素质目标:具备正确的爱国主义价值观;具备自学能力、创新能力;具备吃苦耐劳、精益求精、追求卓越的工匠精神;具备良好的团队协作精神、与人交流能力;具备的安全意识、绿色环保意识、7S管理意识、质量意识和节约意识。
知识目标:掌握制定球头轴零件的加工工艺规程的方法; 掌握G02、G03指令格式、含义、编程方法。
能力目标:会进行球头轴图样分析,能制定球头轴零件的加工工艺规程;能正确编制球头轴零件的数控车削的加工程序,并能进行模拟仿真加工及调试;能正确进行仿真模拟加工,能操作数控车床加工出合格的球头轴零件。
学生在网上搜查学习资料,通过自主学习,小组合作完成课前自学任务,并上传到班级课程网站作业专栏。在完成学习任务的过程中,对于相关知识的欠缺,也可在智慧职教资源库中搜查相关课程资源,进行自主学习与弥补。
学生以企业编程员的身份接受零件的仿真任务,并能够独立完成从零件加工程序的输入-安装工件和刀具-选择对刀基准工具-设置工件坐标系-零件仿真-工件测量全过程的操作。从而检验零件加工程序编制的正确性。如图5.1.1所示。
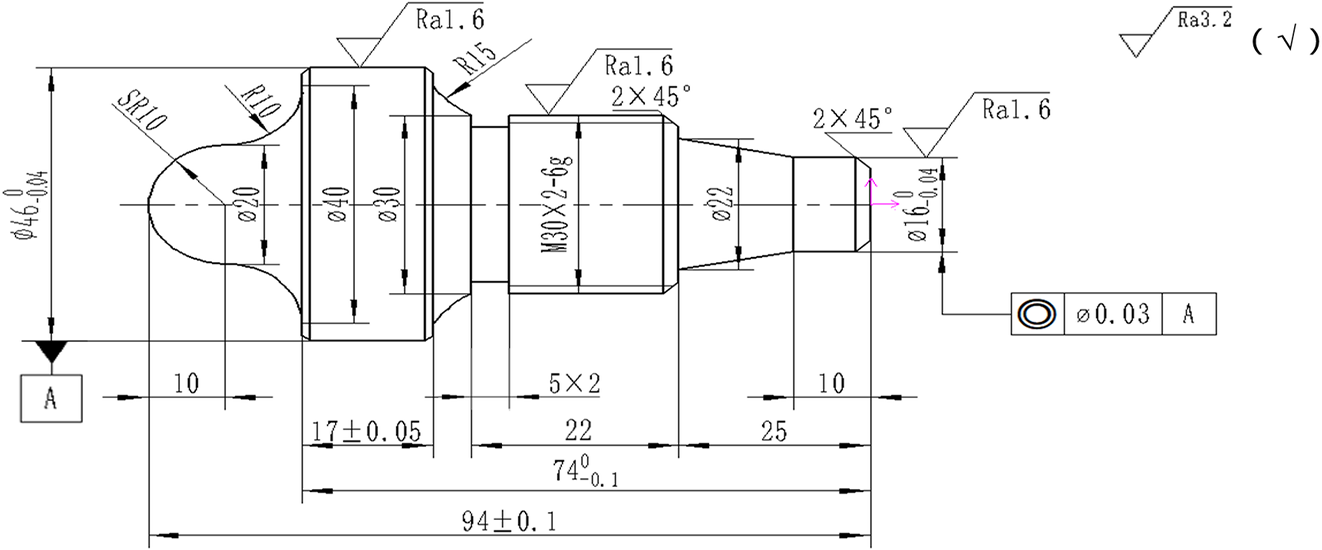
