面平齐,并接触工件的外圆,听见摩擦声或有微小铁屑。
③在刀偏表中,光标移至刀编号为0006的试切直径和试切长度处,键盘分别输入对应的Z0和X30.19的数值,然后按[Enter]键,使主轴停止,完成6号刀Z向和X向对刀。
④刀架移开,退到换刀位置,主轴停转。
6号刀对刀如图3.1.22所示。

评价内容 |
分值 |
自评 |
互评 |
教师评价 |
得分 |
|
---|---|---|---|---|---|---|
工作过程 |
学习态度 |
20 |
||||
通识知识 |
20 |
|||||
关键能力 |
20 |
|||||
工作成果 |
成果质量 |
40 |
||||
合计 |
2.学会了数控车床的数控坐标系、基本指令、模拟仿真软件的使用方法及对刀的方法;掌握了熟练使用模拟仿真软件的能力;掌握了数控车床手动操作与对刀的能力;提高了学生的团队合作、与人交流、7S管理、质量意识、安全意识等综合素质的提高。
3.对教学资源需要进行及时更新,不断补充、完善数字教学资源,对团队教学资源进行整合,提升教学资源利用效率。