综合轴零件的效果图如图5.1.2所示。
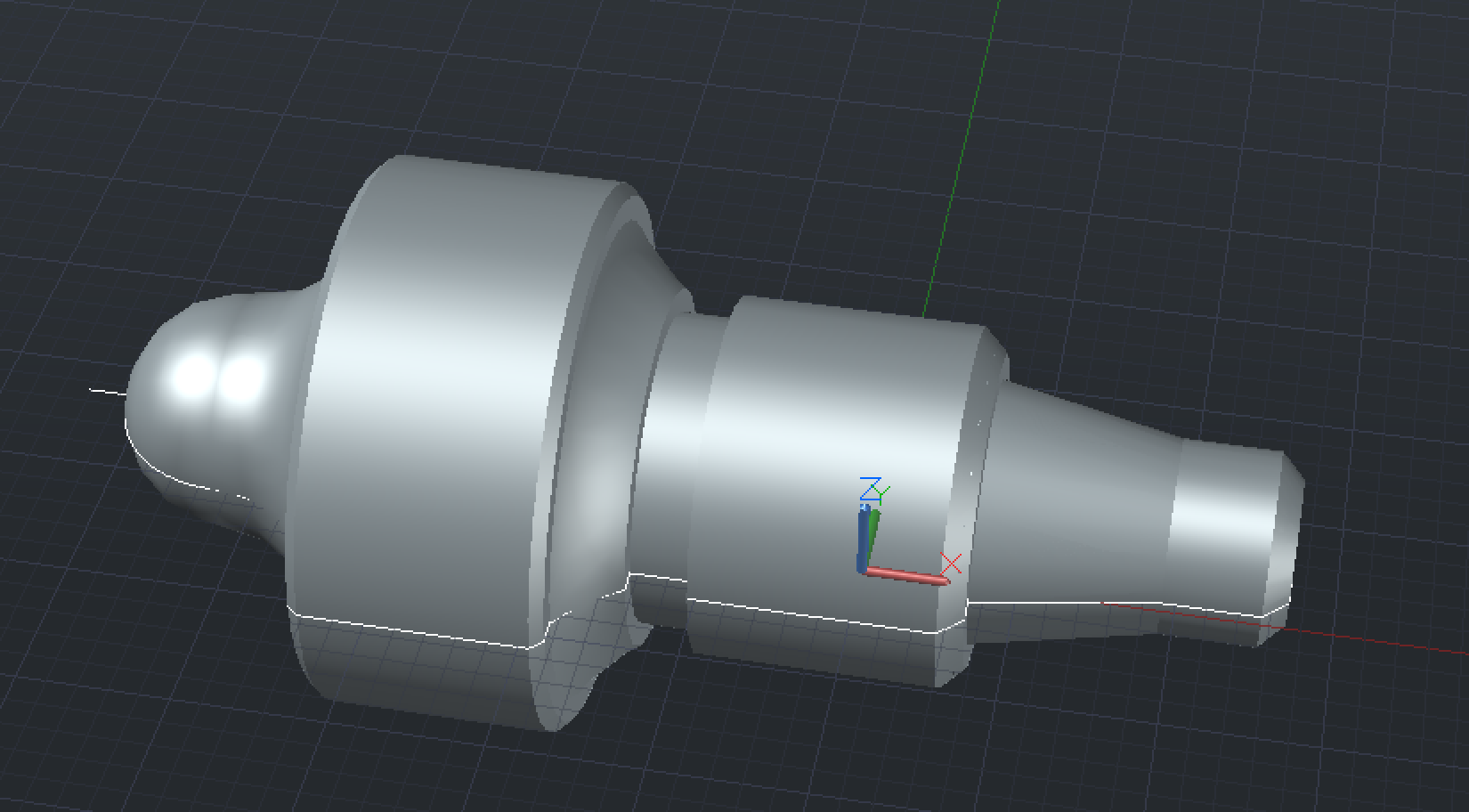
一、加工分析
(一)识读图样
1.加工内容
2.加工精度
由图可知,Φ16及Φ46外圆柱面尺寸精度较高,公差为0.04;M30×2外螺纹面精度较高,公差等级为IT6级,基本偏差为g;外圆锥面小端Φ16大端面Φ22;外沟槽面宽度为5,深度为2;外圆弧面半径尺寸为R15和R10;球面尺寸为SR10;外圆锥面、外沟槽面、外圆弧面及球面尺寸精度为一般公差,精度较低。
(二)加工方案
根据图样分析,图中无倒锥及深凹槽面,可选用80°菱形刀片外圆车刀加工图中外轮廓部分;外沟槽受槽宽的限制,选用5mm宽的外槽刀具。外螺纹是国标60度的标准螺纹,选用标准螺纹车刀,螺距为2mm的外螺纹车刀。导杆厚度受机床参数影响,根据机床参数选取导杆厚度,一般导杆有20mm和25mm厚度。
(三)量 具
通过图样分析,公差在0.02mm,使用精度为0.01外径千分尺测量能够满足要求,长度使用精度为0.02游标卡尺能够满足要求;使用M30×2-6H的螺纹环规检测螺纹尺寸;糙度测量需使用粗糙度测量仪检测或样板进行比对。
(四)夹 具
通过图样分析,此毛坯为棒料,因此选用三爪自定心卡盘进行装夹,在保证加工有效长度的前提下,夹持尽可能长的夹持长度,以保证零件的加工刚性。如图5.1.3所示。
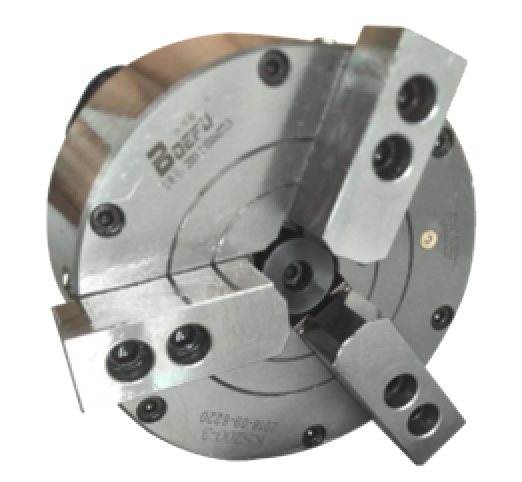
(五)刀 具
根据图样分析,图中无倒锥及深凹槽面,可选用80°菱形刀片外圆车刀加工图中外轮廓部分;外沟槽受槽宽的限制,选用5mm宽的外槽刀具。外螺纹是国标60度的标准螺纹,选用标准螺纹车刀,螺距为2mm的外螺纹车刀。导杆厚度受机床参数影响,根据机床参数选取导杆厚度,一般导杆有20mm和25mm厚度。如图5.1.4所示。
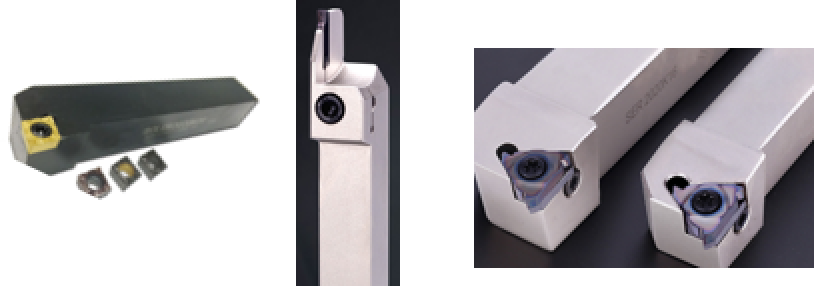
二、程序编制
本零件图纸为综合图形零件,初学者根据零件图纸可采用手动编程和自动编程的方式,不论哪一种编程方法,都需要按照工艺安排找准零件零点和编程基点坐标。
(一)计算基点坐标
1.编程原点
工序20:选取工件左端面的中心点O左为编程原点。
工序30:选取工件右端面的中心点O右为编程原点。
2.基点坐标
根据综合轴零件图,找出各个基点,再根据各工序确定出对应基点坐标值,如图5.1.5所示。
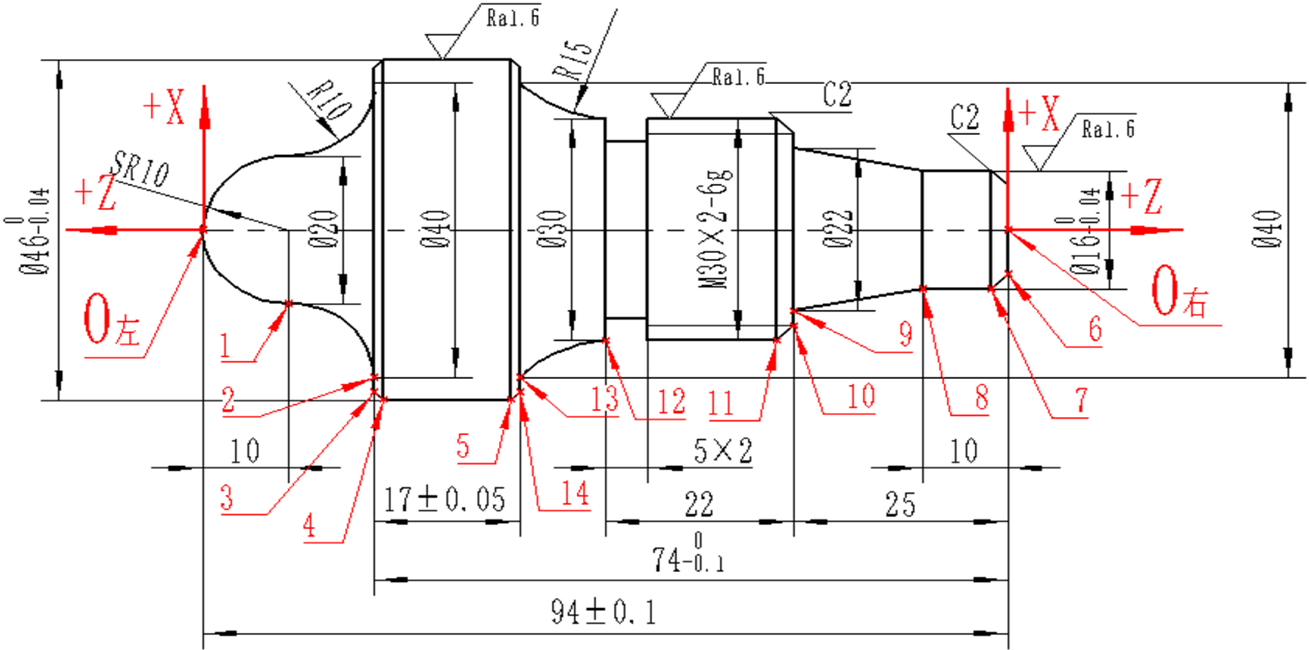
(二)编写程序
O1000 程序格式
T0101 刀具指令T。
M03 S500 主轴控制指令M,主轴转速指令S。
G00 X100 Z100 快速进给指令G00,保证换刀不发生碰撞的点。
G00 X52 Z5
G71 U2 R1 数控车内外径粗车循环指令G71。
G71 P10 Q20 U0.5 W0.1 F0.2
N10 G00 X0
G01 X0 Z0 F0.1 直线插补指令G01。
G03 X20 Z-10 R10 F0.05 圆弧插补指令G03。
G02 X40 Z-20 R10
G01 X44
X46 Z-21 F0.1
Z-40 经工艺分析,调整5点Z坐标值,避免出现接刀痕迹。
N20 G01 X52
G00 Z5
X100 Z100 M05
M00 程序停止指令。
T0101
M03 S1000
G00 X52 Z5
G70 P10 Q20 数控车内外径精车循环指令G70。
G00 X100 Z100 M05
M30 程序结束指令。
加工程序
O2000
T0101
M03 S500
G00 X100 Z100
X52 Z5
G71 U2 R1
G71 P10 Q20 U0.5 W0.1 F0.2
N10 G00 X2 Z5 经工艺分析,进刀点应设在倒角延长线上,经过6点,可避免出现棱边。
G01 X16 Z-2 F0.1
Z-10
X22 Z-25
X26
X30 Z-27
Z-47
G02 X40 Z-57 R15 F0.05
G01 X44 F0.1
X48 Z-59 退刀点 经工艺分析,退刀点应设在倒角延长线上,经过5点,可避免出现棱边。
N20 G01 X52
G00 Z5
X100 Z100 M05
M30
加工程序
O2100
T0202 刀具指令,换2号刀具。
M03S500
G00 X100 Z100
X52 Z5
Z-47 定位到切槽点,需考虑刀宽及刀位点。
G01 X26 F0.05 切槽加工。
X52 F0.5 退出沟槽点。
G00 Z5
X100 Z100 M05
M30
加工程序
O2200
T0303 刀具指令,换3号刀具。
M03 S500
G00 X100 Z100
X35 Z5 螺纹循环点。
G92 X29.1 Z-45 F2 第一次牙底点 螺纹车削简单循环指令。
X28.5 第二次牙底点。
X27.9 第三次牙底点。
X27.5 第四次牙底点。
X27.4 最终牙底点。
G00 X100 Z100 M05
M30
三、仿真加工
(一)加工前准备工作
1.选择机床与系统
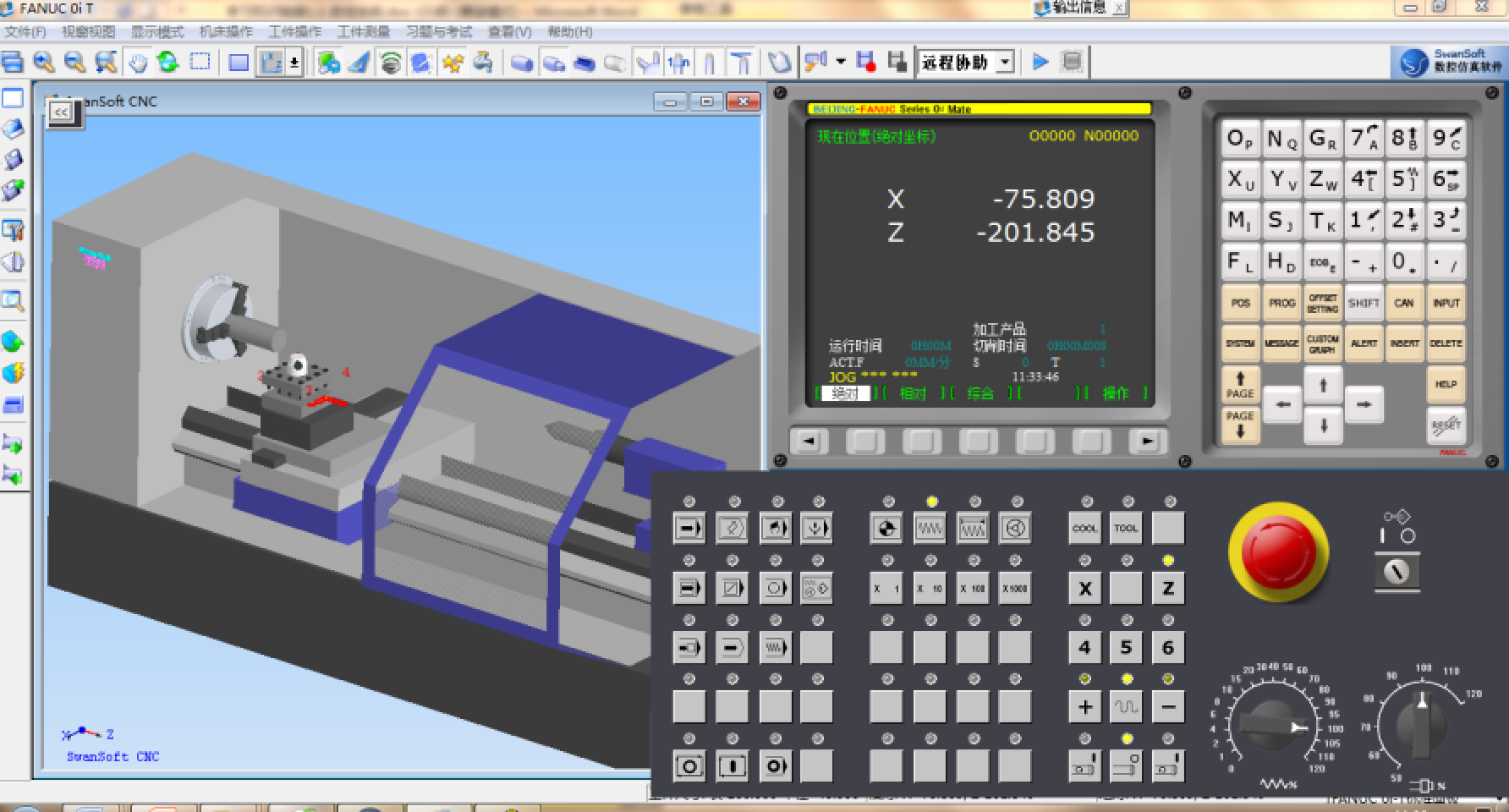
2.回 零
机床为了保证更高的加工精度,通常在通电后需要回零点,但并不是每台机床必要的操作,根据厂家不同,是否回零要参照机床使用说明书。如图5.1.7所示。

3.刀具选择
进入数控加工仿真系统,在工艺流程主菜单进入车刀刀库子菜单下选择各种刀具,并设置刀具相应各参数如图所示,然后选择确定按钮,就可以将各把车刀装在刀架上。刀具库管理对话框如图5.1.8所示。
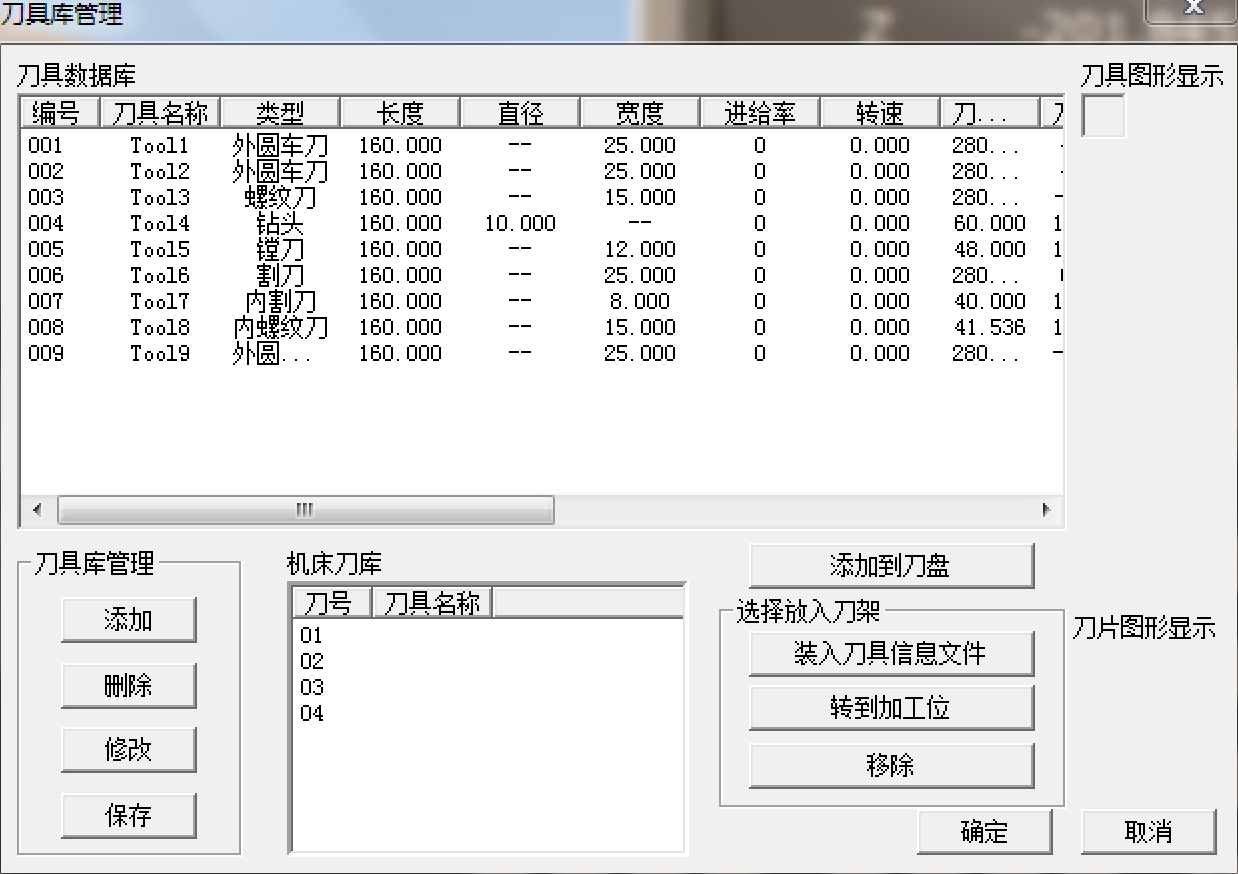
修改刀具对话框如图5.1.9所示。在此可以修改刀具相关参数,以满足使用要求。
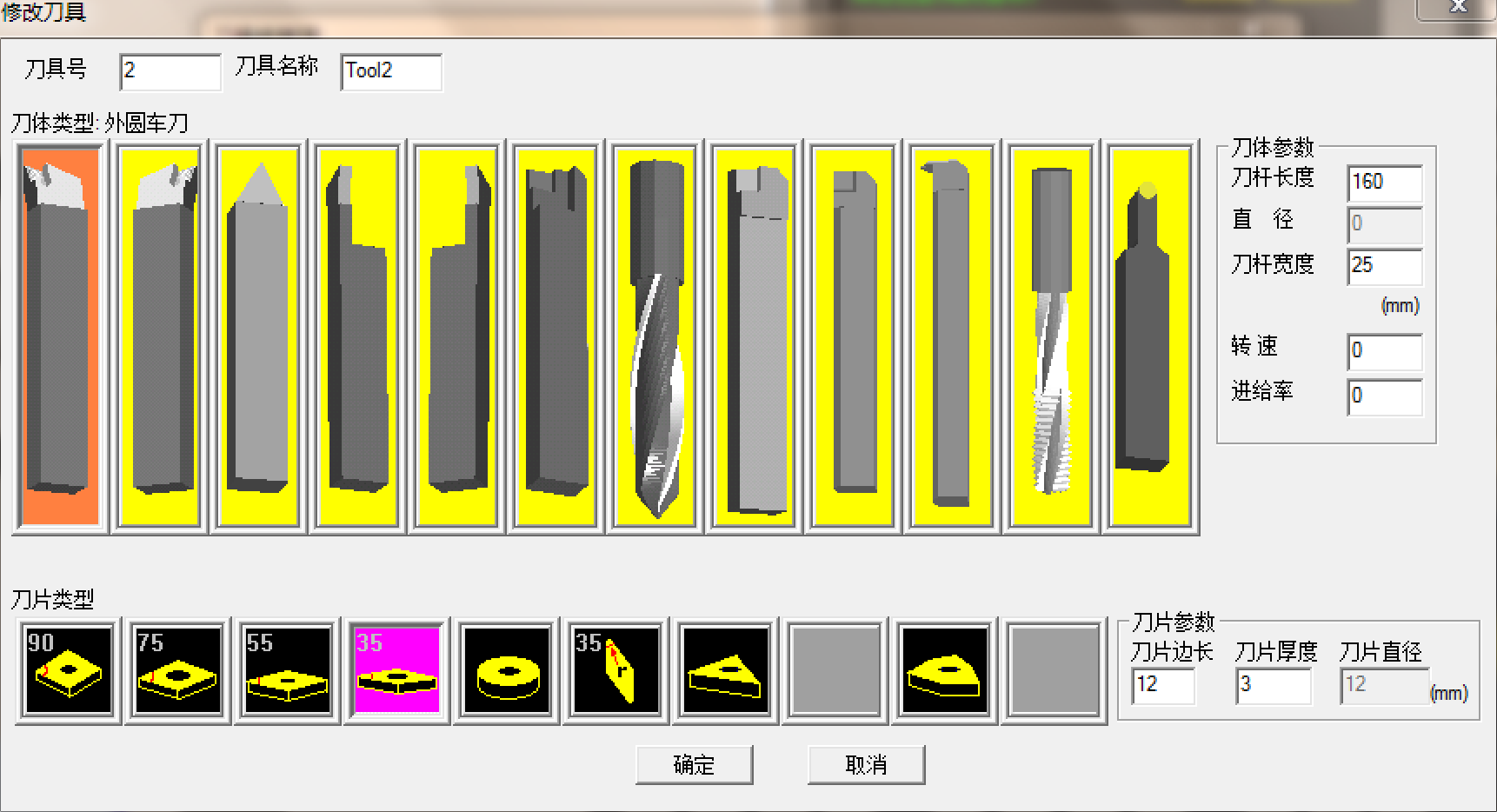
刀具选择与修改完成后,按照刀位安装到机床刀架上,刀架安装后如图5.1.10所示。
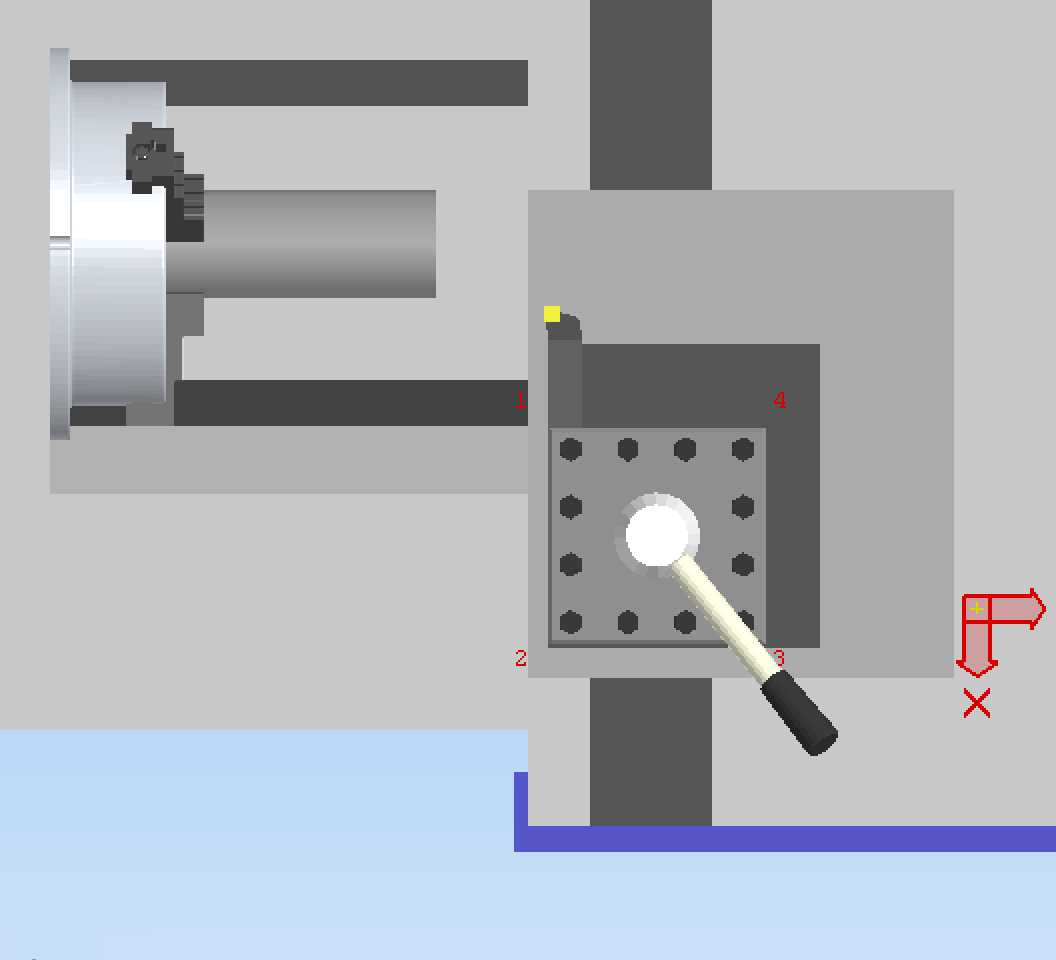
4.毛坯选择
进入数控加工仿真系统,在工艺流程主菜单进入选择毛坯子菜单下按下新毛坯按钮,选择毛坯外径、内径、高、材料和夹具如图5.1.11所示,然后按确定按钮,再选择安装此毛坯即可将该毛坯装在卡盘上,最后调整伸出长度后加紧。
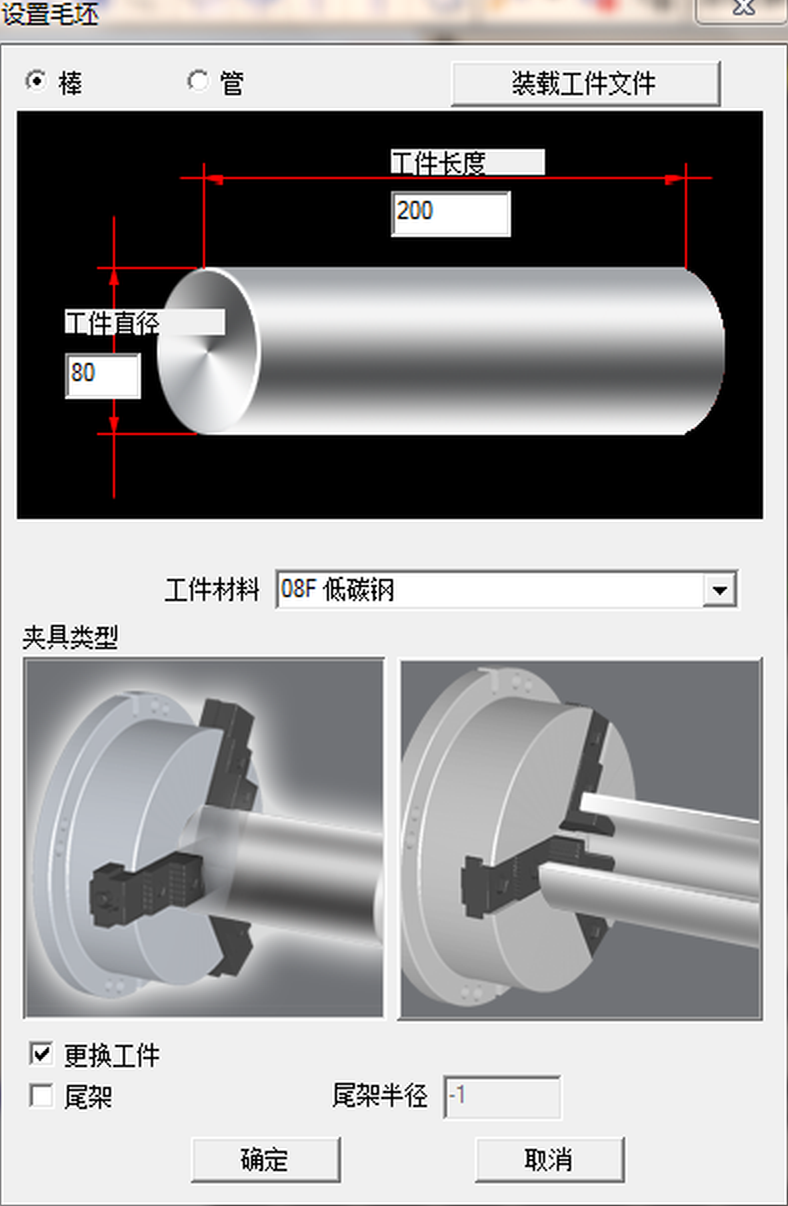
5.导入程序
分别将程序导入到仿真软件中,注意要在“编辑”状态下,方可导入程序。选择“PROG”,新建程序名称,以字母O开头的四位数字。如图5.1.12所示。
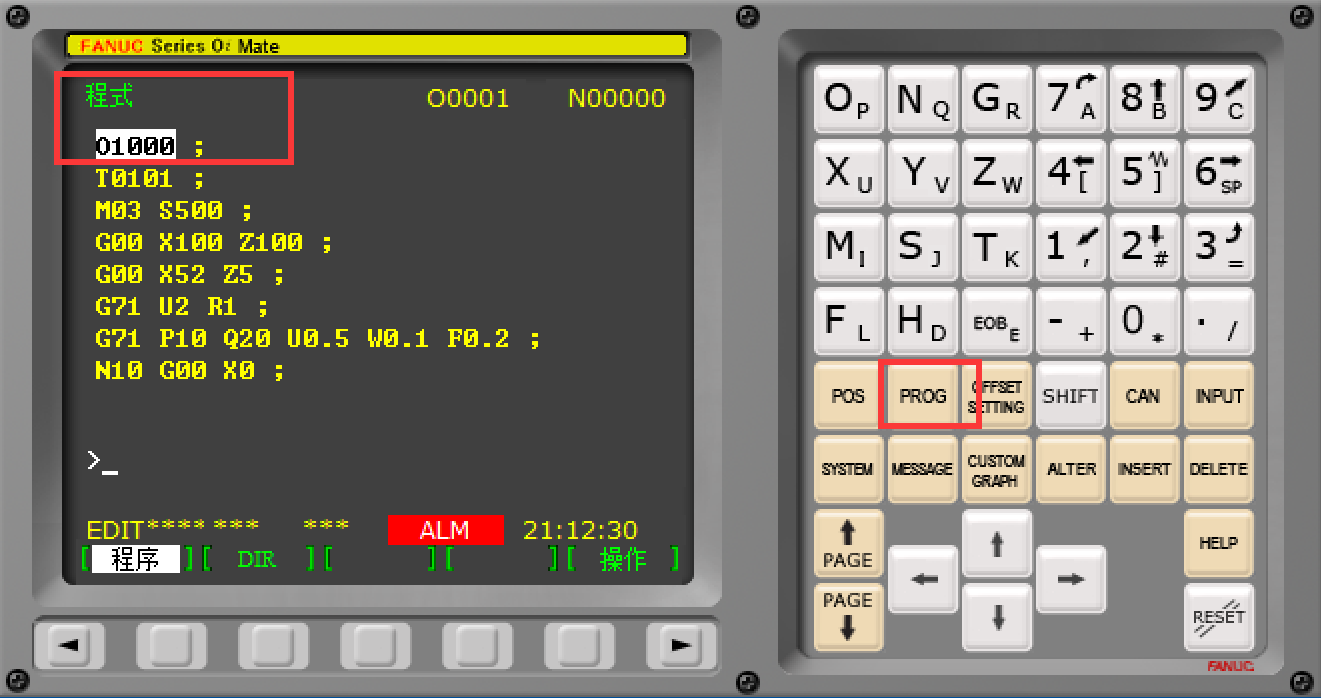
6.循环启动
调整好零件和程序后,点击“自动加工”,设置进给倍率和主轴倍率,点击“循环启动”,注意时刻观察工件的加工状态,遇到问题按下“进给保持”。如图5.1.13所示。
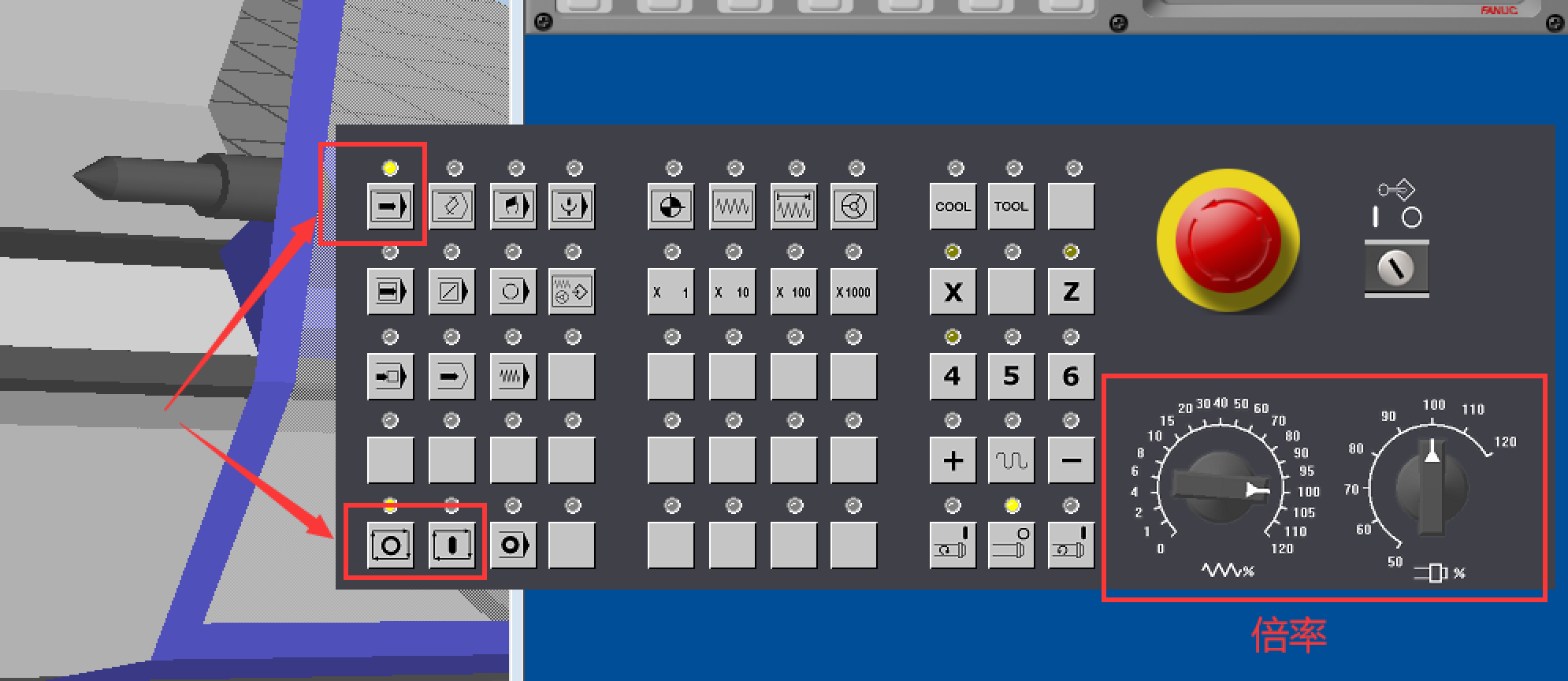
四、实际加工
实际加工与仿真加工还是有所区别的,就加工环境、设备情况、刀具情况等都有所不同,操作者要时刻观察机床加工状态,严格按照7S管理执行。
评价内容 |
分值 |
自评 |
互评 |
教师评价 |
得分 |
|
---|---|---|---|---|---|---|
工作过程 |
学习态度 |
20 |
||||
通识知识 |
20 |
|||||
关键能力 |
20 |
|||||
工作成果 |
成果质量 |
40 |
||||
合计 |
2.“精益求精的大国工匠精神”贯穿教学全过程,切实做到了对学生素质目标的培养。
3.学生在完成任务的过程,鼓励学生担当不同的角色,利用角色扮演法,增强学生的工作责任心,增强小组成员间的协作能力,组织能力和管理能力,调动学生的积极性,充分体现以学生为主体的教学特点。
4.学生对零件编程与加工的具体操作还有待于进一步优化,以便提高加工效率,提高加工质量。